In the dynamic world of automated packaging, Form, Fill, and Seal (FFS) technology stands out as a cornerstone for efficiency and innovation. These thin plastic films, incorporated into FFS machines’ operation, make it easy and efficient for businesses to package a diverse range of products in record time. Understanding the different types, functions and strategic applications of these films is crucial for businesses seeking to achieve greater operational efficiency in their packaging processes.
Through this comprehensive guide, we aim to explore FFS film technologies at length — from a deeper understanding of what they do and how they work through highlighting some nuanced features powering each type. We’ll also showcase major industries that benefit from using Dallas Plastics’ high-quality customizable FFS Films – including vital sectors such as food & beverage, chemical packaging, medical supplies, and agriculture.
Whether you are a procurement manager, a packaging engineer, or an operations manager, understanding the full spectrum of FFS film capabilities is crucial for optimizing your packaging processes. From enhancing product safety to ensuring regulatory compliance, the right FFS film can markedly improve both operational efficiency and product quality.
Understanding Form Fill Seal (FFS) Technology
Form, Fill, Seal (FFS) technology represents a significant advancement in automated packaging systems, seamlessly integrating forming, filling, and sealing processes into one continuous operation. This innovative approach utilizes thin plastic films to create packages that are then filled with a product and sealed, all within the confines of a single machine. The use of FFS technology is prevalent across multiple industries due to its efficiency and effectiveness in packaging a wide range of products, from liquids and pastes to granulated and powdered substances.
Definition and Basics of FFS Films
FFS films are specially designed plastic materials used to form the package directly on the FFS machine. These films need to possess certain qualities such as strength, flexibility, and barrier properties against moisture and air, ensuring they can withstand the forces involved in the packaging process without tearing or puncturing.
Overview of the FFS Process in Automated Packaging
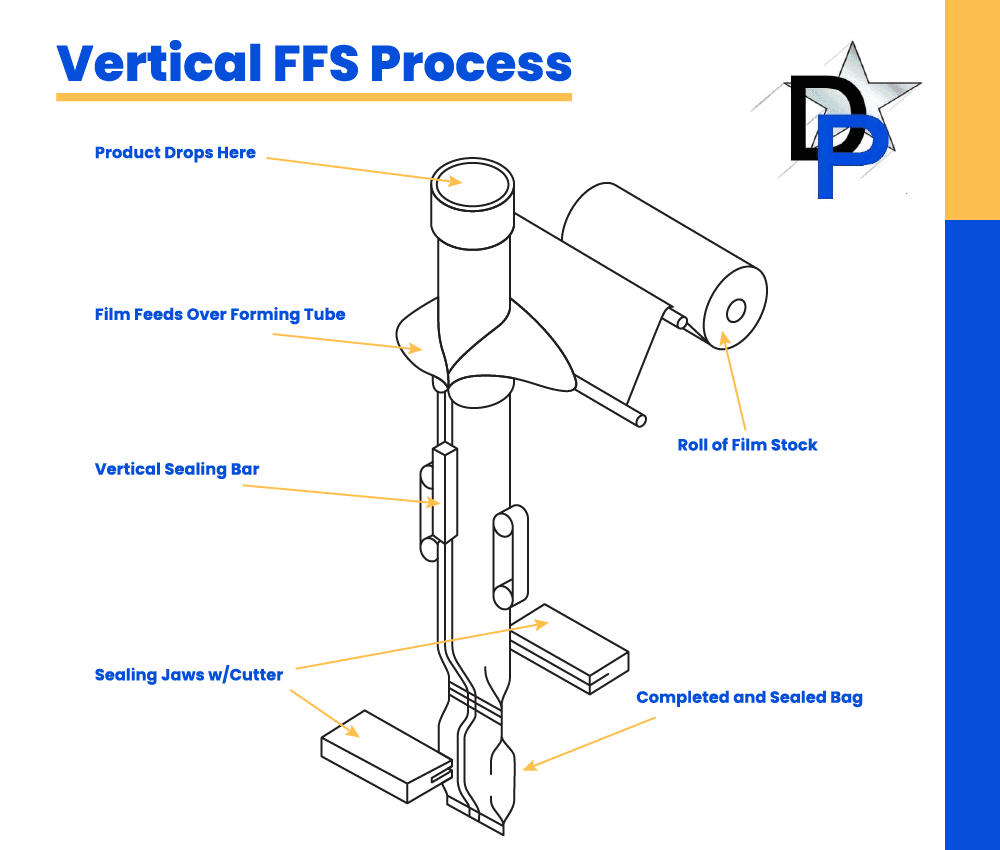
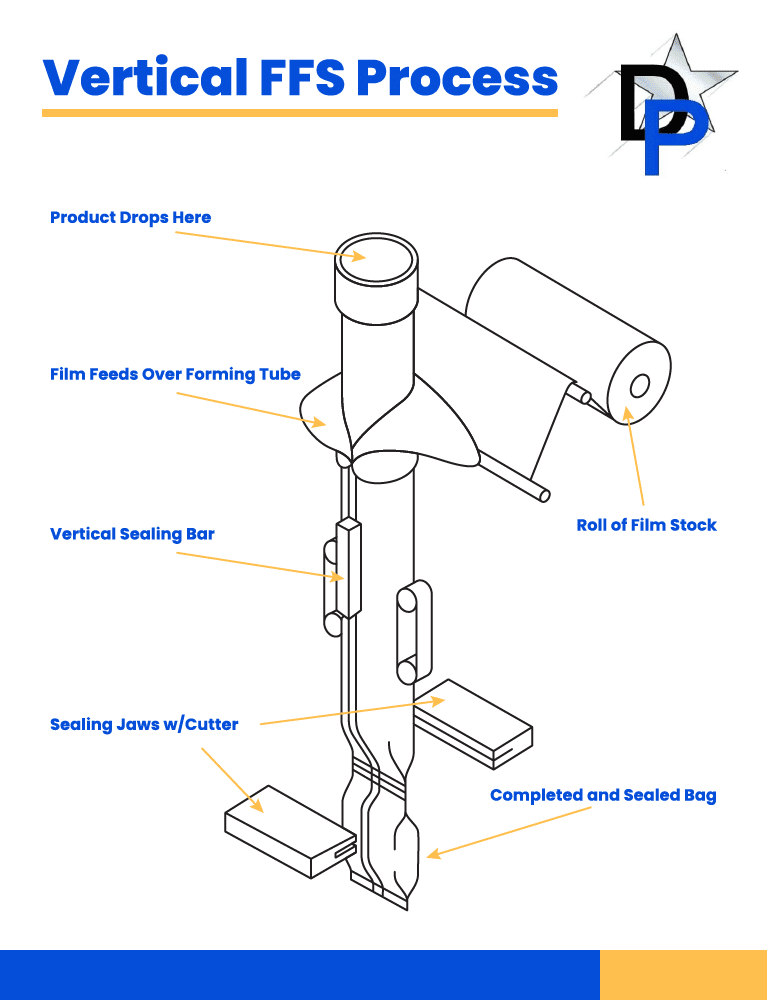
The FFS process involves three main steps:
1. Forming The Film
The process begins with the loading of a roll of FFS film onto an unwinding mechanism. This mechanism carefully feeds the film into the machine, ensuring a smooth and consistent flow to prevent any creases or disruptions. The film is then guided through a series of rollers or guides that help to maintain proper tension and alignment.
In a vertical form fill seal (VFFS) machine, the film is pulled over a forming collar or tube, which shapes the flat film into a cylindrical or tubular structure. As the film wraps around the forming tube, it creates a longitudinal seam that is sealed using heat, pressure, or ultrasonic sealing methods, thereby transforming the flat film into a continuous tube.
