The manufacturing world is an intricate dance of precision and innovation, where the quality of a product is often determined in its creation. In the world of plastic film production, one of the most popular methods is blown film extrusion.
At Dallas Plastics, this method is the backbone of their operation, crafting an array of high-quality plastic films that serve the medical, industrial, and food and beverage sectors. This blog post will offer an in-depth look at the blown film extrusion process, revealing how a meticulous blend of science and technology ensures that each product meets the pinnacle of excellence. From the initial selection of raw materials to the final touches that ready the product for market, we will explore the nuances that define consistent quality and the latest innovations shaping the industry.
Join us as we unravel the complexities of producing plastic films and discover why the manufacturing process is vital to the integrity of the final product.
Understanding the Blown Film Extrusion Process
Blown film extrusion is a manufacturing process used to create a variety of plastic film products by extruding molten polymer through a circular die. The process results in a thin, tubular film that can be used in numerous applications, ranging from plastic bags to packaging films. The basic components essential to this process include the extruder, die, air ring, bubble cooling, collapsing frame, and take-up unit.
Each component of a blown film line plays a pivotal role in shaping the quality and characteristics of the final plastic film. The extruder pushes the polymer through the die, where it takes shape, while the air ring blows air onto the hot film to cool it down. The bubble cooling mechanism further stabilizes the film’s temperature, and the collapsing frame folds the tube into a lay-flat form.
Finally, the take-up unit winds the film onto reels, completing the transformation from raw material to a versatile plastic film ready for various uses.
Steps in the Blown Film Extrusion Manufacturing Process
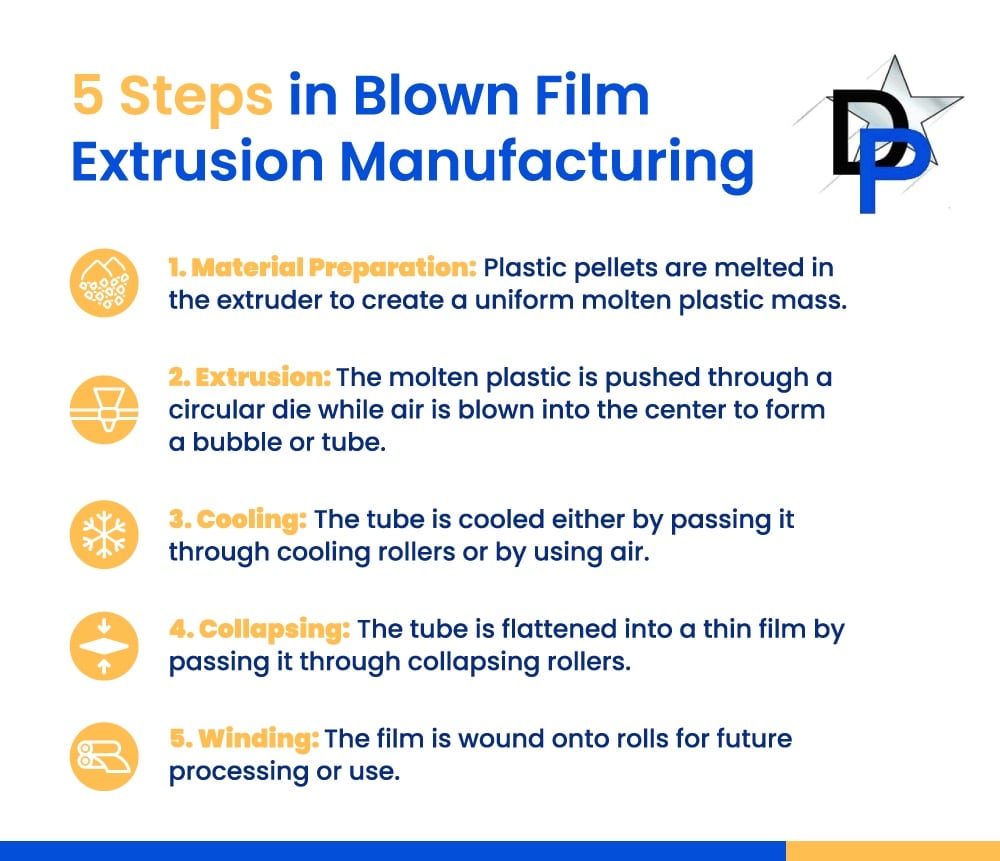
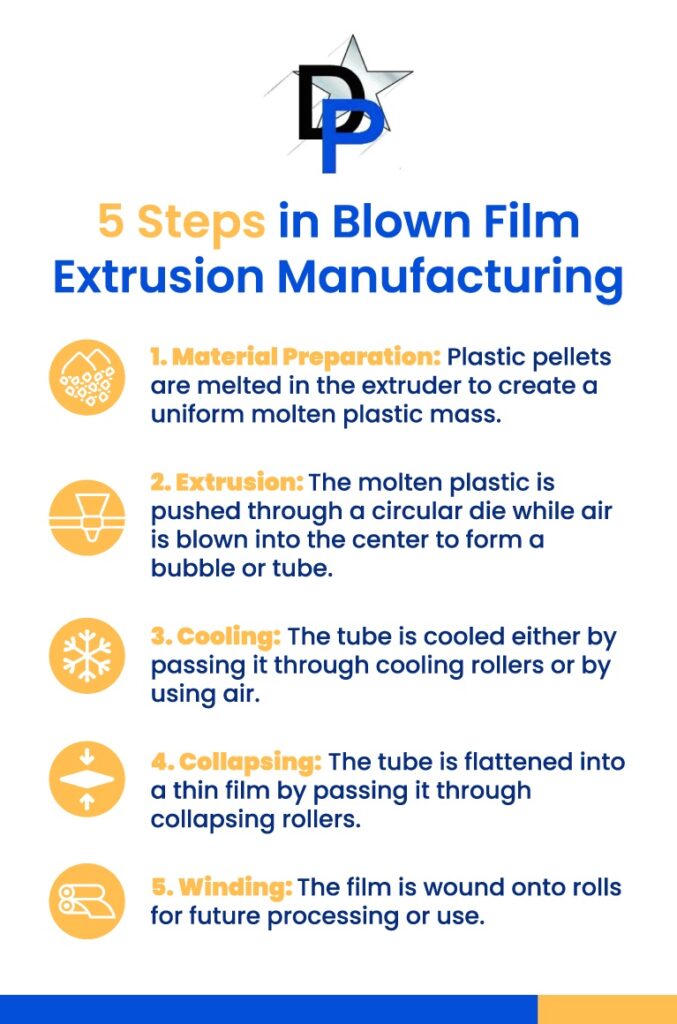
The blown film extrusion manufacturing process begins with a critical first step: the selection of raw materials. The materials used, typically various grades of polyethylene, play a pivotal role in determining the film’s quality, durability, and suitability for specific applications. This careful selection ensures that each batch meets the necessary performance criteria before moving to the next stage.
