From food packaging to industrial applications, plastic film plays an integral role in modern packaging. Its versatility, strength, and flexibility make it a top choice for businesses seeking reliable packaging solutions. Among the many types of plastic films available, High-Density Polyethylene (HDPE) is a preferred option for its unique properties and wide range of applications.
This article explores the key benefits of HDPE and its uses across industries. We’ll also discuss why manufacturers prefer HDPE and how to choose a reliable HDPE supplier.
What Is HDPE?
High-Density Polyethylene (HDPE) is a dependable and versatile material revolutionizing the packaging industry. Celebrated for its strength, flexibility, and cost-effectiveness, HDPE offers a unique combination of durability and lightweight design—making it suitable for varied applications. Whether protecting food products, medical equipment, or industrial goods, HDPE steadily gains prominence as a go-to solution.
One factor that sets HDPE apart is its adaptability to advanced manufacturing processes like blown film extrusion, where molten polymer is formed into films through a controlled flow of air. This approach can create precise packaging films for different uses, supporting efficient production and consistent quality. From industrial to medical packaging needs, HDPE’s versatility continues to expand its reach across different sectors.
Unique Properties of HDPE
High-Density Polyethylene (HDPE) has specific characteristics that cater to businesses looking for high-performance packaging materials. Some of its standout features include:
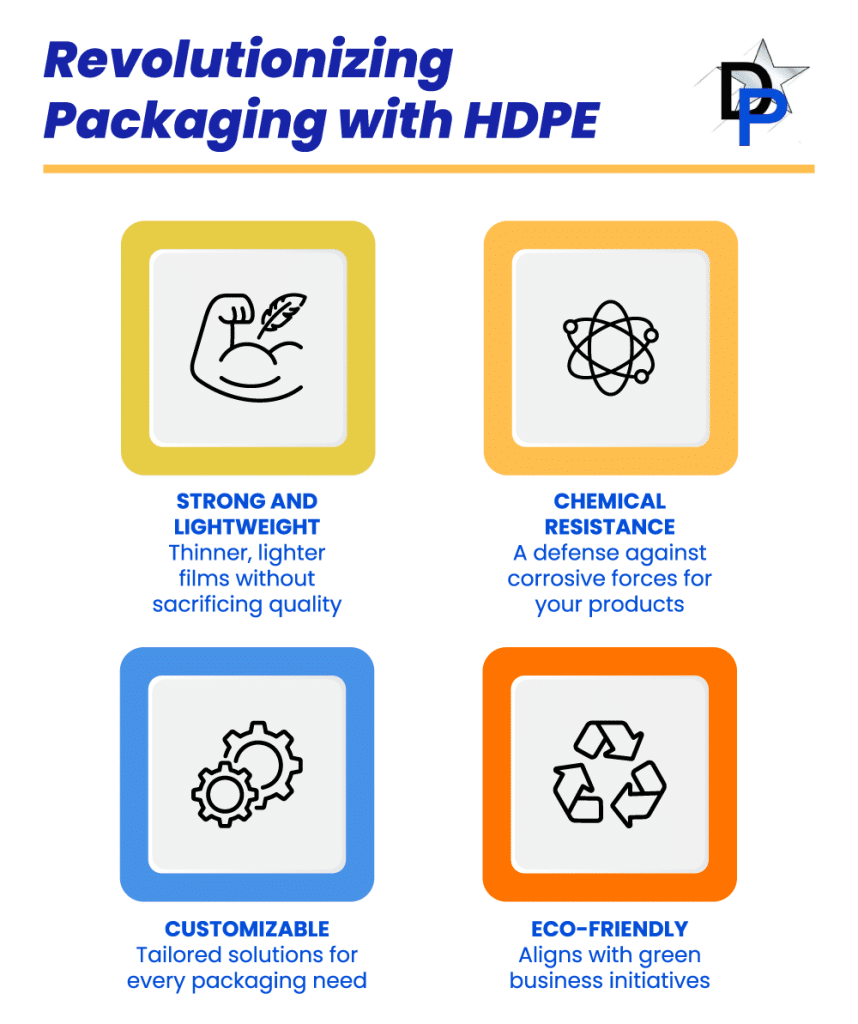
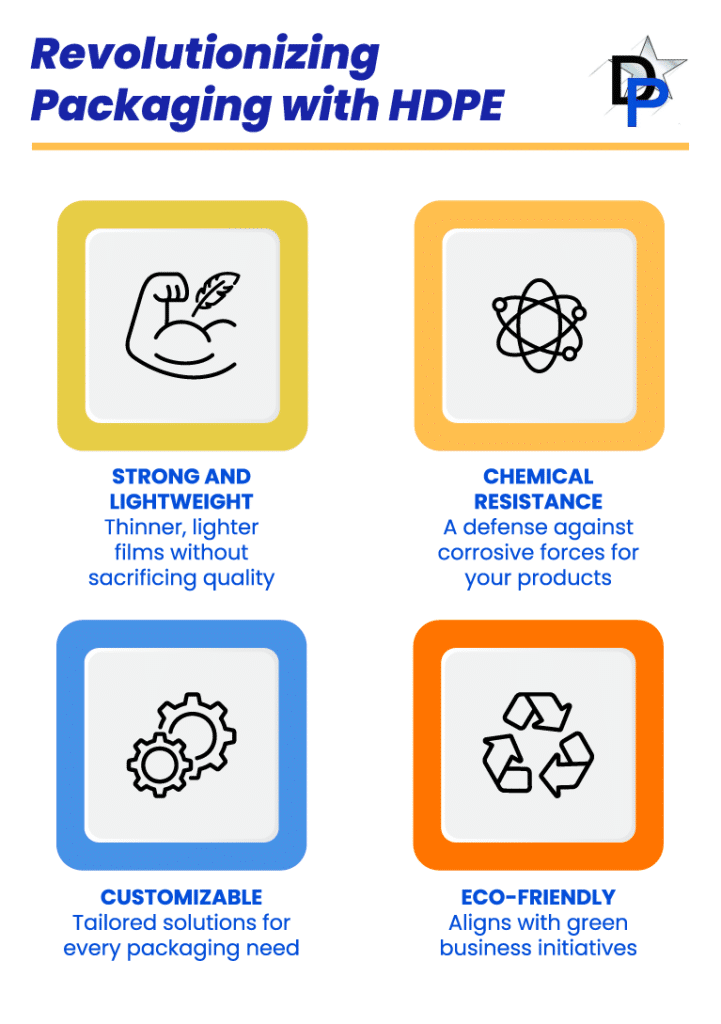
Strength Meets Lightweight Design