In a horizontal form fill seal (HFFS) machine, the film can be folded or manipulated into the desired shape, such as pouches or packets, before sealing along the edges. These forming steps are essential because they define the basic structure and shape of the future packaging, setting the stage for the subsequent filling and sealing operations. This precise and automated handling of the film material ensures that the final packages are uniform, airtight, and ready to efficiently accommodate the product they are designed to hold.
2. Filling it With the Product
Once the film is shaped into its final form, whether it’s a cylindrical tube in vertical form fill seal (VFFS) machines or a pre-shaped pouch in horizontal form fill seal (HFFS) machines, the system is ready to dispense the product. This is achieved through a carefully calibrated dosing mechanism designed specifically for the type of product being packaged. For powders or granular materials, an auger or volumetric cup filler might be used, while liquids often require a pump or gravity-based filler. Precision sensors and controls ensure that each package receives the exact amount of product required, maintaining consistency and reducing waste.
3. Sealing to Secure the Contents
The sealing process in the form fill seal (FFS) packaging system is a pivotal step that ensures the integrity, security, and hygiene of the packaged product. After the film has been shaped and filled with the intended product, the open end of the packaging must be sealed to create a secure, tamper-evident enclosure.
In vertical form fill seal (VFFS) machines, this typically involves making a horizontal seal across the top of the package where the product has just been filled.
In horizontal form fill seal (HFFS) machines, the seal could be along the side or the top of the package, depending on its design. The sealing process utilizes heat and pressure, delivered through heated sealing jaws or bars, to bond the film layers together. Some systems may also use ultrasonic sealing, which employs high-frequency vibrations to create a frictional heat that bonds the materials without direct heat, making it suitable for heat-sensitive products.
Significance of FFS Films in Modern Packaging Technologies
In today’s fast-paced market environment, the role of FFS films has grown considerably. These films facilitate rapid production capabilities and contribute significantly to the scale of operations in manufacturing. This technology allows businesses to achieve greater efficiency by automating repetitive tasks, saving time on manual labor and enabling high-speed production runs. Furthermore, FFS films provide robust protection against external factors like moisture and air that can negatively impact product quality.
Moreover, as the industry continues to embrace automation across different sectors of their manufacturing processes from routine automatic dispensing procedures through advanced multi-function equipment, there is a growing demand for customized tailored cut-to-size options in packaging materials; an area where Dallas Plastics excels at providing flexible solutions suitable for even highly specialized application requirements With ongoing advancements in material science and automation, FFS technology continues to evolve, pushing the boundaries of what is possible in automated packaging.
Request a Quote
Request a Quote
Types of FFS Films
FFS films, or Form Fill Seal films, are crucial components in the packaging industry, offering a versatile solution for safely and efficiently packaging a variety of products. These films are typically categorized into different types primarily based on their production processes and the distinct characteristics they bring to different applications. These different types include:
Monolayer Films Vs. Multilayer Film
Monolayer films are made of one layer, typically an economical choice for applications where barrier protection is less critical. Key features may include:
- Flexibility: Making them ideal for products that need versatile packaging such as snack foods.
- High Clarity and Glossiness: Providing excellent visual appeal which can be important in the retail industry.
Although monolayers provide essential protective properties, their basic single-layer design means they tend not to offer more sophisticated characteristics required by certain industries.
Multilayer films, on the other hand, consist of multiple layers of different polymers, each contributing specific properties to the overall structure. This layered construction allows for the customization of the film to achieve a combination of barrier protection, mechanical strength, and other desired characteristics.
- Enhanced Barrier Properties: By combining layers of diverse materials, multilayer films can offer excellent barrier protection against oxygen, moisture, aroma transfer, and light. This makes them suitable for packaging perishable food items, pharmaceuticals, and products requiring extended shelf life.
- Customizable Properties: The layering process allows for the inclusion of specific functional attributes, like anti-static properties, UV resistance, and heat seal-ability, tailored to the needs of particular applications.
- Superior Mechanical Strength: Multilayer films generally provide greater puncture resistance, tensile strength, and durability compared to monolayer films, making them appropriate for packaging heavier or bulkier items.
