In today’s rapidly evolving packaging industry, multi-layer co-extruded films stand out as a forefront solution, offering unmatched barrier properties, strength, and flexibility.
These advanced films, which incorporate multiple layers of materials each tailored for specific functions, have revolutionized packaging across a variety of sectors. These films are the result of years of research and development dedicated to harnessing the unique properties of different polymers, blended into a single film structure that outperforms traditional materials.
As industries continually seek more efficient and sustainable packaging options, understanding the technical properties and competitive advantages of these films is crucial. Dallas Plastics, as a leader in blown film products and technologies, is at the vanguard of these developments, providing cutting-edge solutions that cater to the demanding needs of modern packaging. This guide will equip you with the essential knowledge and insights needed to leverage the benefits of multi-layer co-extruded films in your operations.
What Are Multi-Layer Co-Extruded Films?
Multi-layer co-extruded films represent a sophisticated advancement in packaging technologies, designed to meet the complex demands of modern industries. These films are crafted through a process called co-extrusion, wherein multiple layers of different polymers are simultaneously extruded to form a single, multi-layered film.
This innovative technique allows for the combination of various material properties in a single film, such as enhanced barrier protection, strength, and flexibility.
At its core, a multi-layer co-extruded film is engineered by blending two or more polymeric materials. Each layer is tailored to confer specific attributes, which when combined, provide a composite material that outperforms traditional mono-layer films in both functionality and performance. The versatility of the layer compositions can be adjusted to suit particular barrier and mechanical properties needed for specialized packaging.
Brief History and Evolution in the Packaging Industry
The evolution of multi-layer co-extruded films is marked by significant milestones that highlight their growing importance in packaging. Initially developed to improve the shelf life and integrity of food products, these films have diversified to accommodate a wide range of applications across various sectors.
Over time, advances in polymer sciences and extrusion technology have allowed manufacturers to add more layers and thereby, fine-tune the protective and mechanical characteristics of these films to better cater to the needs of increasingly sophisticated products and demanding conditions.
This progression has made multi-layer co-extruded films a cornerstone in the field of advanced packaging solutions, demonstrating their pivotal role in enhancing product preservation and improving the cost effectiveness of packaging systems. The adoption of these films continues to reshape the landscape of packaging technologies, offering robust, customized solutions that can be tailor-made for a wide array of industrial applications.
Manufacturing Process of Co-Extruded Films
The manufacturing process of multi-layer co-extruded films is a sophisticated operation that requires precise technology and expertise. Central to this process is co-extrusion technology, which enables the production of films with multiple layers of different materials. This section delves into the step-by-step journey from choosing the right resins to the actual production of the films, alongside an examination of the key technologies employed.
Co-extrusion refers to the simultaneous extrusion of two or more layers of different polymers through a single die to form a multi-layered film. This advanced technology allows the production of films that combine various properties which single-layer films cannot achieve. The result is a tailored packaging solution with enhanced functionalities such as improved barrier properties, increased strength, and better aesthetic appeal.
Step-by-Step Process from Resin Selection to Film Production
- Resin Selection:
- Identification of the appropriate resin types based on desired film properties (e.g., barrier performance, mechanical strength, clarity).
- Blending of different resins to achieve optimal properties in the final film.
- Extrusion:
- Melting and conveying the resin blends through multiple extruders.
- Each extruder is assigned to push a specific layer of material through the die.
- Die Casting:
- The molten resins are forced through a co-extrusion die, which carefully layers and combines them into a single film structure.
- Adjustments in the die ensure even distribution and thickness across the layers.
- Cooling and Solidifying:
- Rapid cooling of the film as it exits the die to solidify the multi-layer structure.
- Control of cooling rates is crucial to prevent defects and maintain film clarity.
- Winding:
- The solidified film is wound onto large reels for subsequent processing and cutting.
Key Technologies Used
- T-Die Process:
- Utilized in flat film extrusion.
- Enhances the uniformity and quality of the film layers across wide widths, ideal for packaging applications.
- Blown Film Extrusion:
- Used for producing films with superior strength and barrier properties.
- The film is extruded through an annular slit die, vertically inflated into a bubble and cooled by high-velocity air.
