Custom poly bags play a vital role in today’s evolving packaging industry, offering versatile solutions across sectors such as medical, food, and industrial applications. As the global packaging market continues its steady rise—valued at approximately $1.17 trillion in 2023 and projected to reach $1.42 trillion by 2028 according to Smithers research—the demand for reliable, innovative, and high-quality packaging solutions remains more critical than ever. With their adaptability and efficiency, custom poly bags are a trusted packaging choice in meeting diverse business requirements.
This guide takes you behind the scenes of custom poly bag manufacturing, exploring every step that transforms raw materials into high-performance, application-specific packaging. From initial design through to production, this process requires meticulous planning, technical expertise, and cutting-edge technology—all aimed at delivering durable, customized solutions tailored to the specific needs of each client. Whether it’s food packaging requiring sanitation and safety, medical-grade films designed for sterility, or industrial-grade liners engineered for strength, the manufacturing process for custom poly bag manufacturing is both complex and precise.
Our goal is to demystify this process, highlighting key steps and innovations that drive the successful production of high-quality poly bags. By understanding how custom poly bags are manufactured, businesses can gain valuable insight into the care, precision, and expertise that go into creating a product that meets their unique packaging needs.
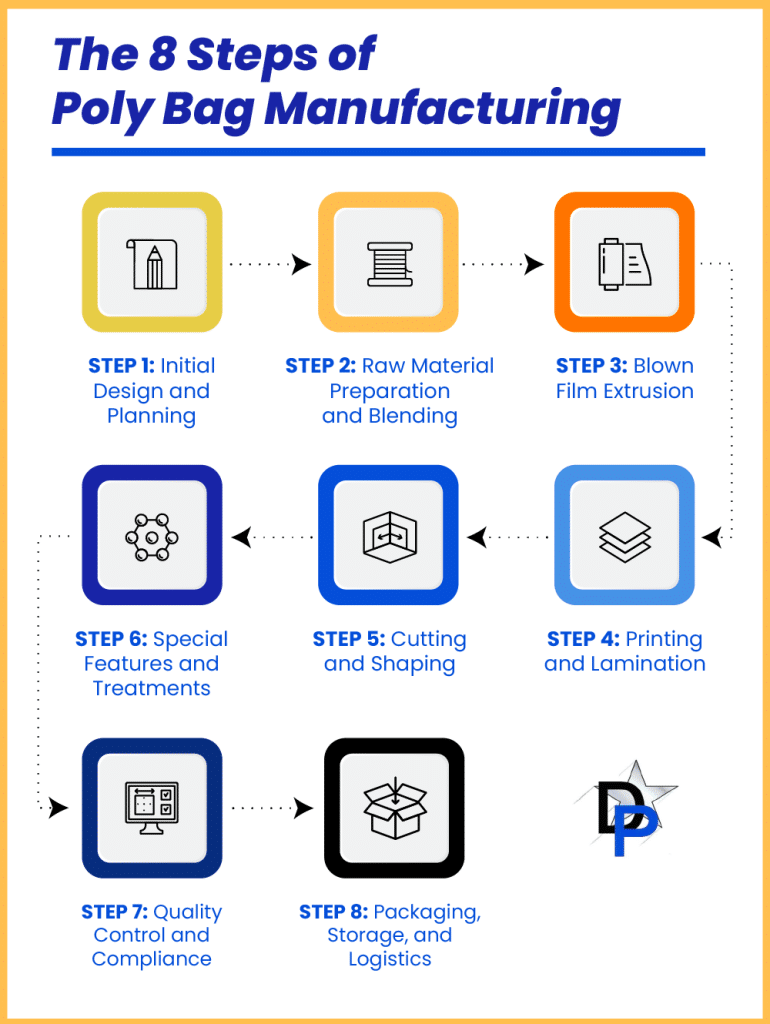
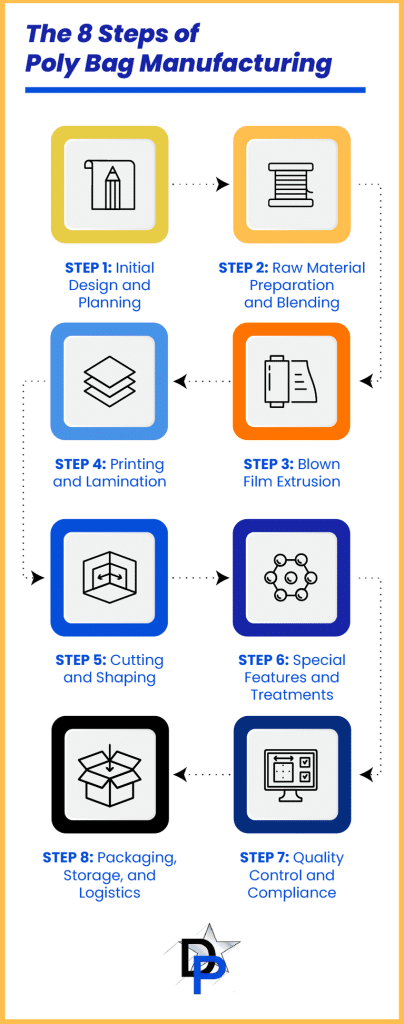
Step 1: Initial Design and Planning
The journey of creating custom poly bags starts with a thorough understanding of the client’s unique needs and objectives. During this foundational phase, manufacturers collaborate closely with clients to gather detailed information about the intended application, size, shape, and functional requirements of the packaging. Whether a client requires box liners for bulk storage or narrow tubing for specialty uses, this stage ensures every aspect—dimensions, durability, clarity, and user convenience—is carefully considered.
