In today’s industrial landscape, high-quality plastic films are critical across various sectors, including medical, food and beverage, and broader industrial applications. Understanding the intricate processes involved in polymer production is essential for industry professionals who depend on the reliability and quality of these materials.
This comprehensive guide explores the core polymer production processes and the chemical reactions that underpin the creation of plastic films, with a particular focus on extrusion and blowing techniques.
By exploring these methods and their impact on product quality, we aim to provide valuable insights that underscore the importance of meticulous production standards. Our discussion will not only clarify the technical aspects of polymer production but also position Dallas Plastics as a paragon of excellence and innovation in the field.
Overview of Polymer Production Processes
Polymer production involves a range of processes that transform raw materials into a variety of plastic films. The core techniques utilized in this process include extrusion and blowing, which are tailored to manufacture films with specific mechanical and chemical properties suited for diverse applications.
These processes rely on various chemical reactions that dictate the final properties of the plastic films produced. The goal of polymer production is to create high-quality plastic films that meet stringent industry standards in terms of strength, clarity, flexibility, and durability. Achieving these standards is crucial, as these films are applied across industries where reliability and safety are paramount.
Common Polymer Production Processes
Polymer production is pivotal in manufacturing sectors that demand durable and flexible materials. The two core techniques in use are extrusion and blowing. These processes involve the shaping of molten plastic into films of varying thickness and dimensions, depending on the intended application.
Extrusion Techniques
Polymer extrusion is a popular production process because of its efficiency and versatility. Here’s how it works:
- Materials Selection: Polymers such as polyethylene or polypropylene are chosen for their specific properties accommodating to end-use applications.
- Melting and Shaping: The selected polymers are fed into an extruder, which melts them. The molten polymer is then forced through a die, shaping it into a continuous profile as per requirement.
- Cooling and Solidifying: Upon exiting the die, the polymer profile is cooled and solidified into a solid shape. This process can be tailored to manufacture products ranging from simple pipes to complex multi-layer films.
Blowing Techniques
Plastic film blowing is an essential method for creating thin, flexible films commonly used in packaging materials. The steps involved include:
- Extrusion of molten polymer: Similar to the basic extrusion process, molten polymer is extruded through a circular die.
- Blowing: Air is injected into the center of the extruded tube, inflating it into a bubble. This bubble is then blown up until the polymer cools and sets into a tubular film shape.
- Flattening and Winding: The film is then flattened through rollers and wound onto reels for further processing.
Both extrusion and blowing techniques confer specific benefits and have certain limitations:
- Advantages:
- Scalability and continuous production flow, essential for high-volume manufacturing.
- Control over film thickness and size, critical for diverse applications from medical to industrial packaging.
- Disadvantages:
- Requires consistent material quality to avoid defects in the final product.
- High setup and equipment costs limit the initial investment feasibility for small-scale producers.
Understanding these processes underscores the capability to control not just the material output but also critical properties like clarity, flexibility, and strength of the plastic films. Whether for wrapping food, securing medical instruments, or covering industrial goods, efficiently managed production techniques ensure that produced films meet stringent application standards.