Vertical FFS Vs. Horizontal FFS
Form Fill and Seal (FFS) films can be divided into two main types based on the orientation of the packaging equipment used: Vertical Form Fill Seal (VFFS) films and Horizontal Form Fill Seal (HFFS) films. Each type of film is designed for specific packaging configurations and comes with its own set of advantages and limitations.
Vertical Form, Fill, Seal
- Orientation: VFFS films are designed for vertical packaging machines that create pouches or bags by forming the film into a tube, filling it with product from the top, and then sealing it vertically.
- Applications: Ideal for packaging granular, powdered, and liquid products. Commonly used for food items like snacks, coffee, sugar, nuts, and frozen foods. Suitable for non-food items like detergents, chemicals, and small hardware.
- Mechanical Properties: These films usually have good sealing properties to handle the vertical sealing process. Often designed to be puncture-resistant if handling denser products.
- Ease of Use: VFFS machines are generally faster than HFFS machines due to their simpler motion paths. Capable of producing a variety of package styles, including pillow bags, gusseted bags, and block-bottom bags.
Horizontal Form Fill Seal (HFFS) Films
- Orientation: HFFS films are designed for horizontal packaging machines that form, fill, and seal the film horizontally.
- Applications: Commonly used for single-serve sachets, pouches, and flow-wrapped products. Suitable for packaging food items like chocolate bars, biscuits, ready-to-eat meals, and medical devices. Also used for non-food items like wet wipes and personal care products.
- Mechanical Properties: These films often require high tensile strength to handle horizontal pulling and sealing processes. Designed to maintain shape and structural integrity throughout the fill and seal cycle.
- Ease of Use: HFFS machines allow for precise control over the placement and orientation of products, making them ideal for packaging items that need to be aligned properly. Capable of creating a variety of package types, including three- and four-sided sealed pouches, flow packs, and cartons.
Specialty Plastic Films
For specialized applications, there are films designed with specific properties tailored to meet unique industry requirements. Specialty plastic films may incorporate various additives or undergo unique treatments to enhance certain features:
- High Barrier Films: Engineered to provide superior protection against moisture, gasses, and other external elements.
- Bio-based Films: Made from renewable resources for companies looking to improve their sustainability metrics.
- High-temperature Films: Designed to withstand extreme temperatures without degrading, suitable for products that require sterilization.
- Recyclable Films: Designed to reduce environmental impact, these sustainable alternatives utilize recycled materials without compromising on product safety.
Application of FFS Films Across Industries
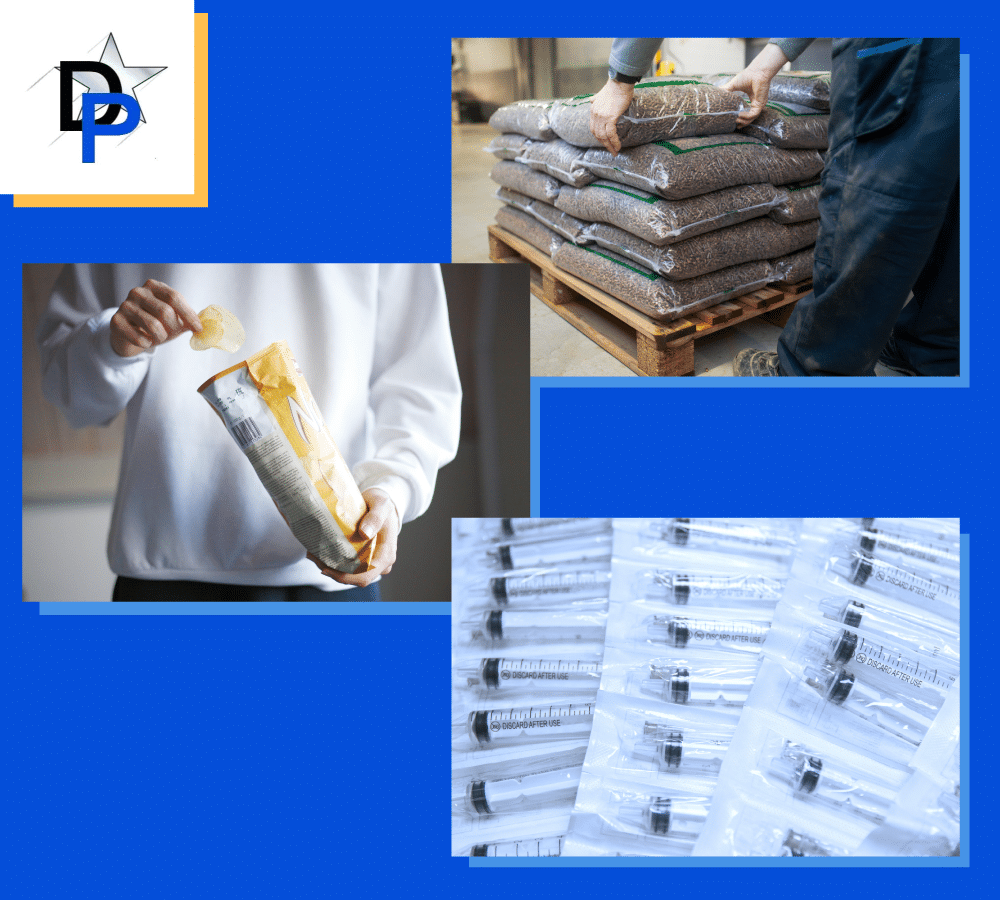