Once the appropriate raw materials are chosen, they are fed into the extruder where they melt at high temperatures. The molten polymer is then forced through a circular die to form a seamless tube. This tube is drawn upward while air is introduced into its center, inflating the tube to the desired size. This reorients the polymer and gives blown film strength in the transverse direction as well as the machine direction. As the tube ascends, it cools and solidifies, creating a bubble. The bubble’s size and the air volume control the thickness and width of the film.
The next phase involves the film being gently collapsed by a collapsing frame into a lay-flat form. This flattened tube of film is then carefully wound onto reels, creating rolls that are ready for subsequent cutting, printing, and finishing processes. The winding must be consistent to avoid defects and ensure uniformity in the final product. Each of these steps is meticulously monitored to maintain the highest standards of quality throughout the manufacturing cycle.
Request a Quote
Request a Quote
Maintaining Consistency and Quality in Blown Film Products
Maintaining consistency and quality in blown film products is of paramount importance to ensure that the films meet the specific requirements of their intended applications. The quality of the raw materials is the cornerstone for the final product’s properties. Selecting the appropriate resin grades and additives can significantly influence the film’s optical clarity, strength, flexibility, and barrier properties.
The process of blown film extrusion demands precise temperature control throughout the extrusion process. This level of precision is crucial as it directly affects the polymer’s melting behavior and flow characteristics, which in turn determines the uniformity of the film.
Furthermore, the cooling phase is equally critical. The rate at which the film is cooled can alter its mechanical properties, such as thickness and strength. Controlled air flow around the bubble ensures even cooling, contributing to the film’s dimensional stability and preventing irregularities that could compromise its quality.