HDPE has an impressive strength-to-weight ratio, allowing manufacturers to create thinner, lighter films without sacrificing structural integrity. This not only reduces material usage but can also lower transportation costs by cutting down on bulk and weight.
Chemical Resistance for Product Integrity
HDPE’s strong resistance to chemicals helps shield products from contamination or degradation. This feature is particularly pivotal for applications in medical settings, industrial packaging, and food storage where product safety is paramount.
Versatile for Customization and Processing
HDPE can be tailored to precise requirements, whether that involves specialized resin blends, unique color or clarity levels, or specific dimensional needs. Its flexibility benefits clients seeking films made to precise standards for varied packaging applications.
Sustainability and Recyclability
As an eco-friendly material with potential for recycling—depending on applicable infrastructure—HDPE can help businesses reduce environmental impact. Properly managed recycling initiatives and closed-loop programs can extend the usefulness of HDPE, aligning with many companies’ sustainability goals.
Benefits of HDPE: Why Industries Prefer It
HDPE stands out for its reliability and performance across industries. Below are some of the benefits that reinforce HDPE’s role in modern packaging:
- Durability: It resists everyday wear, impacts, and environmental stressors like moisture or moderate temperature swings.
- Reduced Downtime and Costs: Fewer replacements, minimal repairs, and lower weight all contribute to cost-effectiveness over time.
- Moisture Resistance: HDPE’s moisture barrier properties protect food products, pharmaceuticals, and other moisture-sensitive items from spoilage and degradation.
- Food-Safe Design: As an FDA-approved material, HDPE is a preferred choice for food packaging that meets regulatory standards.