The technologies and precision involved in the manufacturing process of co-extruded films ensure that these advanced packaging solutions can meet the specific needs of various industry applications effectively. By leveraging co-extrusion, manufacturers can optimize the film’s performance, making them suitable for a range of demanding packaging challenges.
Technical Properties and Advantages
Multi-layer co-extruded films, often recognized for their versatility in various applications, boast exceptional technical properties that set them apart from traditional packaging materials. The essential characteristics such as barrier properties, strength, flexibility, temperature, and chemical resistance, contribute to their growing preference in demanding packaging domains.
Barrier Properties: Moisture, Gas, and Light
These films excel due to their superior barrier qualities against moisture, oxygen, and light, pivotal in extending the shelf life of perishable products and sensitive goods. The multi-layer structure allows the integration of specific materials tailored to block out different elements, significantly reducing product spoilage and quality degradation.
Strength and Flexibility Comparisons to Traditional Films
Compared to traditional single-layer films, co-extruded films offer enhanced mechanical strength and elasticity, allowing them to withstand harsh handling and environmental conditions without compromising their integrity. This strength does not sacrifice flexibility; the films can adapt to various shapes and sizes, ensuring comprehensive protection and packaging versatility.
Temperature and Chemical Resistance
The resilience of these films against extreme temperatures and adverse chemical interactions is critical, especially in industries like food processing and pharmaceuticals. These properties ensure that the films can maintain their structural integrity and performance characteristics under various operational conditions, contributing further to the safety and stability of the packaged products.
Competitive Advantages Over Traditional Packaging Materials
