In the ever-evolving landscape of the plastic packaging industry, understanding the nuanced differences between Low-Density Polyethylene (LDPE) and High-Density Polyethylene (HDPE) films is crucial for professionals tasked with making informed material selections. These two types of polyethylene films, while similar in name, exhibit distinct properties and functionalities that make them suitable for diverse packaging applications.
This blog post will investigate the composition, applications, and advantages of LDPE and HDPE films, highlighting how Dallas Plastics harnesses these materials to produce superior packaging solutions tailored to meet the specific needs of the medical, industrial, and food and beverage sectors. Let’s explore the integral roles these specialty plastic films play in delivering quality and efficiency in packaging solutions.
Properties of LDPE and HDPE Films
Low-density polyethylene (LDPE) and high-density polyethylene (HDPE) films are two staples in the plastic packaging industry, each possessing unique characteristics that make them suitable for different applications. By understanding their properties, professionals can make informed choices that align with their specific packaging needs.
Composition and Structural Differences
The primary distinction between LDPE and HDPE lies in their molecular structures. LDPE is characterized by its branched chain configuration, which results in a loose, flexible material structure. This branching prevents the polymer chains from packing closely, leading to a lower density and softer texture. In contrast, HDPE features a linear molecular structure that allows the chains to pack tightly together, resulting in stronger intermolecular forces and a higher density material.
Density Variations and Impact on Material Behavior
Due to their structural differences, LDPE and HDPE films also differ in density. LDPE typically has a density range of 0.910-0.940 g/cm³, whereas HDPE has a density of 0.941-0.965 g/cm³. This variation significantly influences the behavior of the materials under various conditions. LDPE’s lower density translates into higher ductility and less rigidity, making it more suitable for applications requiring flexibility. Conversely, HDPE’s higher density contributes to its greater tensile strength and rigidity, making it ideal for more demanding applications.
Flexibility and Tensile Strength Comparisons
LDPE films are renowned for their exceptional flexibility but tend to have lower tensile strength compared to HDPE films. This makes LDPE films an excellent option for products that need to be packaged gently and with flexibility but without the necessity for high strength. HDPE films, on the other hand, offer robust resistance to tearing and perform well in applications where durability is crucial.
Understanding these key properties helps industry professionals to tailor their packaging strategies according to the specific strengths and limitations of each material, ultimately optimizing performance and cost-effectiveness.
Common Applications of LDPE Films
Low-Density Polyethylene (LDPE) films boast a range of applications within the plastic packaging industry, their unique properties making them ideally suited for specific uses. Here, we explore the most common applications of LDPE films, highlighting where they’re most effectively implemented.
Lightweight Product Packaging
LDPE films are particularly valued in the packaging of lightweight items. Their inherent flexibility and resilience make them an excellent choice for consumer goods that require a gentle touch, protecting items such as textiles, paper goods, and perishable items from moisture and dirt.
Shrink Film Applications
Another prominent use of LDPE films is in shrink film which benefits from LDPE’s elasticity which allows the film to tightly conform to the contours of an item, providing a secure hold without compromising the integrity of the packaging. This ability not only ensures the stability of goods during transport but also preserves their freshness and extends shelf life.