Quality Control Measures in Blown Film Extrusion
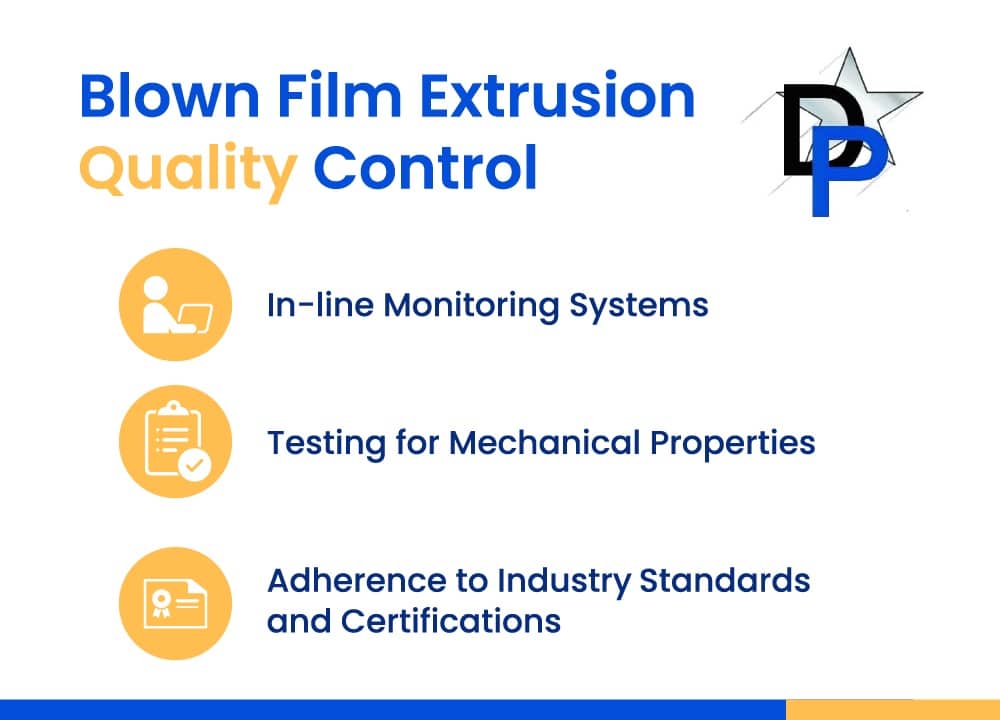
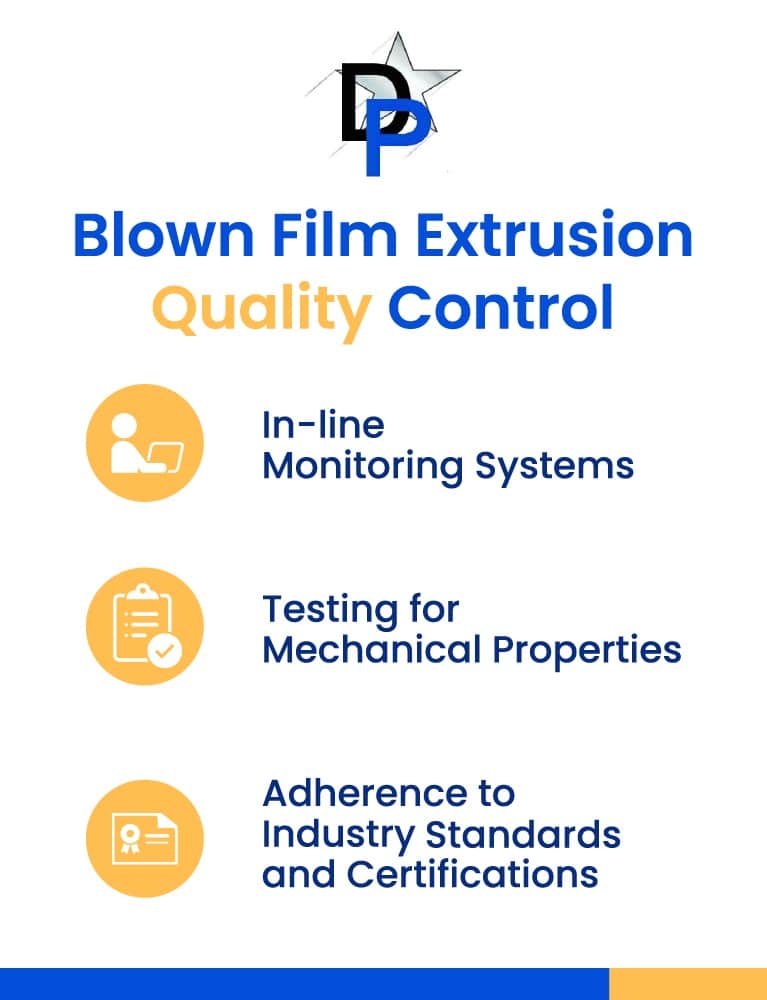
Quality control measures in blown film extrusion are pivotal in ensuring that the final product meets the required specifications and standards. These measures include a range of techniques and technologies designed to monitor and regulate the quality of the plastic films as they are produced.
In-line monitoring systems are employed to continuously check film thickness and width during the extrusion process. This real-time data allows for immediate adjustments, ensuring uniformity and minimizing material waste.
