In the intricate dance of manufacturing, precision and safety are paramount, especially when it comes to plastic films—a staple in sectors like medical, industrial, and food and beverage. Current Good Manufacturing Practices, or cGMP, are the choreographed steps ensuring that products meet the highest standards of quality and safety. In this blog post, we will explore the crucial role cGMP plays in the production of plastic films, examining the benefits and necessity of adhering to these rigorous guidelines.
We will also delve into Dallas Plastics’ commitment to cGMP practices and examine its impact on the company’s leadership in plastic film manufacturing.
Whether you’re a manufacturing executive, a procurement manager, or a quality assurance specialist, understanding the advantages of cGMP in plastic film manufacturing is key to making informed decisions and maintaining a competitive edge. Join us as we unwrap the layers of cGMP’s impact on plastic film production and Dallas Plastics’ dedication to upholding these esteemed standards.
What are Current Good Manufacturing Practices (cGMP)?
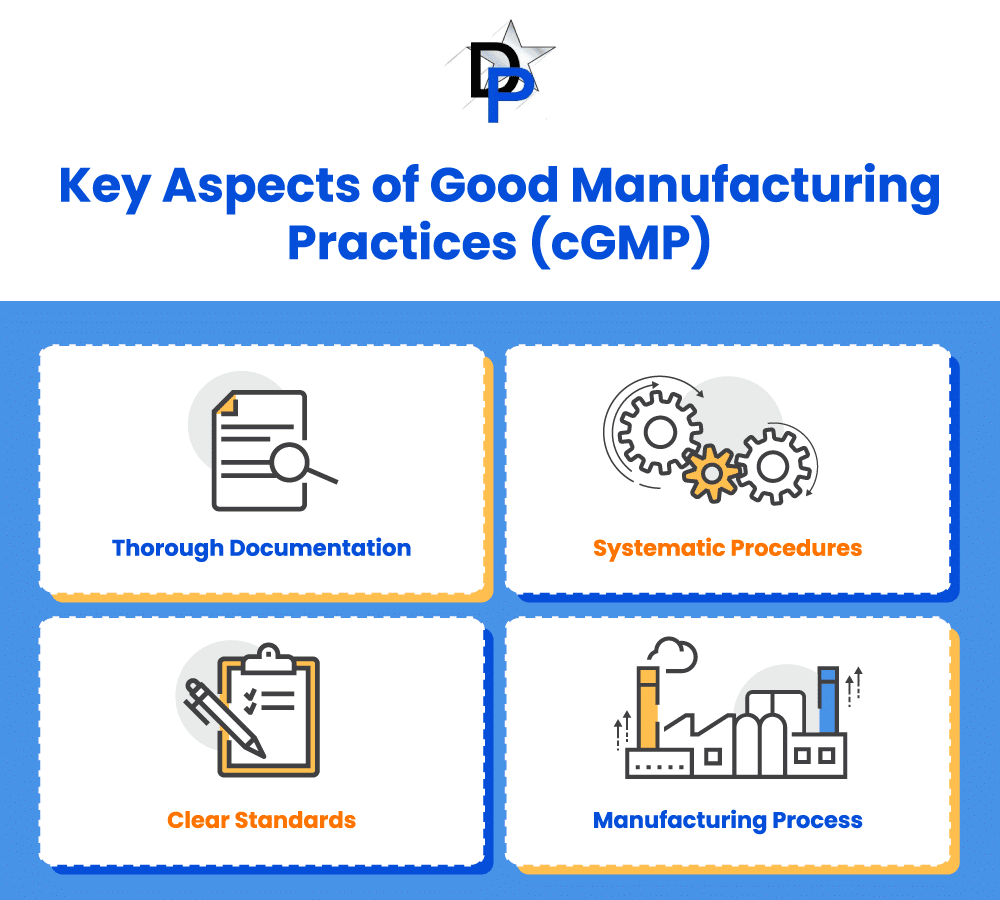
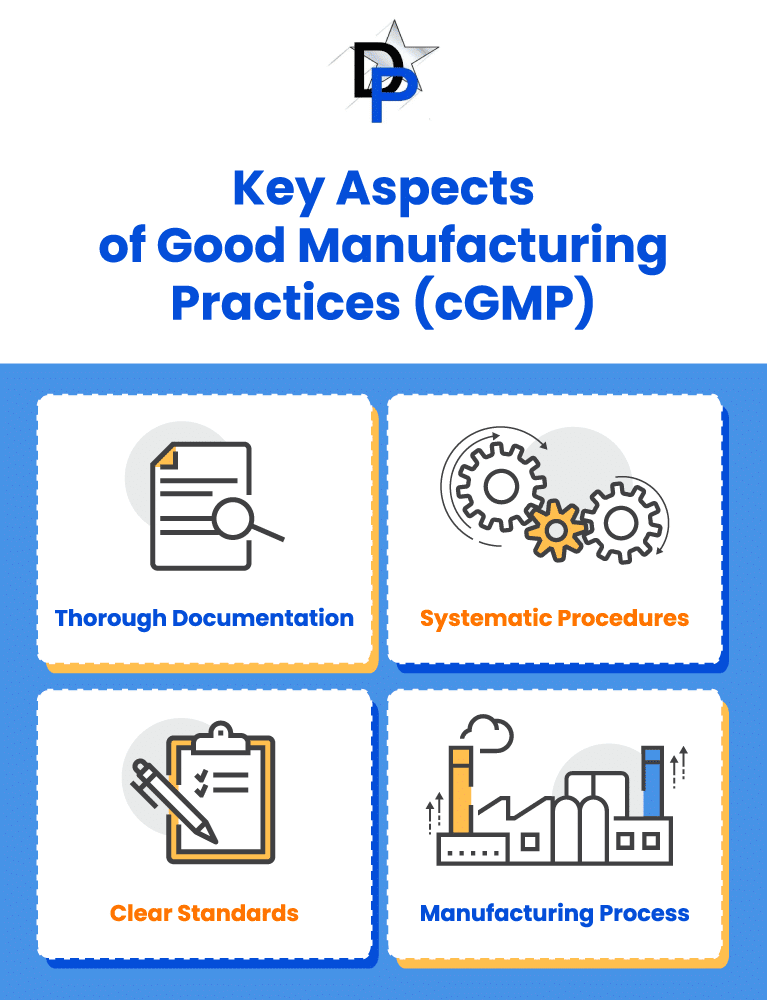
Current Good Manufacturing Practices, commonly known as cGMP, are the regulations enforced by the FDA and other regulatory bodies worldwide to ensure proper design, monitoring, and control of manufacturing processes and facilities.
The adoption of cGMP regulations ensures the identity, strength, quality, and purity of product manufacturing by requiring that manufacturers adequately control operational processes across the entire value stream.. This includes establishing strong quality management systems, obtaining appropriate quality raw materials, establishing robust operating procedures, detecting and investigating product quality deviations, and maintaining reliable testing laboratories.