Multi-layer co-extruded films offer a host of competitive advantages when compared to traditional packaging materials. These advantages not only result in superior performance but also contribute to overall cost savings and environmental sustainability, which are key considerations in today’s market.
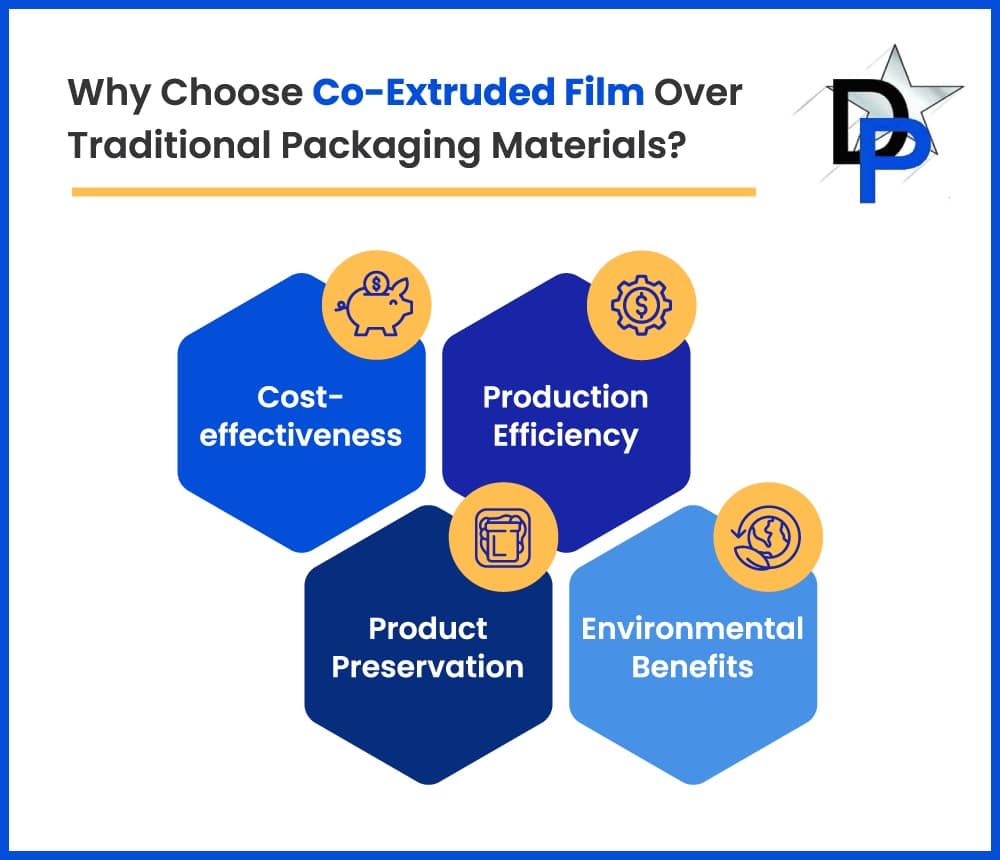
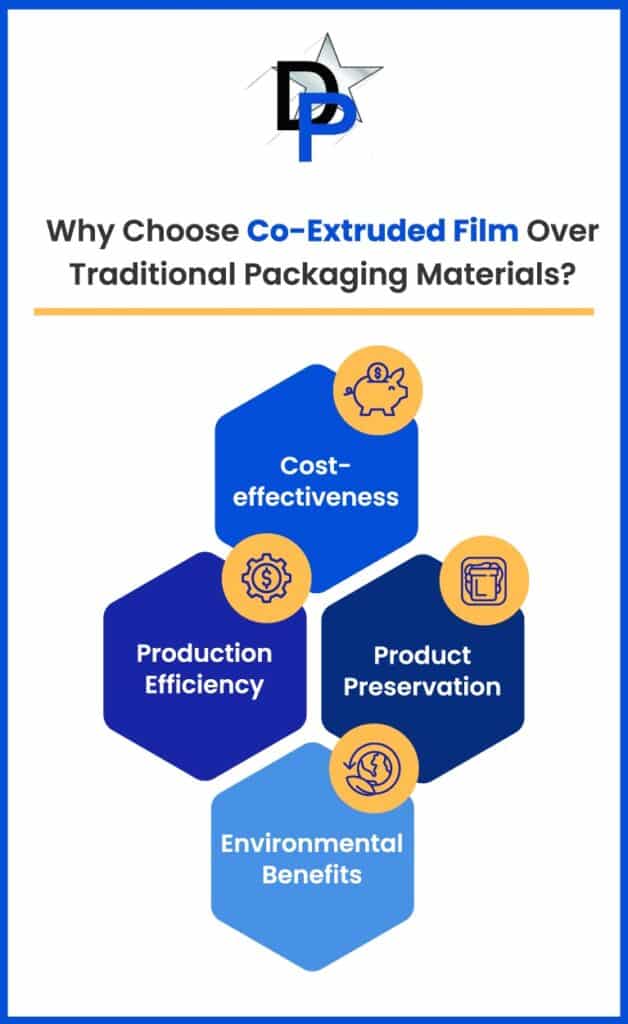
Cost-effectiveness and Efficiency in Production
The production of multi-layer co-extruded films is highly efficient, leading to lower production costs over time. This efficiency arises from the ability to perform multiple extrusions during a single production phase, which minimizes waste and maximizes output. The streamlined process also reduces labor costs and energy use, making it a more economical choice for large-scale applications.
Superior Product Preservation Capabilities
Thanks to the enhanced barrier properties of multi-layer co-extruded films, they excel in product preservation. These films are adept at protecting contents from moisture, gas, and light – the primary culprits in product degradation. This attribute is particularly beneficial in the food and beverage industry, where extended shelf life is crucial. By keeping contents in optimal condition longer, these films help reduce waste and improve consumer satisfaction.
Environmental Benefits and Sustainability Aspects
In addition to their production and preservation advantages, multi-layer co-extruded films are often more sustainable than their traditional counterparts. Many such films are designed for easier recycling, which encourages compliance with global environmental standards and appeals to eco-conscious consumers and businesses. Moreover, the durability and strength of co-extruded films reduce the need for secondary packaging, further cutting down on material use and waste.
These factors clearly demonstrate the superiority of multi-layer co-extruded films over traditional packaging materials, making them a smart choice for businesses looking to enhance operational efficiency, product integrity, and sustainability commitments.