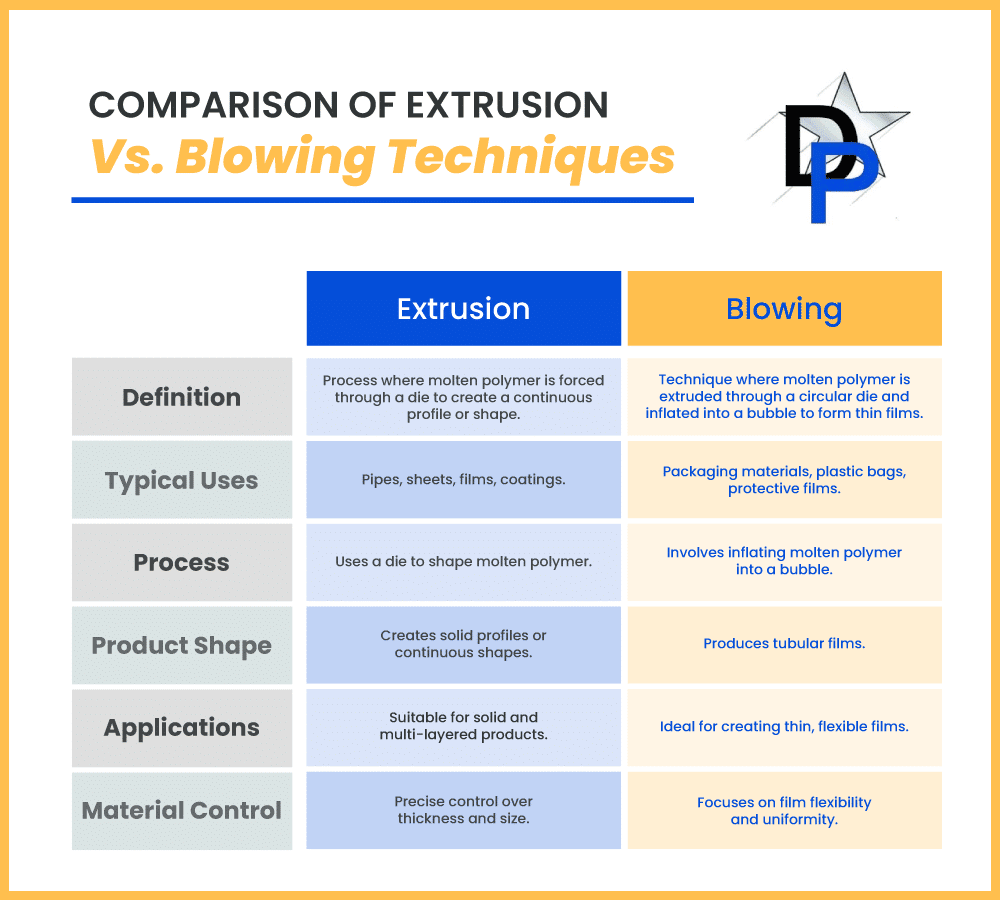
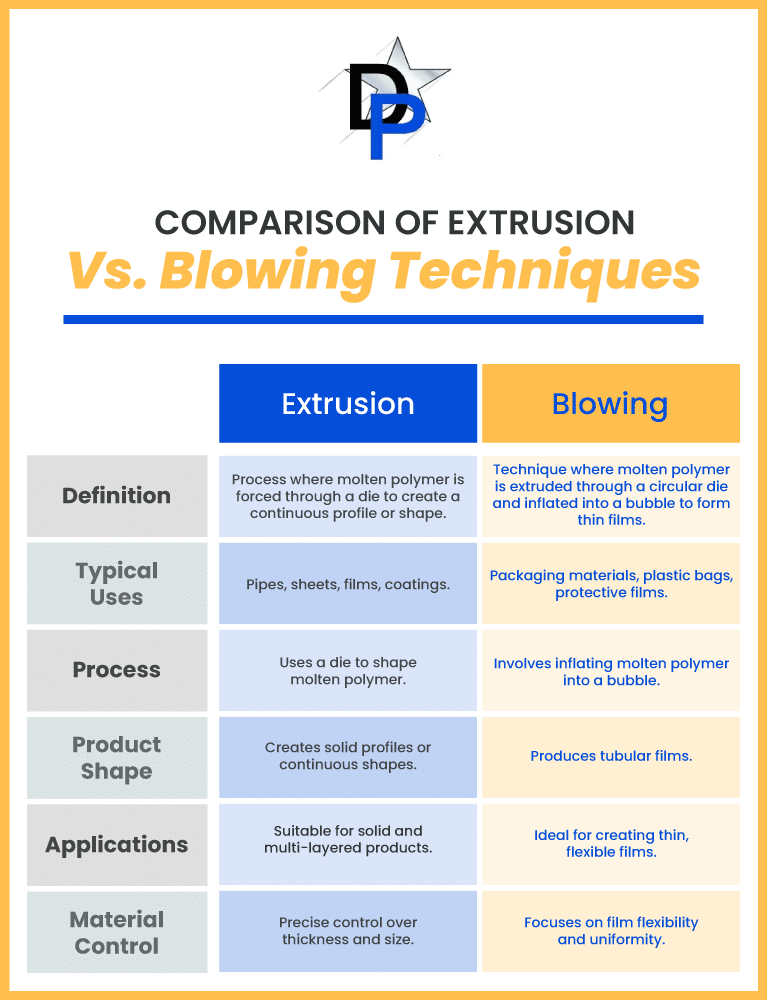
Chemical Reactions in Polymer Production
Polymer production is fundamentally rooted in chemical reactions, primarily polymerization, where monomers (small molecules) combine to form a polymer (large molecule composed of repeating units). Understanding these reactions reveals how the physical and chemical properties of the finished plastic films are determined.