The role of cGMP is pivotal in safeguarding the consumer by ensuring that products are consistently produced and controlled to the quality standards appropriate for their intended use. These regulations are flexible enough to allow each manufacturer to decide individually how to best implement the necessary controls by using scientifically sound design, processing methods, and testing procedures.
The key aspects of cGMP include thorough documentation, systematic procedures, and clear standards, which are crucial for traceability and accountability in the manufacturing process. Compliance with cGMP regulations and guidelines is essential for manufacturers to release products that are safe for consumer use and to avoid costly recalls and reputational damage.
The Importance of cGMP in Plastic Film Manufacturing
The importance of cGMP in the manufacturing industry cannot be overstated. Adherence to cGMP guidelines directly influences the production process, providing a structured framework that manufacturers must follow. This is especially vital in the production of plastic films, which are used in critical applications where precision and safety are paramount.
The control of environmental conditions is a crucial aspect of cGMP that significantly impacts the integrity of plastic films. By following cGMP guidelines, manufacturers can effectively manage the risk of contamination, which is especially critical in applications where plastic films are used for packaging in the medical, food, and beverage industries. Consistent implementation of these practices ensures that every batch of plastic film produced is of predictable and reproducible quality, thereby guaranteeing reliability for end-users and maintaining the trust of customers and stakeholders.