One of the key elements in this phase is customization. Businesses often tailor their packaging for branding purposes, incorporating logos, graphics, or text to reinforce their market presence. Additionally, printing options are explored to meet practical needs, such as product identification through barcodes. Clients may also choose between virgin plastic resins or recycled plastic resins, taking into account factors like sustainability goals, material performance, and the inclusion of special additives for strength, flexibility, or visual appeal.
By addressing these details upfront, manufacturers can produce a design blueprint that aligns with client specifications while ensuring smooth progression to subsequent stages of production. This critical step establishes a clear roadmap for creating bags that precisely meet functional and branding requirements.
Step 2: Raw Material Preparation and Blending
After finalizing the design and functional specifications, the next stage focuses on preparing the essential building blocks of specialized poly packaging. Most of these products are crafted from polyethylene resins, widely valued for their strength, flexibility, and cost-effectiveness. Selecting the right resin is crucial, as it ensures that the final product meets the unique demands of its intended application, whether that’s providing durability for industrial-grade packaging or achieving the clarity needed for food or medical uses.
To fine-tune the performance of the base material, resins are often paired with targeted additives for qualities like UV resistance or enhanced tear strength. Many clients also consider incorporating virgin plastic resins or recycled content, balancing environmental responsibility with key performance needs. Achieving a consistent resin blend is a meticulous process. Manufacturers carefully combine materials in precise ratios to ensure uniformity throughout production, preventing defects that could emerge in the later stages of manufacturing.
Step 3: Blown Film Extrusion
Blown film extrusion is a cornerstone of custom poly bag manufacturing, where raw material becomes the versatile base material that forms the backbone of these bags. This carefully controlled process begins by heating the prepared resin blend until it melts. The molten resin is then pushed through a circular die to create a continuous tube of plastic. Air is introduced from the center of the die, forming a bubble as the tube expands. This “bubble” is drawn upward, cooled, and collapsed into a flat film tube known as a layflat.
For applications requiring added durability or specialized functionality, manufacturers may use multi-layer coextrusion. This advanced technique layers different types of resins, enabling customization of specific properties for the film—such as enhanced flexibility or improved barrier performance. By precisely controlling these layers, the film can meet stringent demands across food, medical, or industrial packaging.
Maintaining consistency and precision during blown film extrusion is critical. Quality control measures track parameters like film thickness, strength, and uniformity. These checks ensure that the film will move smoothly into later stages such as cutting, shaping, or printing, all while meeting the client’s specifications.
Step 4: Printing and Lamination (If Required)
Once the tubular film is produced, certain customization steps—such as flexographic printing or lamination—may be introduced to elevate both functionality and branding. Printing, a popular option, is typically done using flexographic presses. This high-speed, precision-driven process allows manufacturers to add logos, product information, barcodes, and other branding details directly on the film. It’s especially favored for creating vivid colors and crisp details required in medical, industrial, and food packaging.
For tasks that demand added durability or specialized finishes, lamination is employed. This involves bonding multiple film layers to achieve unique protective qualities or an upscale look. From strengthening the bag’s resistance against moisture to providing a more robust, multi-layer structure, lamination can be a key advantage for packaging delicate or high-value items. Advanced processes also align these features with Form, Fill, and Seal (FF&S) technology, ensuring an efficient fit in automated packing lines.
Step 5: Cutting and Shaping
After the film has been produced, printed, or laminated, it proceeds to the cutting and shaping phase. The layflat film is carefully converted into various bag styles—bags on rolls, box liners, drum liners, or shrink film—using high-precision cutting equipment. This ensures each product adheres to the exact specifications defined in the planning phase.
Sophisticated machinery helps create uniform seal strengths, precise perforations for easy tearing, and optional custom wind configurations, such as perforated rolls or fan-folded stacks. By tailoring these aspects, manufacturers deliver products that stand up to their intended usage, whether it’s storing bulk items, lining containers, or transporting delicate items.