Request a Quote
Request a Quote
Applications Across Various Industries
Multi-layer co-extruded films are highly versatile, making them an ideal choice for a variety of sectors requiring advanced packaging solutions. The properties of these films cater specifically to the complexities and demands of different industries, ranging from food and beverage to pharmaceuticals and industrial goods. Understanding how these films serve different sectors can help businesses pick the right type of packaging that aligns with their product needs and regulatory requirements.
Food and Beverage Industry: Enhancing Shelf Life and Product Safety
In the food and beverage sector, the primary concern is preserving the freshness and extending the shelf life of products. Multi-layer co-extruded films provide excellent barrier qualities against moisture, oxygen, and light, all of which can significantly degrade food items. For example, snacks and ready-to-eat packaged foods benefit immensely from this technology, as these films maintain the crispness and taste integrity from production to pantry. Moreover, the ability of these films to customize thickness and permeability makes them an optimal choice for tailored packaging needs, such as modified atmosphere packaging, further safeguarding food quality during extended storage periods.
Pharmaceuticals: Ensuring Drug Safety and Integrity
For pharmaceuticals, packaging must conform to stringent standards to maintain drug efficacy and safety. Multi-layer co-extruded films are designed to isolate contents from external elements that could alter the product, such as light and humidity. This ensures that the pharmaceuticals are well-protected from external environmental factors that could compromise their chemical stability. Additionally, these films offer excellent resistance to harsh chemicals, making them suitable for safely transporting and storing sensitive medical products, including serums, tablets, and diagnostic kits.
Industrial Goods: Providing Durability and Protection
The industrial sector often deals with the transport and storage of goods under varied environmental conditions which require robust packaging solutions. Multi-layer co-extruded films are valued in this industry for their strength and flexibility, which are critical for the protection of heavy-duty items from mechanical damage and harsh weather conditions. Whether it’s automotive components, machinery parts, or construction materials, these films can be customized to provide extra thickness and resistance, ensuring that products reach their destination in pristine condition.
By adopting multi-layer co-extruded films, industries can leverage the high-performance packaging to meet specific needs, ensuring product safety, longevity, and compliance with industry standards. This makes them an invaluable asset across diverse sectors in modern packaging applications.
Future Trends and Innovations in Co-Extruded Films
The realm of multi-layer co-extruded films is continuously evolving, driven by the quest for more advanced packaging solutions. Innovations in this field are not only enhancing the technical capabilities of these films but are also focusing on reducing environmental impact. Here’s a look at some of the notable future trends and innovations in co-extruded films.
Advanced Polymer Blends for Enhanced Performance
Developments in polymer science are central to the future of co-extruded films. Advanced polymer blends are being designed to tailor the properties of films more precisely to specific applications. These new blends can offer improved:
- Barrier properties: Enhanced formulations are achieving greater resistance to moisture, oxygen, and light, which is crucial for packaging applications that require extended shelf life.
- Mechanical strength: Innovations in polymer structures are leading to films that are both stronger and more flexible, reducing the risk of tears or punctures during packaging, handling, and transport.
- Thermal resistance: With better thermal properties, these films can withstand higher temperatures during processing and storage, making them more versatile for a variety of products.
Innovations in Recyclability and Environmental Impact Reduction
Sustainability is becoming a necessary consideration in the development of packaging materials. Co-extruded films are no exception, and recent innovations are focused on making these films more environmentally friendly:
- Recyclable materials: Research is ongoing into multilayer films that can be easily recycled, addressing the challenge of separating different polymer layers in traditional co-extruded films.
- Biodegradable options: Emerging technologies are exploring the use of biodegradable polymers in co-extrusion processes to produce films that can break down naturally, reducing long-term waste.
- Reduction of production waste: New manufacturing techniques are being developed to reduce waste during the film production process, contributing to a more sustainable production cycle.
These advancements in multi-layer co-extruded film technologies not only promise improved performance but also align with global environmental sustainability goals. By integrating innovative polymer blends and embracing greener production practices, the future of co-extruded films looks both high-performing and sustainable.
Choosing the Right Co-Extruded Film for Specific Needs
Selecting the appropriate multi-layer co-extruded film for your packaging needs involves careful consideration of several factors to ensure optimum performance. Understanding these variables can help professionals tailor choices to specific industry requirements, enhancing protection and functionality.