- Consistent Quality: HDPE’s uniform thickness and durability lead to reliable production outcomes with fewer defects.
- Reduced Product Loss: HDPE’s strength and resistance to environmental elements safeguard packaged goods from damage and loss.
- Ease of Processing: HDPE’s lightweight design and compatibility with automated packaging processes help streamline production.
- Excellent Barrier Properties: HDPE’s barrier properties help shield products from light, oxygen, and other environmental factors.
These attributes ensure that HDPE-based packaging maintains quality and product integrity throughout storage and shipping.
Applications of HDPE Across Industries
High-Density Polyethylene (HDPE) serves a variety of sectors, each having unique requirements around safety, cleanliness, or resilience. Here’s how HDPE fits into vital market segments:
Medical Packaging Films
In the medical sector, pure, uncontaminated packaging is critical. Products like surgical wraps and protective covers for medical tools often rely on HDPE to maintain sterility and withstand exposure to disinfectants. Regulatory compliance also plays a significant role, ensuring patient and worker safety.
Industrial Packaging Solutions
Industrial packaging places a premium on strength and resistance to harsh conditions. HDPE’s robust nature ensures materials and components remain secure during transport or storage. Its chemical resistance and durability further shield industrial goods from damage.
Food-Grade Plastic Sheeting
HDPE is favored in the food industry due to its moisture barrier properties and non-reactive composition. Food products packaged using HDPE maintain freshness and avoid odor absorption, thus supporting extended shelf life and safety.
Specialty Applications and FF&S Technology
Advanced Form, Fill, and Seal (FFS) technology benefits from HDPE’s consistency, enabling automated packaging lines to run smoothly. HDPE can be engineered for narrow tubing, high-strength films, and more, offering specialized solutions for niche applications.
Solutions for Converters
Converters play an essential role in the packaging ecosystem. Converters require robust, consistent supplies of HDPE films that can handle a range of packaging demands—from large-scale production runs to specialty applications. Dallas Plastics addresses these needs with converter-grade sheeting optimized for lamination, printing, or other converting processes. By delivering uniform thickness and custom formulations, the company ensures reliable performance and compatibility with modern equipment.
Request a Quote
Why HDPE Is the Ideal Choice for Manufacturers
Manufacturers across diverse sectors often select HDPE for multiple reasons:
- Consistent Production Results: HDPE’s uniform thickness and durability lead to less waste and reliable outcomes in large runs.
- Compatibility with Modern Machinery: Its adaptable properties suit advanced manufacturing systems that value efficiency.
- Cost-Effective Processes: Reduced downtime and straightforward processing help preserve margins.
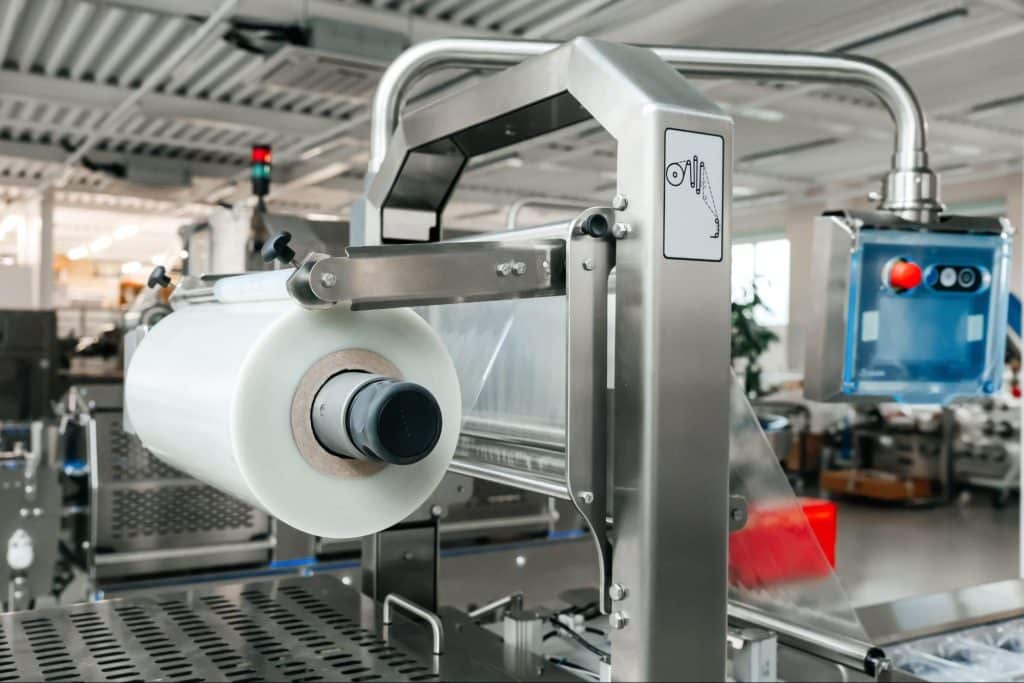
Potential Limitations of HDPE
While HDPE offers numerous advantages, it is important to understand its potential drawbacks:
- Temperature Constraints: At very low temperatures, HDPE can become brittle. Conversely, in high-heat environments, it may soften or warp if used beyond recommended temperature ranges.