Polymerization Types
Addition Polymerization:
- Involves unsaturated monomers like ethylene and propylene.
- No by-products produced, largely used for commodities like polyethylene films.
Condensation Polymerization:
- Occurs between monomers with two functional groups.
- Water or other small molecules are by-products.
- Common in the production of nylon and polyester films.
Controlling Polymer Properties
Catalysts and Initiators:
- Specially designed molecules like peroxides that trigger and speed up polymerization reactions.
- Their choice dictates the reaction rate and molecular weight of the polymer.
Temperature and Pressure:
- Precisely controlled during the polymerization process.
- Influence the polymer’s structural characteristics like tensile strength and elasticity.
This detailed management of chemical reactions ensures that polymer properties can be finely tuned to meet specific performance criteria required by diverse applications.
Importance of Quality Standards in Polymer Production
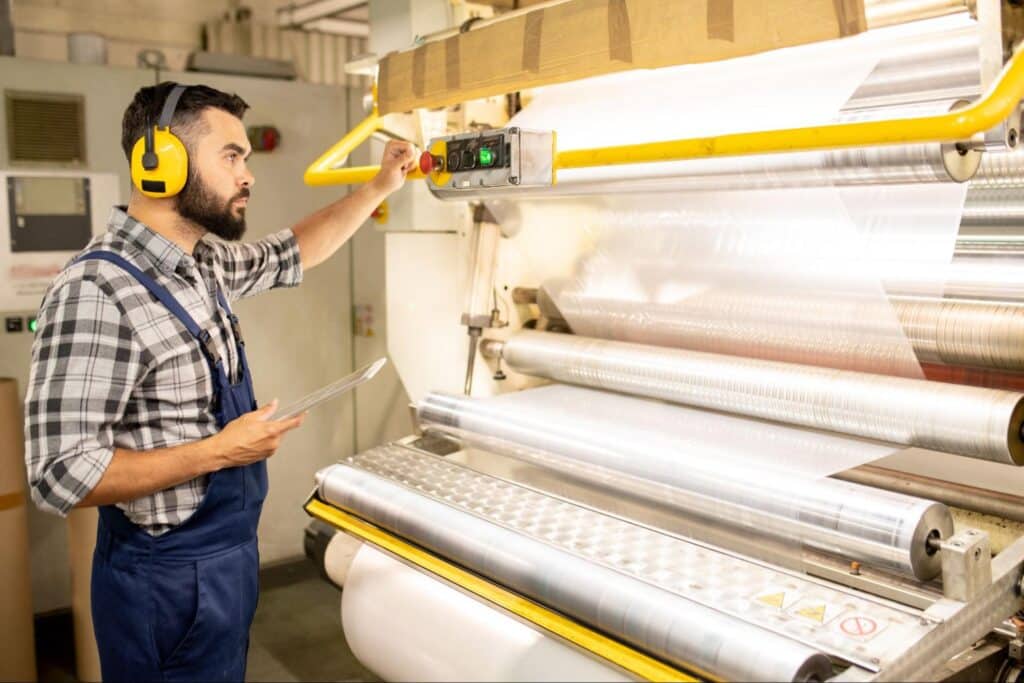
Ensuring the integrity and quality of polymer products necessitates strict adherence to quality standards. The implementation of current Good Manufacturing Practices (cGMP) guidelines is paramount in this context.
These guidelines help manufacturers control production processes and guarantee that the plastics produced meet necessary specifications for purity, strength, and compliance with safety regulations. This attention to quality is especially critical in sectors where plastics are used in safety-sensitive applications.