Medical Packaging
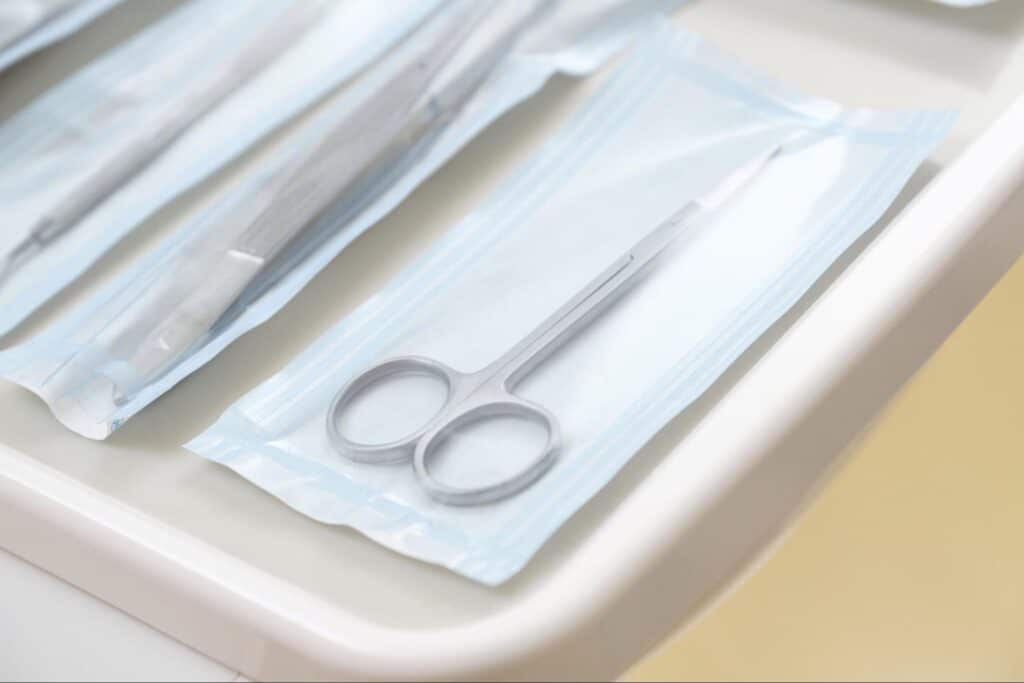
In the medical sector, the transparency and flexibility of LDPE films are invaluable. These properties contribute to producing sterile, see-through bags and wraps that protect medical devices and pharmaceuticals. LDPE films are preferred for these applications because they are less reactive with other materials and can be sterilized, ensuring safety and compliance with health regulations.
LDPE’s versatility and benign chemical nature make it a frontline choice for numerous demanding applications, confirming its integral role in the modern packaging landscape. Each of these uses demonstrates the film’s adaptability and reliability, key factors for industries that prioritize both protective qualities and clarity in packaging solutions.
Common Applications of HDPE Films
High-Density Polyethylene (HDPE) films are recognized for their robust performance in various packaging scenarios, thanks to their strength and durability. These films are optimal for sectors demanding high resilience and protective properties in their packaging materials.
Use in Industrial Packaging
HDPE’s rigidity and strength make it a preferred choice for industrial packaging needs. Its toughness helps in safeguarding products during transportation and storage, effectively reducing damage risks. Items typically packaged with HDPE films include large machinery parts, building materials, and bulk chemicals that require a high degree of protection against external environments.
Ideal for Food and Beverage Industry Applications
The food and beverage industry greatly benefits from the use of HDPE films, primarily because of their resistance to chemicals and moisture. This resistance ensures that the packaging does not react chemically with the contents, thus preserving the food’s freshness and shelf life. HDPE films are commonly used in bottling applications, such as milk, water, and juice containers, where hygiene and durability are paramount.
Benefits in Agricultural Films
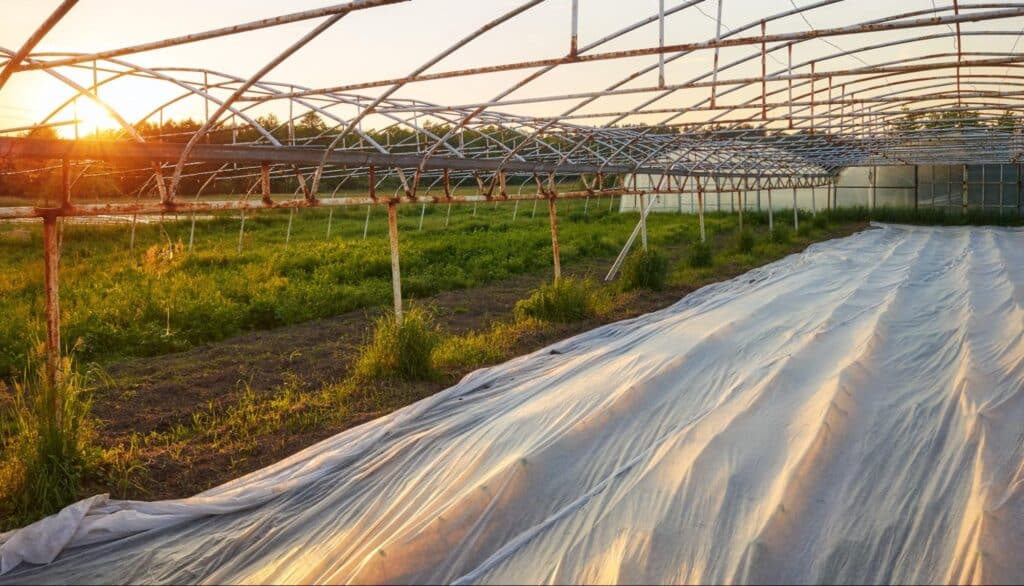
In agriculture, HDPE films are used extensively in applications such as mulch films, greenhouse covers, and soil amendments. The high durability of HDPE is crucial in these applications, where exposure to harsh environmental conditions is common. Its ability to withstand various weather influences, including ultraviolet (UV) radiation, makes it exceptionally suitable for outdoor agricultural uses, contributing to enhanced crop protection and yield improvement.