Form Fill Seal (FFS) technology has revolutionized packaging across multiple industries, offering tailored solutions that meet diverse environmental and regulatory demands. This technology offers limitless options for automated applications, and by choosing the correct type of FFS film with tailored features that meet these specific needs, industries can achieve various objectives. These include maintaining product safety in each phase of production from automation to transport/distribution chain ecologies.
Food and Beverage Sector
In the food and beverage industry, packaging not only serves the purpose of protection but also plays a vital role in maintaining the freshness and extending the shelf life of products. FFS films enable cost- and time-efficient solutions for packaging various food products. Key uses include:
- Packaging of Perishables: such as meats, fruits, and vegetables to retain freshness.
- Snack Packaging: involves high-speed wrapping processes.
- Beverage Sachets and Pouches: for liquids or powdered mixes.
This sector often requires the use of food-grade plastic sheeting that meets strict regulatory standards for health and safety.
Medical Packaging
In the realm of medical products, sterility and security are paramount. FFS films deliver by providing robust protection against environmental contaminants, ensuring that medical devices and pharmaceuticals reach consumers uncompromised. Applications include:
- Packing of Syringes and Catheters: where sterility is critical.
- Protective packaging for medications: ensuring barrier protection from moisture and gasses.
- Flexible Packaging for Lab Supplies: customizable to specific shapes and sizes.
Medical packaging films often need to be compatible with sterilization processes, such as gamma irradiation, making the material choice crucial.
Industrial Packaging Solutions
For industrial applications, durability and resistance to harsh conditions are essential. FFS films in this sector are designed to withstand extreme environments, protecting products from dust, moisture, and mechanical stresses. Common uses include:
- Chemical Packaging: which requires chemical resistance and strong seals.
- Hardware and Components Packaging: designed for heavy items needing robust protective barriers.
- Agricultural Products Packaging: where large volumes and pest protection are necessary.
FFS films used in industrial settings are typically made of sturdy plastic materials, engineered specifically to withstand the stresses associated with handling and transportation.
By leveraging the versatility and adaptability of FFS technology, industries can achieve greater efficiency in their packaging processes while ensuring product safety and compliance with relevant regulations. Whether it’s preserving the freshness of food, ensuring the sterility of medical products, or protecting industrial goods, FFS films offer a reliable and effective solution.
Benefits of Using FFS Films
FFS films, or Form Fill Seal films, play a pivotal role in modern packaging systems, offering numerous benefits across various sectors. Their use considerably enhances operational efficiency, ensures product safety, and aids in meeting regulatory compliance. This section explores these key benefits in detail, highlighting how they contribute to streamlined packaging processes.