Factors to Consider When Selecting Films
- Application Purpose: Define what primary protection or function the film needs to serve. This could range from UV protection, moisture barrier, to puncture resistance. Identifying the main function will guide the selection process significantly.
- Physical Properties: Consider the strength, flexibility, and durability required. Different applications demand varying degrees of each attribute. For instance, industrial goods might need tougher films to withstand harsh handling.
- Chemical Compatibility: Assess the film’s resistance to chemicals it might encounter. This is particularly crucial in industries like pharmaceuticals where the packaging might interact with various substances.
- Regulatory Requirements: Ensure that the selected film complies with all relevant industry regulations and standards. Non-compliance can lead to significant financial and reputational damage.
How Dallas Plastics is Pioneering Advanced Packaging Solutions
Dallas Plastics has established itself as a front-runner in the field of advanced packaging solutions through its innovative approach to multi-layer co-extruded films. Leveraging state-of-the-art technology and in-depth industry knowledge, Dallas Plastics crafts high-performance films that meet the precise needs of various industries.
Unique Capabilities of Dallas Plastics
The heart of Dallas Plastics’ innovation lies in its specialized co-extrusion techniques and formulations. By using unique polymer blends and mastering the intricacies of multi-layer film design, the company creates products that not only meet but often exceed industry standards for quality and performance. Features such as enhanced barrier properties, superior tensile strength, and optimal flexibility are just the start. Each film is engineered to provide specific benefits, such as increased shelf life for food products or heightened protection for sensitive pharmaceuticals.
Dallas Plastics’ commitment to sustainability also sets them apart. They continuously work on improving the environmental impact of their films, focusing on the development of recyclable and biodegradable options without compromising the quality and integrity of the packaging.
Customer Support and Technical Assistance
Understanding the complexities of modern packaging needs, Dallas Plastics offers exceptional customer support to guide clients through the selection and customization process. Their team of experts is readily available to provide consultations, share insights into the latest industry trends, and help troubleshoot any challenges clients might face.
Moreover, Dallas Plastics doesn’t just sell products; they provide solutions. Clients can expect comprehensive technical assistance, ensuring that the films they choose perfectly match their operational and functional requirements. Whether a client is dealing with a challenging packaging environment or needs to meet stringent regulatory requirements, Dallas Plastics’ support team is equipped to tailor solutions that align with specific goals and constraints.
Engaging with Dallas Plastics for Custom Packaging Solutions
Engaging with Dallas Plastics for tailored packaging needs begins with understanding your specific requirements. Dallas Plastics specializes in designing and producing custom multi-layer co-extruded films tailored to the unique needs of each industry. Whether you are involved in food and beverage, pharmaceuticals, or industrial goods, they offer detailed consultations to identify the perfect film solutions that enhance both product preservation and cost-efficiency.
Steps for Consultation and Customization
- Initial Consultation:
- Discuss your product requirements, potential challenges, and specific goals.
- Gain insights into the various options of co-extruded films Dallas Plastics provides.
- Material Selection:
- Receive expert advice on selecting the appropriate materials based on your product’s barrier needs, strength, flexibility, and sustainability requirements.
- Prototyping and Testing:
- Dallas Plastics facilitates small-scale production trials to test the films under real-world conditions ensuring they meet all specified requirements.
- Production and Implementation:
- Once the prototype meets approval, full-scale production commences.
- Continuous support and adjustments are provided to guarantee optimal performance.
- Follow-Up Services:
- After delivery, Dallas Plastics remains available for further modifications, performance evaluations, and any additional needs that arise.
Drive Innovation and Efficiency in Your Packaging Processes
Understanding the multifaceted benefits and applications of multi-layer co-extruded films is crucial for any business aiming to enhance its packaging strategies. These films offer a superior blend of barrier properties, durability, and cost-effectiveness, making them an ideal choice for industries demanding high-performance packaging solutions.
At Dallas Plastics, we are committed to providing not just products but complete packaging solutions tailored to meet the specific needs of your industry. Request a quote from Dallas Plastics. Let us assist you in exploring the various applications of our advanced co-extruded films and help you achieve the packaging excellence your products deserve.