Adherence to these standards ensures that every phase of the manufacturing process, from raw material sourcing to final product inspection, is executed with an emphasis on quality and consistency. This steadfast commitment to cGMP is essential in fostering traceability and accountability, critical components in modern manufacturing that allow for the tracking of materials and processes, ensuring that any issues can be swiftly identified and addressed.
Moreover, cGMP ensures that manufacturers are consistently evaluating and improving their processes to maintain product quality standards. By following these guidelines, manufacturers are encouraged to regularly evaluate and enhance their processes, leading to the development of superior products. Furthermore, cGMP compliance is instrumental in meeting the specific quality demands of different industries, whether it’s the stringent sterility requirements in the medical sector or the durability standards in industrial applications, thereby reinforcing the trust and reliance placed by customers in these high-performance products.
Advantages of cGMP Certified Plastic Films
Current Good Manufacturing Practices (cGMP) certified plastic films come with a promise of superior product reliability that is critical for end-users across various sectors. These certifications ensure that the films have been manufactured under stringent quality control measures, which translates into consistent performance and longevity of the product. This consistency in product quality is especially crucial for businesses operating in highly regulated industries, such as medical and food packaging sectors, where any deviation from strict standards can have serious consequences.
By using cGMP certified plastic films, businesses can leverage the enhanced reputation that these products carry. It signifies a commitment to upholding high-quality standards and provides assurance that the products meet rigorous health and safety benchmarks.
Moreover, compliance with international standards and regulations is streamlined through cGMP certification, leading to fewer regulatory hurdles and reduced chances of product recalls. This proactive approach to quality management through cGMP certification ultimately helps in mitigating risks associated with product failures and protects the brand reputation.
Considerations for Businesses in Choosing a Plastic Film Supplier
In today’s fiercely competitive business landscape, making informed decisions when selecting suppliers is crucial to the success of any venture. While many factors can impact this decision-making process, a key consideration for businesses in choosing a plastic film supplier should be cGMP compliance.
A supplier’s adherence to Current Good Manufacturing Practices is not just a badge of honor; it represents a commitment to manufacturing processes that prioritize product quality, safety, and consistency. For businesses in sectors where these factors are non-negotiable, such as in medical, industrial, and food and beverage industries, the cGMP status of a supplier is a key differentiator.
The long-term benefits of partnering with a cGMP-compliant plastic film manufacturer cannot be overstated. Such a partnership ensures that the products received meet stringent quality standards, which is essential for maintaining the integrity of the end user’s product. Moreover, it minimizes the risk of product recalls that can arise from quality failures, thereby protecting a business’s reputation and bottom line.
Suppliers like Dallas Plastics that maintain cGMP compliance offer their clients the assurance that the plastic films supplied are produced under rigorous control and to the highest standards.
Taking the Next Steps: Ensuring Your Supplier Meets cGMP Standards
Once a business has recognized the value of partnering with a cGMP-compliant plastic film supplier, it’s essential to take the necessary steps in ensuring that their potential partner meets these standards. Conducting due diligence is crucial when evaluating suppliers’ adherence to cGMP guidelines. Querying potential suppliers on their cGMP practices can provide insights into their commitment to quality and safety. It’s essential to consider how they maintain product standards, manage quality control, and handle documentation. These factors are indicative of a supplier’s reliability and dedication to excellence in manufacturing.
Evaluating a supplier’s cGMP compliance isn’t limited to verbal assurances; tangible evidence is key. Requesting access to relevant documentation and records can help assess their compliance level. Additionally, conducting audits and arranging site visits can be effective strategies for verifying a supplier’s claims about their cGMP standards. These steps are vital for businesses aiming to uphold their product quality and safeguard their reputation in the industry.
Request a Quote
Request a Quote
Dallas Plastics and Its Commitment to cGMP
Dallas Plastics incorporates Current Good Manufacturing Practices (cGMP) to ensure that every aspect of their production process aligns with rigorous quality and safety standards. Through an entrenched culture of compliance, Dallas Plastics meticulously integrates cGMP protocols into the daily operations, from initial design to final product delivery. The resulting product portfolio boasts the coveted cGMP certification, making Dallas Plastics a trusted provider of high-quality plastic films for businesses worldwide.