Enhancing Operational Efficiency in Packaging Processes
FFS technology leverages automation to optimize packaging operations, significantly boosting productivity and reducing labor costs. The seamless nature of FFS films in the packaging process minimizes downtime due to the following factors:
- Speed: FFS machines can package products at high speeds, handling hundreds, if not thousands, of items per hour. This rapid processing capability is crucial in sectors like food and beverage, where time-sensitive products are managed.
- Reduced Waste: Precision in film usage ensures minimal material wastage. FFS films are cut and sealed to exact specifications, meaning each segment of the film is utilized with maximum efficiency.
- Lower Labor Requirements: Automation reduces the need for manual intervention. Fewer personnel are required to manage packaging operations, which lowers the risk of human error and further enhances workflow efficiency.
Contributing to Product Safety and Integrity
The integrity of a product’s packaging is paramount, particularly in industries such as food and medical sectors. FFS films provide robust protection against various environmental factors:
- Barrier Protection: FFS films are engineered to offer excellent barrier properties against moisture, oxygen, and other contaminants, preserving the quality and extending the shelf life of packaged products.
- Tamper Evidence: Many FFS films are designed to include tamper-evident features, ensuring that any unauthorized access to the packaged content is easily detectable, which is vital in pharmaceuticals and consumer goods.
- Consistency and Reliability: The automated nature of FFS machines ensures that each package is sealed with consistent quality, reducing the risk of leaks or breaches that could compromise product safety.
Compliance with Industry-Specific Regulations
Regulatory compliance is a critical consideration for industries like pharmaceuticals and food and beverage. FFS films help businesses adhere to strict industry standards and regulations:
- Material Compliance: Different industries require FFS films that comply with different quality and safety standards, such as food-grade plastic sheeting. Businesses must ensure they select appropriate materials to avoid damaging their reputations or facing legal penalties.
- Traceability: Advanced FFS systems can incorporate printing and labeling solutions that help in tracking and tracing the products throughout the supply chain, essential for regulatory compliance.
- Customizable Features: Depending on the regulatory needs of a sector, FFS films can be customized to include UV protection, anti-static properties, and other specialized characteristics to comply with particular industry requirements.
By understanding the extensive benefits provided by FFS films, businesses in various sectors can leverage this technology to enhance their operational effectiveness, ensure the safety and integrity of their products, and maintain compliance with industry regulations. This blend of efficiency, safety, and compliance makes FFS films a critical component of modern automated packaging systems.
Selecting the Right FFS Film
Selecting the perfect FFS film for your packaging requirements involves considering various factors to ensure optimal performance and cost-effectiveness. This process is crucial for procurement managers and packaging engineers who aim to enhance production efficiency and maintain product quality.
Material Properties
Different materials offer specific benefits and limitations. Here are key considerations:
- Barrier Properties: Essential for products needing protection against moisture, oxygen, or chemicals.
- Flexibility and Strength: Determines the handling and resistance to tearing during filling and transportation.
- Optical and Aesthetic Qualities: Important for consumer-facing products where appearance can influence buying decisions.
- Size: The dimensions of the film must align with the specific requirements of the product being packaged, ensuring optimal protection, presentation, and convenience.
Durability and Protective Features
Durability is critical in ensuring that the packaging withstands the physical demands of transit and storage without compromising the product:
- Resistance to Puncture and Abrasion: Essential for industrial goods that may be exposed to rough handling.
- Thermal Resistance: Important for products subjected to varying temperatures.
- Chemical Stability: A must for packaging products with potential chemical interactions, such as cleaners or certain foods.
Cost-effectiveness
Balancing quality with cost efficiency is key:
- Initial Investment vs. Long-term Savings: Evaluate the upfront costs against potential savings from reduced waste and improved process efficiency.
- Operational Impact: Consider if higher quality films can increase machine speed or reduce downtime.