Role of cGMP Guidelines
cGMPs are vital in the polymer production industry as they stipulate requirements that manufacturers must adhere to during the production process. These include the proper design and maintenance of equipment, clear documentation of processes, and stringent control of production environments. By following these guidelines, manufacturers can avoid contamination, inconsistencies, and defects which are crucial to producing high-quality plastic films.
Quality’s Impact in Critical Industries
In the medical field, polymer films are used extensively for products such as sterile packaging and surgical tools, necessitating high standards of hygienic and mechanical properties to ensure patient safety. Similarly, in the food industry, where packaging films directly contact edibles, high-quality plastics are essential to prevent toxin release and ensure prolonged shelf life. In heavy industries, plastic films must possess specific chemical resistance and mechanical strength to withstand harsh environments, ensuring operational safety and durability.
Clearly, maintaining high-quality standards in polymer production is more than a compliance requirement; it directly impacts functionality, safety, and performance across various critical sectors. This underscores the importance of thorough quality checks and balances throughout the manufacturing process, enhancing the final product’s reliability and effectiveness in its specific usage.
Application of Blown Film Products in Various Industries
Blown film products are integral to a diverse range of industries, each with specific needs and regulatory standards. Their application spans from medical packaging that ensures sterility and durability, through to food-grade films designed for safety and freshness preservation, extending to robust industrial packaging solutions.
Medical Packaging Films
In the healthcare industry, the stakes for quality and precision are particularly high. Medical packaging films are used in various applications including the packaging of sterile medical devices, pharmaceuticals, and other supplies essential for health services. These films must comply with stringent sterilization requirements to prevent contamination. Features such as high barrier properties, puncture resistance, and clarity are critical to ensure safety and functionality.