Testing for mechanical properties is another cornerstone of quality control. This involves assessing the tensile strength, elongation, and puncture resistance of the films, which are critical for their performance in various applications.
Adherence to industry standards and certifications is also a fundamental aspect of the quality control process. Many industries require certifications such as Food and Drug Administration (FDA) approvals for food-grade films, ISO standards for medical applications, or International Safe Transit Association (ISTA) tests to ensure packaging film’s ability to withstand stress during transportation. These rigorous quality control measures are a testament to a manufacturer’s commitment to excellence and customer satisfaction.
The Importance of Manufacturing Processes in Determining Film Quality
Addressing challenges in producing high-quality plastic films requires an in-depth understanding of the manufacturing process. Manufacturers must employ stringent controls to ensure that the films meet exacting standards, as these products are often used in applications where clarity and uniformity are essential.
How manufacturing controls lead to better performance in final applications is demonstrated through the end-use of the film products. For instance, in the medical sector, films must meet strict regulations and exhibit high barrier properties. In the food and beverage industry, flexible packaging films need to maintain freshness while presenting a visually appealing product. Thus, the precision of the manufacturing processes directly translates to the efficacy and suitability of the plastic films in their intended uses, making the process a cornerstone of quality assurance.
Innovations in the Blown Film Industry
The blown film industry has witnessed significant advancements in extrusion technology that have led to improvements in the properties of the resulting films.
New Extruder Designs and Enhanced Die Geometries
These new enhancements allow the capability of producing films with better barrier properties, clarity, and strength, which are crucial for packaging applications. These technological upgrades have allowed manufacturers to meet the evolving demands of various industries, such as food packaging that requires films with specific oxygen or moisture barriers.
Automation and Control Systems
Automations and control systems have also revolutionized the blown film manufacturing process. Manufacturers now employ sophisticated software and sensors that allow for precise control over every aspect of production, from extrusion speed to air flow. This automation ensures consistent film thickness and quality, reduces material waste, and increases overall efficiency.
Sustainability Measures
In terms of materials, there has been a push towards developing new polymer blends and additives that enhance film characteristics, such as UV resistance, biodegradability, and recyclability, aligning with the industry’s move towards sustainability.
Dallas Plastics’ Approach to Blown Film Extrusion
Dallas Plastics employs a meticulous approach in its blown film extrusion process, underpinning its reputation for producing films of exceptional quality. The cornerstone of this approach is sourcing certified prime resins and designing custom films that meet the precise requirements of their customers.
State-of-the-art extrusion equipment and cutting-edge technology are hallmarks of Dallas Plastics’ manufacturing capabilities. This investment in advanced machinery allows for precise control over the extrusion process, resulting in films with consistent thickness and superior mechanical properties. Advanced sensors and automated control systems are used to gather real-time data, allowing for adjustments that ensure exceptional uniformity throughout the film manufacturing cycle.
Moreover, Dallas Plastics’ quality assurance team employs rigorous testing procedures at every stage of production. This includes in-line monitoring as well as extensive mechanical property tests performed on finished films to meet or exceed relevant industry standards. With over 30 years of industry leadership, we’ve established a reputation for exceeding customer expectations with our relentless focus on service and quality.
Our robust quality control measures are a testament to its dedication to excellence. Every step of our manufacturing process is meticulously monitored, from the selection of top-tier raw materials to the employment of advanced in-line monitoring systems that measure film thickness and width.
Get High-Quality Films Tailored to Your Needs
Understanding the complexities of blown film extrusion is crucial for manufacturers, quality assurance professionals, and procurement managers dedicated to sourcing superior plastic film products. Dallas Plastics stands at the forefront of this industry, harnessing cutting-edge technologies and stringent quality control measures to deliver films that meet the exacting standards required by medical, industrial, and food and beverage applications.
Dallas Plastics stands out as a leader in producing blown film products catered to the stringent demands of the medical, industrial, and food and beverage sectors. Their expertise is evident in the precision and care taken to meet the unique requirements of these industries, where film quality is not just about appearance but also about performance and safety. The company’s track record is marked by an unwavering commitment to customer satisfaction, ensuring that each product delivered meets the highest standards of reliability and quality.
Our commitment to excellence is evident in every product we create. We employ cGMP guidelines and use prime certified materials to ensure that our blown film products are not only consistent and high quality but also tailored to the unique needs of our diverse clientele.
Choose Dallas Plastics as your trusted partner for all your blown film needs. Let us put our expertise to work for you, ensuring that your products are protected and presented with the utmost quality. Reach out to us today to request a quote, and together, we’ll create packaging solutions that stand out in the crowded marketplace.