Each of these applications of HDPE films highlights the material’s adaptability and reliability in meeting the requirements of different industries, making it a versatile player in the realm of plastic packaging solutions.
Advantages of LDPE in Packaging Solutions
Low-Density Polyethylene (LDPE) film offers a range of benefits that make it a preferred choice for specific types of packaging solutions. Its inherent properties cater to sectors where flexibility, clarity, and cost-effectiveness are crucial. Below are some key advantages that LDPE films provide in the packaging industry.
Ease of Processing and Cost-Effectiveness
LDPE is well-regarded for its ease of processing, which directly translates into cost efficiency. This material can be easily molded and extruded, making it suitable for a vast range of product shapes and sizes without significant production costs. It processes at lower temperatures compared to other plastics, which also helps in saving on energy costs during manufacturing. Consequently, LDPE is an economical option for bulk packaging needs.
Superior Clarity for Product Visibility
One of the standout features of LDPE film is its superior clarity. This property is particularly valuable in packaging that necessitates a clear view of the product, such as in food packaging and retail goods. High visibility through the packaging not only enhances product appeal but also aids in quality inspection processes, allowing for easy monitoring of the packaged contents without the need to open the package.
Excellent Sealing Properties
LDPE films exhibit excellent sealing qualities, ensuring that the items inside are well-protected against contaminants and leakage. This sealing capability is essential for maintaining the integrity and shelf life of perishable goods, including food and pharmaceuticals. The solid seals formed by LDPE also contribute to its effectiveness in applications requiring air-tight packaging, like those used in various medical products.
By leveraging these advantages, LDPE films serve as an integral component of packaging solutions that require durability, transparency, and cost efficiency. Whether it’s for consumer goods or sensitive medical equipment, LDPE’s properties make it versatile enough to meet varying packaging demands efficiently.
Advantages of HDPE in Packaging Solutions
HDPE (High-Density Polyethylene) films are favored in the packaging industry due to several inherent advantages that meet the high-demand needs of various sectors.
High Resistance to Chemicals and Moisture
HDPE films are known for their robust resistance to chemicals, making them an excellent choice for packaging products that may be sensitive or reactive to certain substances. This characteristic also extends to a strong moisture barrier, essential for preserving the quality and integrity of items prone to damage from humidity and water exposure.
Better Performance at Higher Temperatures
When compared to other plastics, HDPE films excel in environments that require exposure to higher temperatures. This makes HDPE an ideal material for applications involving sterilization processes or packaging goods that experience thermal exposure during shipping and storage.
More Environmentally Sustainable Options
HDPE is not only durable but also offers more environmentally sustainable options. It is frequently recycled, which helps reduce plastic waste. Companies looking to enhance their environmental stewardship find HDPE appealing for its contributions to eco-friendly initiatives. This alignment with sustainability goals is critical as industries seek to lower their environmental impact without compromising on packaging quality or performance.
Each of these properties positions HDPE films as a top-tier choice for industry professionals demanding high-performance packaging solutions that also support broader environmental objectives.