Real-world examples of Dallas Plastics’ adherence to cGMP standards are evident in their production facilities. Regular audits, both internal and by third-party assessors, guarantee that the manufacturing environment and procedures conform to the established guidelines. Clients of Dallas Plastics can attest to the benefits of this compliance, as they receive products that are manufactured in a controlled and validated process.
Moreover, Dallas Plastics’ commitment to cGMP is reinforced by continuous employee training, ensuring that every team member is proficient in these essential practices to maintain the highest level of product quality and safety.
Dallas Plastics' Industry Leadership and Expertise
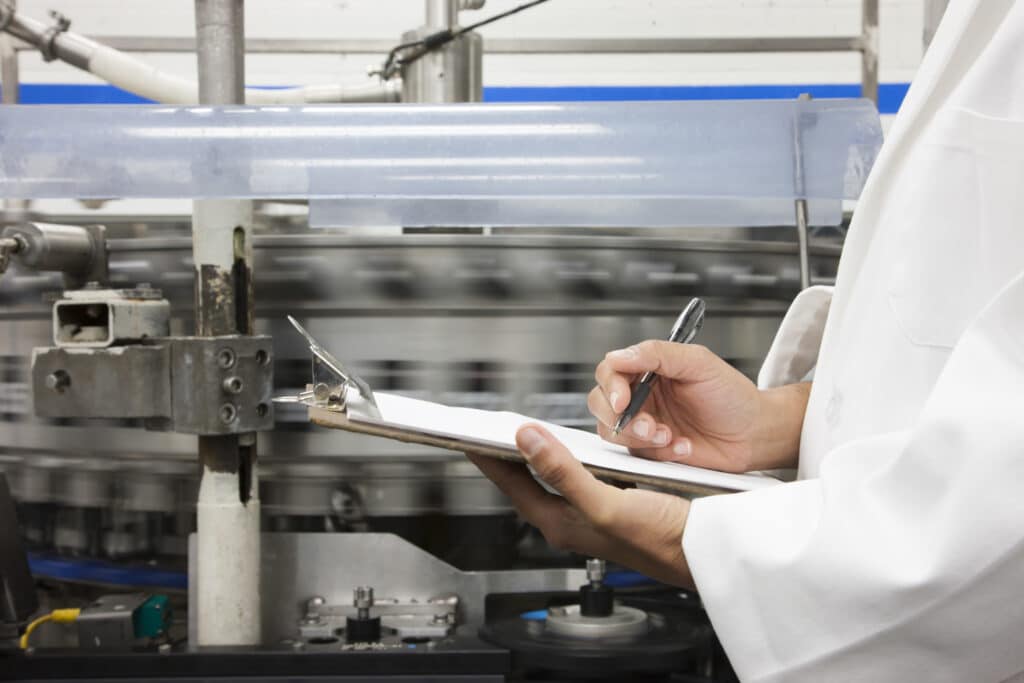
The standards set by cGMP are not merely regulatory benchmarks; they are the foundation of trust and assurance in the plastic film manufacturing industry. By adhering to these guidelines, manufacturers demonstrate their commitment to delivering products of predictable quality that meet the stringent requirements expected by customers.
Dallas Plastics has solidified its position as an industry leader through decades of dedicated service and an unwavering commitment to manufacturing excellence. With a rich history steeped in innovation and customer satisfaction, the company has developed a robust understanding of the intricacies involved in the production of high-quality plastic films. Their expertise is not only evident in the superior products they deliver but also in the meticulous processes they employ. Likewise, the expertise and capabilities of Dallas Plastics extend beyond their commitment to cGMP-certified manufacturing.
Dallas Plastics’ unwavering dedication to cGMP practices sets them apart as a supplier committed not just to exceeding industry standards but also building enduring partnerships with businesses across various sectors. Our clients can attest to the peace of mind that comes from knowing their supplier doesn’t just comply with cGMP standards but embraces them as a core aspect of their operational excellence.
Take the next step in securing your business’s reputation and protecting your customer base. Embrace the advantages of working with a cGMP-compliant manufacturer like Dallas Plastics. Our expertise is your advantage, and together, we can achieve the highest standards of quality and reliability in your products. Reach out to us to request a quote and let’s discuss how our cGMP-certified plastic films can support your business goals.