Tips for Procurement Managers and Packaging Engineers
- Assess the Entire Lifecycle: Consider not only the purchase price but also the operational and disposal costs.
- Request Samples: Testing different films under real conditions can provide insightful data that influence the decision-making process.
- Consult with Suppliers: Leverage their expertise to understand the nuances of different films and their suitability for your specific needs.
By carefully evaluating these factors, professionals can ensure they select the best FFS film that offers reliability, efficiency, and value in their packaging operations.
Implementing FFS Solutions in Operations
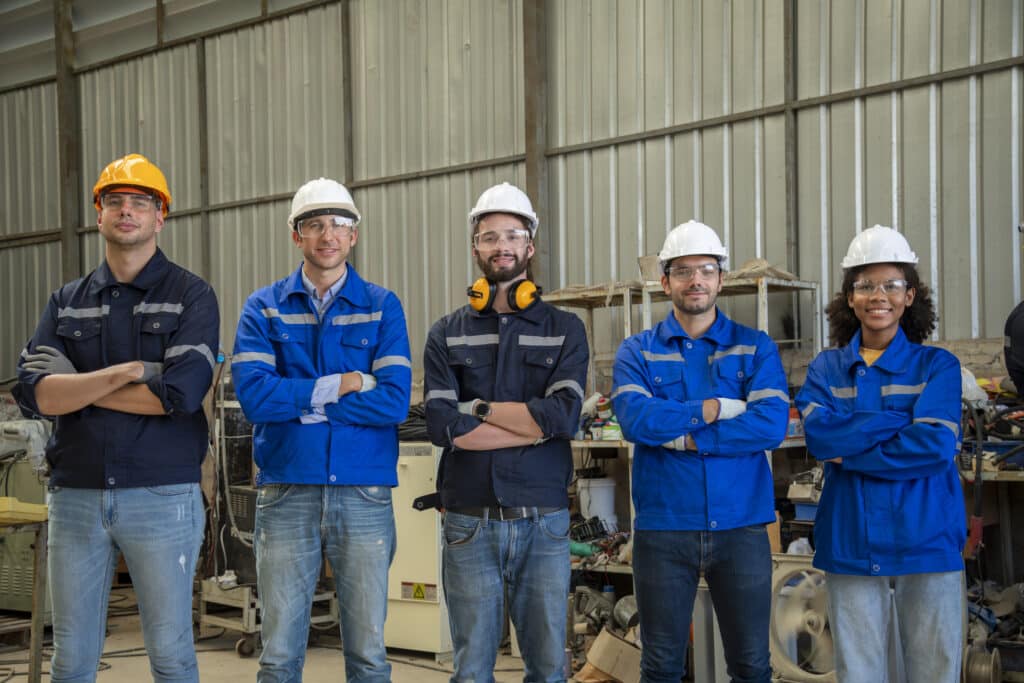
Before embarking on the implementation of FFS systems, companies must understand the necessary steps and considerations involved. This includes setting up the system, training personnel, and ensuring consistent maintenance to uphold packaging quality and performance.
Initial Setup and Integration into Existing Systems
Setting up an FFS system demands careful planning to ensure compatibility with existing packaging lines. The steps typically include:
- Assessment of Space and Infrastructure: Evaluate the available space and infrastructure adaptability for accommodating new FFS machinery.
- System Customization: Tailor the system settings to match specific product and packaging requirements.
- Integration Testing: Conduct thorough testing to confirm seamless integration with existing operations, ensuring no disruption in other processing lines.
Training and Support for Operations Staff
For the FFS system to operate efficiently, skilled personnel are essential. Key training objectives are:
- Operational Training: Enable staff to manage daily operations, troubleshoot minor issues, and understand the full functionality of the FFS technology.
- Safety Training: Educate on safety protocols to prevent work-related accidents and ensure a safe working environment.
- Ongoing Support: Provide continuous technical support and advanced training sessions to help personnel keep abreast of technological advancements and operational best practices.