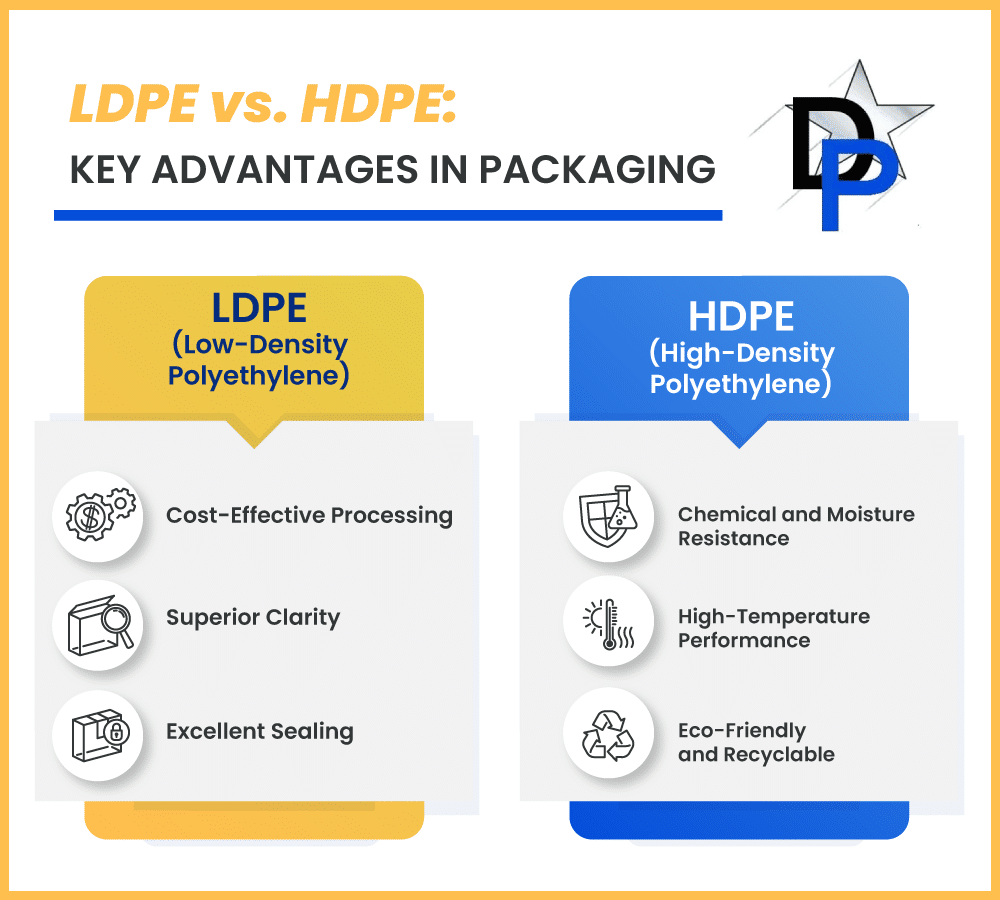
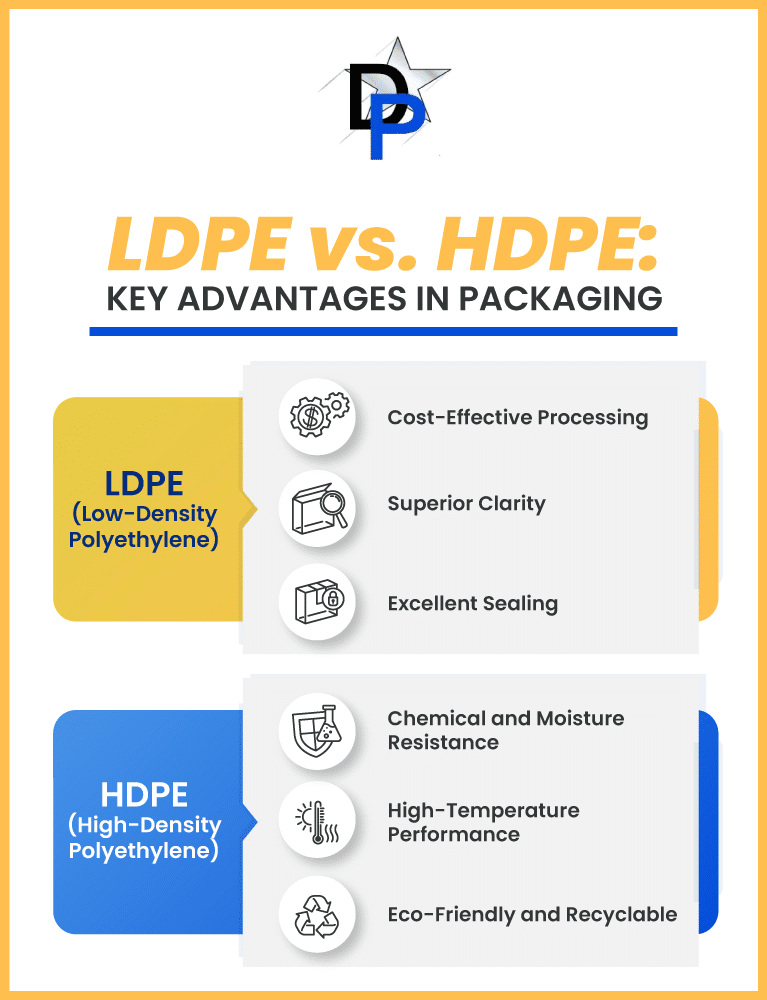
Integration of LDPE and HDPE at Dallas Plastics
Dallas Plastics has long recognized the diverse needs of the plastic packaging industry and has intricately tailored its product offerings to include both LDPE and HDPE films, ensuring a comprehensive range of solutions to meet varied industry demands. Understanding the unique characteristics of these materials allows Dallas Plastics to provide products that precisely align with customer requirements.
Customization Capabilities to Meet Specific Industry Needs
Dallas Plastics excels in customization, making it possible for customers to specify dimensions, thickness, and additives according to their unique specifications. Whether a company is looking for UV protection, anti-static properties, or flame retardants in their plastic films, Dallas Plastics can incorporate these features to produce a product that meets exacting standards and functional requirements.
Overview of Product Offerings Encompassing Both Materials
The range of products at Dallas Plastics includes everything from general-purpose films to highly specialized plastic films designed for specific sectors such as food and beverage, medical, or industrial applications. For LDPE, offerings include highly flexible films suitable for consumer goods packaging, while HDPE films are provided for applications requiring higher tensile strength and barrier protection against moisture and chemicals.
Adherence to cGMP Guidelines for Quality Assurance
Quality remains a cornerstone of Dallas Plastics’ operations. The company strictly adheres to current Good Manufacturing Practices (cGMP), ensuring that each batch of LDPE and HDPE film complies with stringent regulatory standards. This commitment not only results in superior product quality but also enhances reliability and trustworthiness in the eyes of clients concerned with regulatory compliance and product efficacy.