- Recycling Challenges: Although HDPE is recyclable, local recycling capabilities vary. Without proper infrastructure, disposal can be complicated, and the material may end up in landfills.
- Not Biodegradable: As a petroleum-based plastic, HDPE does not naturally break down in the environment. Businesses concerned with long-term sustainability should explore organized recycling programs or seek formulations that integrate recycled content.
- Potential Cost Fluctuations: Resin prices can shift over time, especially when influenced by raw material availability or changes in oil markets. Planning and budgeting processes must remain flexible to account for these variations.
Despite these challenges, ongoing innovations in resin formulations, processing techniques, and recycling initiatives continue to address many of these concerns. Choosing a well-qualified supplier can help mitigate limitations by guiding packaging designs, selecting the best resin blends, and advising on proper handling or disposal methods.
How to Choose a Reliable HDPE Film Partner
A capable partner for HDPE films ensures that packaging meets both performance and regulatory demands. Below are key considerations when selecting your HDPE film supplier:
cGMP Compliance for Quality Assurance
A supplier adhering to current Good Manufacturing Practices (cGMP) aligns with stringent production standards. This is essential for sensitive sectors like healthcare and food packaging.
Advanced Technological Capabilities
Look for service providers employing cutting-edge methods like lamination or specialized printing. This enhances film versatility and opens avenues for more elaborate packaging solutions tailored to your specifications.
Customization Flexibility
Your HDPE partner should offer solutions—like unique resin blends and custom film sizes—that address your specialized needs. A willingness to adapt, rather than provide generic solutions, is crucial.
Demonstrated Experience and Reputation
Seasoned suppliers can navigate complex requirements, ensuring consistent quality. Seek those who have proven success across industries, from medical to industrial packaging.
Transparent Communication and Reliability
Reliable timelines, open reporting, and proactive updates foster a positive and productive partnership. Clear communication helps both parties address potential challenges quickly.
Dallas Plastics’ Leadership in HDPE Film Production
Dallas Plastics brings over three decades of experience in blown film manufacturing, making it a trusted source for high-quality HDPE solutions. With multiple facilities and a commitment to quality standards, the company continually meets rigorous demands for food-grade, medical, and industrial applications.
Customers benefit from capabilities such as multi-layer coextrusion for advanced barrier properties and flexographic printing for branding or regulatory text. Dallas Plastics addresses these needs with converter-grade sheeting optimized for lamination, printing, or other converting processes. By delivering uniform thickness and custom formulations, the company ensures reliable performance and compatibility with modern equipment.
HDPE: A Versatile Choice Shaping the Future of Packaging
High-Density Polyethylene (HDPE) continues to shape modern packaging with its impressive blend of durability, adaptability, and cost-effectiveness. Its performance across medical, industrial, and food-related applications demonstrates why so many businesses rely on HDPE to secure their products in transit and on the shelf.
If you’re seeking dependable HDPE film solutions, look no further than Dallas Plastics. Leveraging over 35 years of specialized industry expertise, Dallas Plastics is ready to help you optimize your packaging processes and support your business growth. Partner with a trusted expert committed to innovation, quality, and customer satisfaction.