Regular Maintenance and Quality Checks
To maximize the lifespan and efficiency of FFS systems, regular maintenance and quality assurance checks are vital. These should focus on:
- Routine Inspections: Schedule regular inspections to ensure machinery parts are functioning properly and efficiently.
- Quality Control: Implement stringent quality control measures to monitor packaging integrity and consistency, avoiding potential product recalls or customer dissatisfaction.
- Preventative Maintenance: Develop a preventative maintenance schedule to address potential issues before they lead to system downtime.
Implementing FFS solutions requires thorough preparation, robust training programs, and diligent maintenance. By emphasizing these areas, companies can enhance the reliability and productivity of their packaging operations.
Maximizing Efficiency and Quality with Form Fill Seal Films
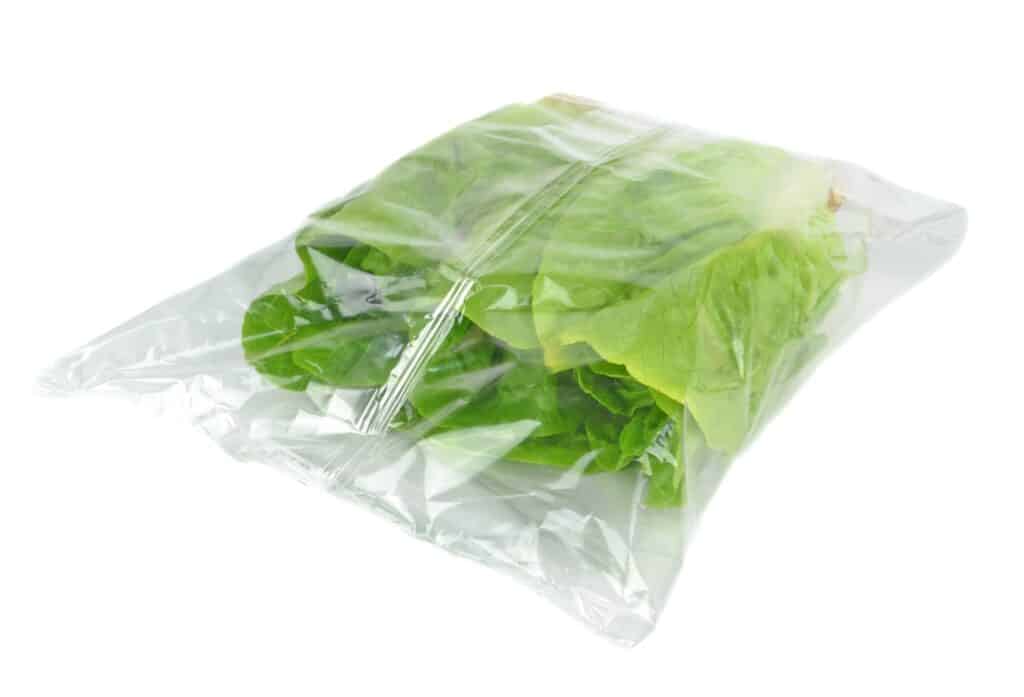
In today’s fast-paced markets, where product quality and efficiency are paramount, businesses must leverage innovative packaging solutions that provide unparalleled advantages. FFS films have revolutionized the industry by enhancing automation capability while guaranteeing high levels of consistency in terms of both process control and regulatory compliance.
With their broad spectrum of high-quality, customizable options tailored to meet specific industry needs, Dallas Plastics stands out as a leader in the field. Their commitment to innovation and compliance with regulatory standards ensures that your packaging solutions are not only efficient but also robust and compliant.
By incorporating their films into your operations, you are choosing a path that leads to improved operational efficiency, enhanced product safety, and adherence to necessary regulatory standards.
Reach out to Dallas Plastics today to discuss how their FFS films can be integrated into your packaging systems or to explore their custom film solutions. Their expert team is ready to assist you in making informed decisions that align with your specific packaging needs and help you achieve your operational goals.
Let’s work together to revolutionize your packaging processes with the best solutions the industry has to offer.