Dallas Plastics’ Expertise in Plastic Film Solutions
Dallas Plastics has positioned itself as a leader in the plastic film industry by not only providing a broad range of LDPE and HDPE film solutions but also through its innovative application of technology and commitment to quality. This expertise is highlighted in their approach to incorporating cutting-edge techniques and maintaining a client-centric service model, which ensures tailored, high-quality outputs for every customer need.
Innovative Use of FF&S Technology
One of the key technological advancements Dallas Plastics leverages is Form-Fill-Seal (FF&S) technology. This method enhances the functionality of packaging by automating the process of forming the bags, filling them with product, and sealing them. This technology significantly improves efficiency in packaging operations and provides consistent quality in the final product. The use of FF&S technology is particularly beneficial in ensuring precise and robust packaging solutions, which are critical in sectors where packaging integrity and durability are paramount.
Service-Oriented Approach with Expert Staff Guidance
Dallas Plastics distinguishes itself through a that emphasizes direct engagement and expert guidance. Their team comprises industry veterans who possess deep knowledge of both materials and their applications.
This expertise enables them to offer valuable insights and recommendations to clients, ensuring that the plastic films provided meet the specific needs of different industries, whether it’s medical, food and beverage, or industrial. By prioritizing customer service, Dallas Plastics ensures a seamless experience from initial consultation through to the delivery and implementation of the plastic films.