This stage highlights the importance of consistent dimensions and robust seals: any variation could compromise functionality, leading to issues like leaks or tearing. Through exact shaping and customization, each poly bag is primed to handle real-world conditions efficiently and reliably.
Step 6: Special Features and Treatments
Custom poly bags can be enriched with unique features and treatments to meet specialized demands in various industries. These enhancements may include antimicrobial coatings for contamination control, high-clarity resin blends for better product visibility, or thickness adjustments to improve tear and puncture resistance. By incorporating these tailored features, manufacturers deliver value that aligns with critical requirements in food, medical, or industrial applications.
Additionally, eco-conscious businesses can opt for biodegradable materials or resin blends designed to reduce environmental impact. Thickness customization helps balance material usage with performance needs—thinner bags for lighter loads and thicker, reinforced versions for more demanding tasks. Such targeted upgrades provide practical solutions, ensuring the packaging performs reliably under a variety of conditions.
For medical and food settings, these specialized features are particularly valuable. They not only comply with strict hygiene standards, but also enhance user confidence and product integrity. From upgraded barrier properties to advanced safety treatments, every detail is fine-tuned to serve both practical and regulatory considerations.
Step 7: Quality Control and Compliance
Ensuring premium quality is pivotal in custom poly bag manufacturing, underscored by rigorous testing and adherence to regulations such as cGMP (current Good Manufacturing Practices). Throughout production, samples undergo thorough assessments for tear resistance, seal integrity, thickness uniformity, and dimensional accuracy. For industries like healthcare and food, additional evaluations—like contact safety or sterilization compatibility—further validate the packaging’s readiness for specialized use.
Many products also require external certifications to confirm alignment with industry standards. These credentials offer peace of mind that the packaging meets the functional, hygienic, or safety demands of its intended market. By enforcing stringent quality checks at every stage, manufacturers uphold reliability, safety, and performance, paving the way for end-users to trust these packaging solutions in critical environments.
Step 8: Packaging, Storage, and Logistics
After custom poly bags pass quality checks, they move into packaging, storage, and ultimately, delivery. Depending on the product type—be it drum liners, box liners, or mailer films—bags are neatly organized and packaged to prevent damage during transit. Labeling each package with product details and order information streamlines inventory management and helps avoid errors.
For large-volume shipments, palletized storage supports efficient ordering and straightforward retrieval when demand spikes. This well-structured system fosters timely deliveries, an aspect crucial for industries that operate on tight timelines or rely on just-in-time manufacturing. Reliable partnerships with shipping providers help ensure that products arrive in top condition and on schedule, reinforcing a manufacturer’s commitment to dependable service.
Benefits of Custom Poly Bags in Various Industries
Custom poly bags offer targeted solutions that surpass the capabilities of off-the-shelf alternatives. For instance, they can be designed to preserve freshness and maintain food safety—essential attributes in the food sector—thereby reducing spoilage and boosting product appeal. In the medical field, where contamination control is paramount, these tailored bags can feature tear resistance and sterility safeguards, aligning with strict hygienic standards as seen in medical-grade applications.
On the industrial front, robust liners and specialized shrink films are indispensable for tasks requiring reliable performance in harsh or demanding environments. Reinforced materials ensure puncture resistance and maintain structural integrity for bulk or heavy-duty applications. Customized thickness, color, and branding elements further optimize the packaging, allowing businesses to streamline processes, meet compliance requirements, and bolster their market presence.
Ultimately, custom poly bags empower businesses with versatile packaging solutions that strike the right balance between functionality, durability, and design. Whether safeguarding consumables, protecting sterile equipment, or maintaining heavy industrial loads, these bags consistently deliver the performance and reliability industry professionals need.
Request a Quote
Final Thoughts on Custom Poly Bag Manufacturing
The production of custom poly bags is a meticulous journey that combines innovative technology, skilled craftsmanship, and a deep understanding of diverse industry requirements. From the initial design stage to the final quality checks, every step is shaped by a commitment to delivering high-performing, specialized packaging solutions. This integrated approach ensures packaging consistency, durability, and alignment with strict guidelines for food, medical, and industrial applications.
Whether you need food-grade solutions for product preservation, medical-grade films for sterile environments, or heavy-duty liners that withstand the rigors of industrial use, custom poly bags offer a dependable option. Embracing a customized approach to packaging means investing in protection, usability, and a perfect synergy between your products and their packaging.
To learn more about how these solutions can support your business goals, contact Dallas Plastics for a personalized consultation. Our team offers expert guidance from design through delivery, helping you secure packaging that upholds performance standards—and your brand reputation.