Request a Quote
Commitment to Sustainable and High-Quality Product Delivery
Sustainability is a critical aspect of the plastic film industry, and Dallas Plastics is committed to minimizing environmental impact while maintaining product efficacy. By adopting more environmentally friendly practices and continually refining their material usage strategies, they provide sustainable yet effective packaging solutions. This commitment not only reflects the company’s responsibility towards environmental conservation but also appeals to contemporary businesses looking to enhance their eco-friendly practices.
Through rigorous adherence to industry standards and continuous innovation, Dallas Plastics delivers superior plastic film solutions that meet high-quality benchmarks and eco-conscious expectations.
Decision-Making Factors for Choosing Between LDPE and HDPE
Selecting the appropriate type of plastic film, whether LDPE or HDPE, involves careful consideration of several factors. These decisions can significantly impact both the performance and cost-effectiveness of packaging solutions. Understanding these key considerations will enable industry professionals to make informed choices that align with their specific packaging needs.
Considerations of Cost vs Performance
Cost is a major consideration, influencing the choice between LDPE and HDPE films. Typically, LDPE can be slightly less expensive than HDPE due to differences in manufacturing processes and raw material costs. However, the choice isn’t solely about upfront costs; performance factors play a critical role. For instance, while LDPE provides excellent clarity and flexibility, HDPE offers superior strength and resistance, which may be crucial for certain applications.
Matching Material Properties with Specific Application Needs
Each type of plastic film possesses unique properties that make them suitable for different applications:
- LDPE Film is highly flexible and resists tearing. It is ideal for products requiring a softer packaging touch, such as perishable goods.
- HDPE Film, with its higher tensile strength and rigidity, is better suited for heavier or bulkier items needing robust protection.
Choosing between LDPE and HDPE thus depends significantly on the nature of the products to be packaged and the demands of the packaging environment.
Understanding Industry-Specific Requirements
Different industries have unique packaging standards and requirements that influence the choice of plastic film:
- The Food and Beverage industry often requires HDPE for its resistance to contaminants and higher temperatures.
- Medical sector packaging might favor LDPE for its flexibility and transparency, facilitating the safe storage and handling of sensitive medical products.
In every case, the decision should be guided by a thorough understanding of industry-specific compliance, safety standards, and environmental considerations.
By carefully balancing these factors, packaging professionals can choose the most appropriate, cost-effective, and compliant plastic film for their needs.
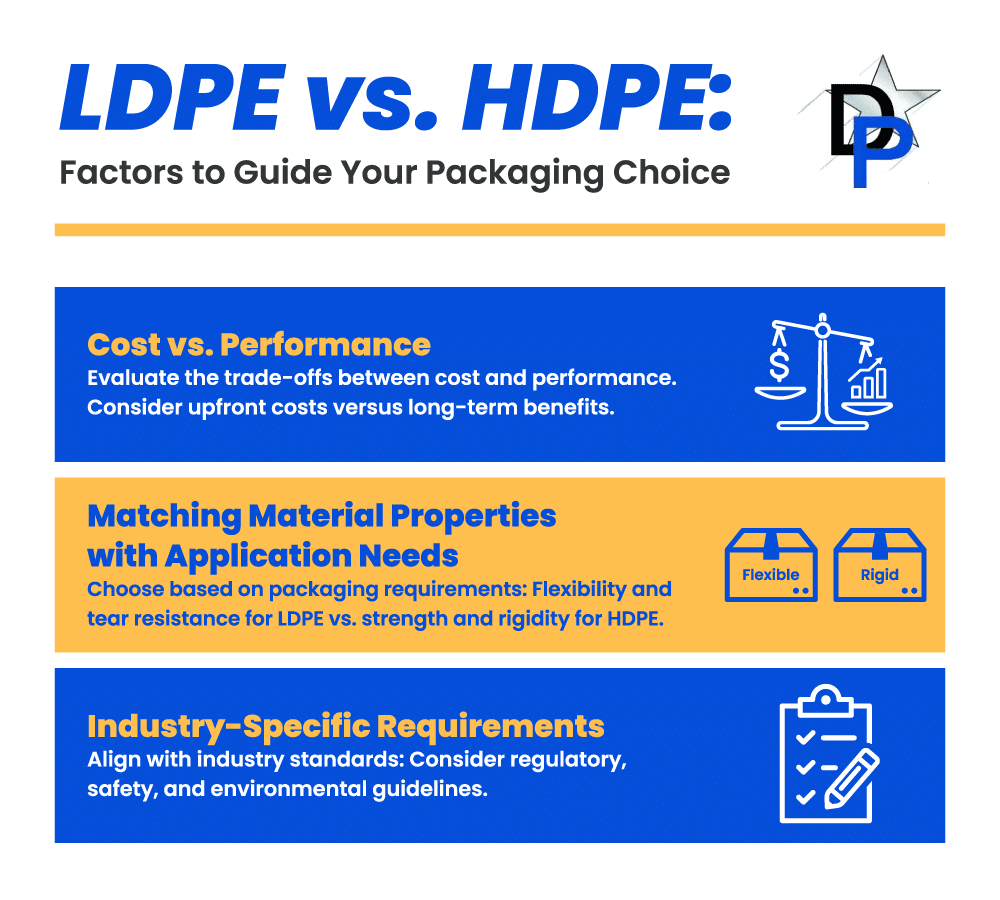
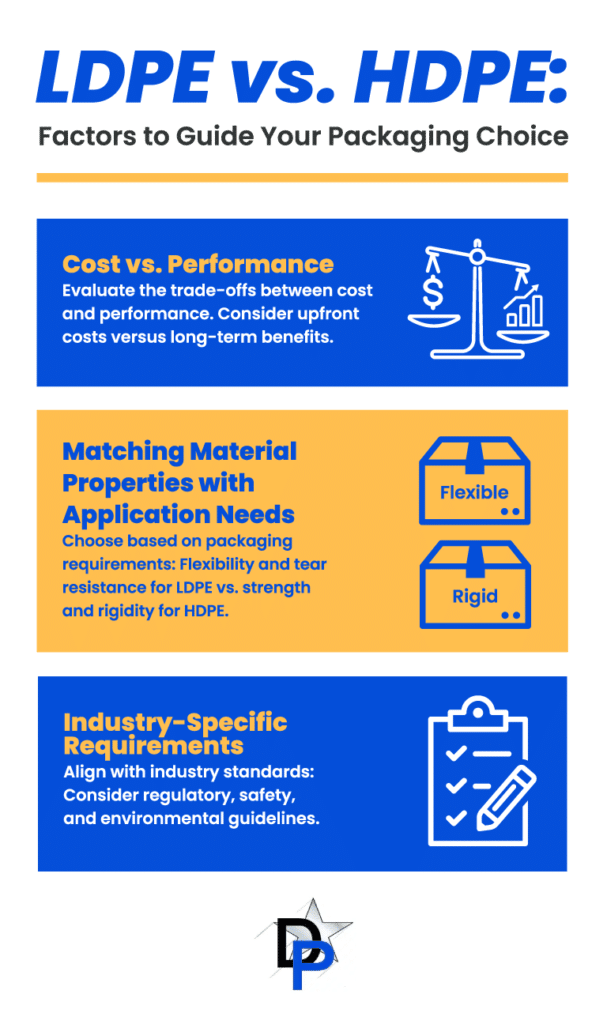
Making the Right Choice for Optimal Packaging Solutions
As we’ve explored the unique properties and applications of LDPE and HDPE films, it’s clear that the choice between these materials can significantly impact the efficiency and success of your packaging solutions. At Dallas Plastics, we specialize in providing high-quality, tailored plastic film solutions that meet the diverse needs of the medical, industrial, and food and beverage sectors. Our expertise and commitment to innovation ensure that we offer only the best in both LDPE and HDPE film technologies.
If you’re looking to enhance your packaging strategy with materials that offer both performance and reliability, reach out to us at Dallas Plastics. Our team is ready to assist you in selecting the right film for your specific needs, ensuring that your products are protected with the highest standards of quality and care.