Food-Grade Plastic Sheeting
The food and beverage sector relies heavily on plastic films to maintain the quality and longevity of products. These films are crafted to meet food safety regulations that restrict the migration of harmful substances into food. Attributes such as moisture barriers, resistance to tearing, and adaptability to various temperatures are essential. Plastic films used in food packaging also often possess special characteristics such as enhanced sealability and printability that aid in branding and information delivery.
Industrial Packaging Solutions
In the industrial sector, the ability of films to protect goods during storage and transportation is paramount. Blown film products used in this context are engineered for high tensile strength and impact resistance, accommodating the rigorous demands of heavy or bulky products. They also often have specific resistance to chemicals and UV radiation, ensuring long-term durability even under challenging environmental conditions.
Specialized Techniques in Plastic Film Production
Understanding the specialized techniques in plastic film production is crucial for appreciating the advanced capabilities Dallas Plastics brings to the polymer industry. Techniques such as Form, Fill, and Seal (FF&S) technology and the production of specialty and converter grade sheeting offer unique solutions that cater to specific industry needs.
Form, Fill, and Seal (FF&S) Technology
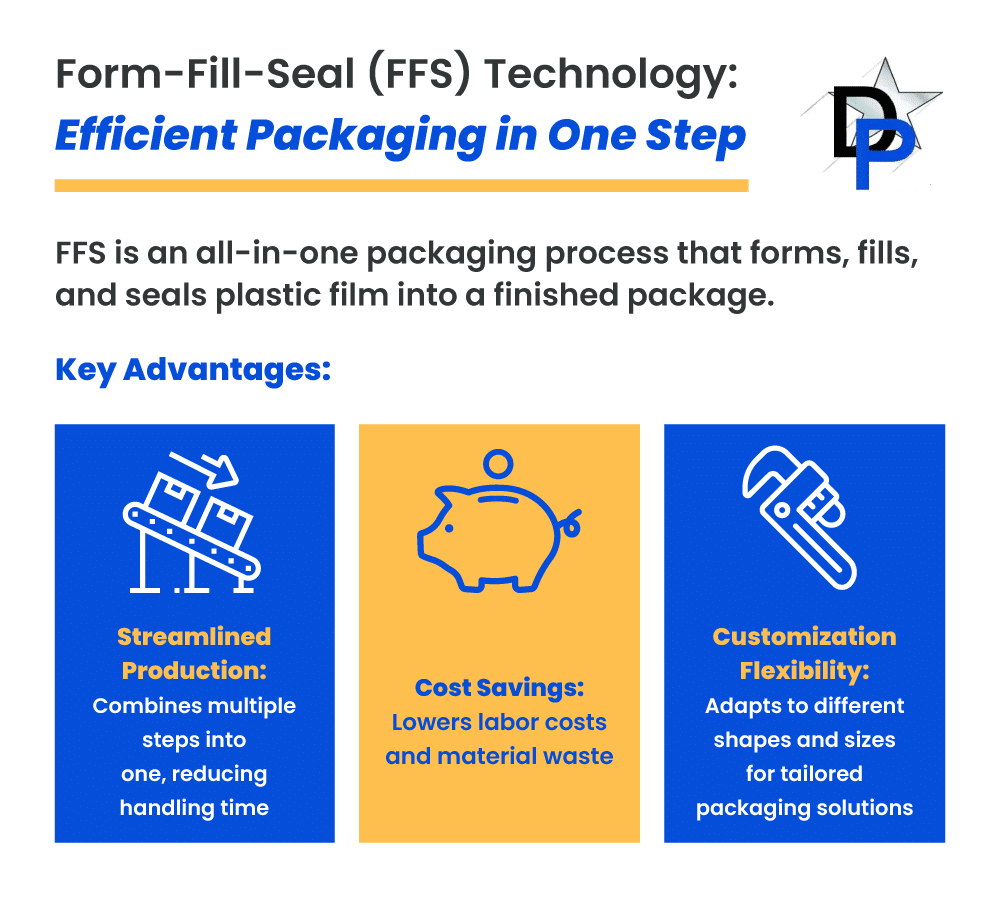
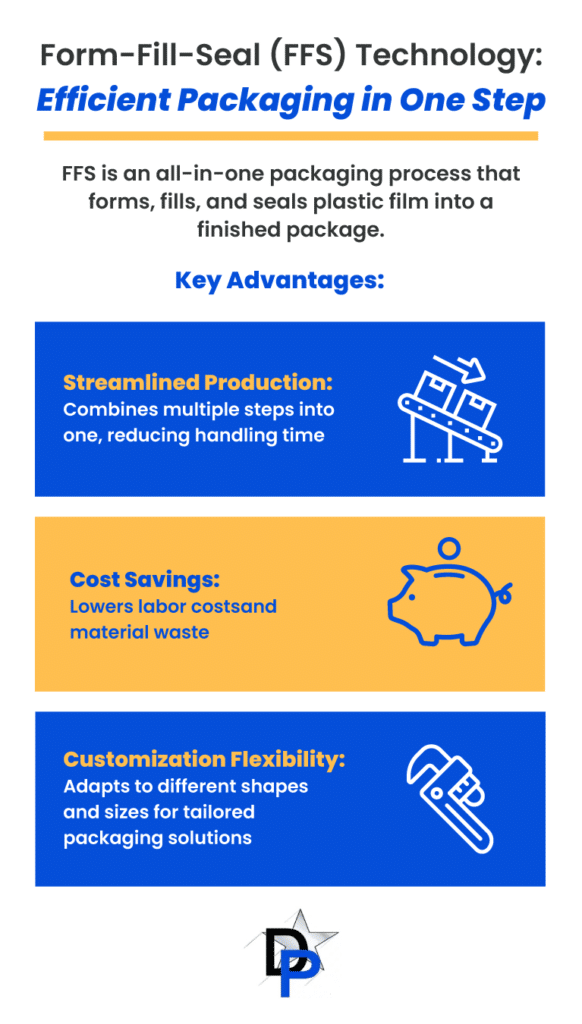
FF&S technology integrates the formation of plastic film, the filling of products, and the sealing process into one continuous operation. This integrated approach not only streamlines production but also enhances efficiency and reduces waste.
- Efficiency: The singular flow from film creation to product packaging minimizes handling and increases throughput.
- Cost-effectiveness: Reduction in labor and less material waste contribute to lower overall production costs.
- Customization: FF&S machines can be tailored to meet specific packaging requirements, adapting to varying product shapes and sizes.
Specialty and Converter Grade Sheeting
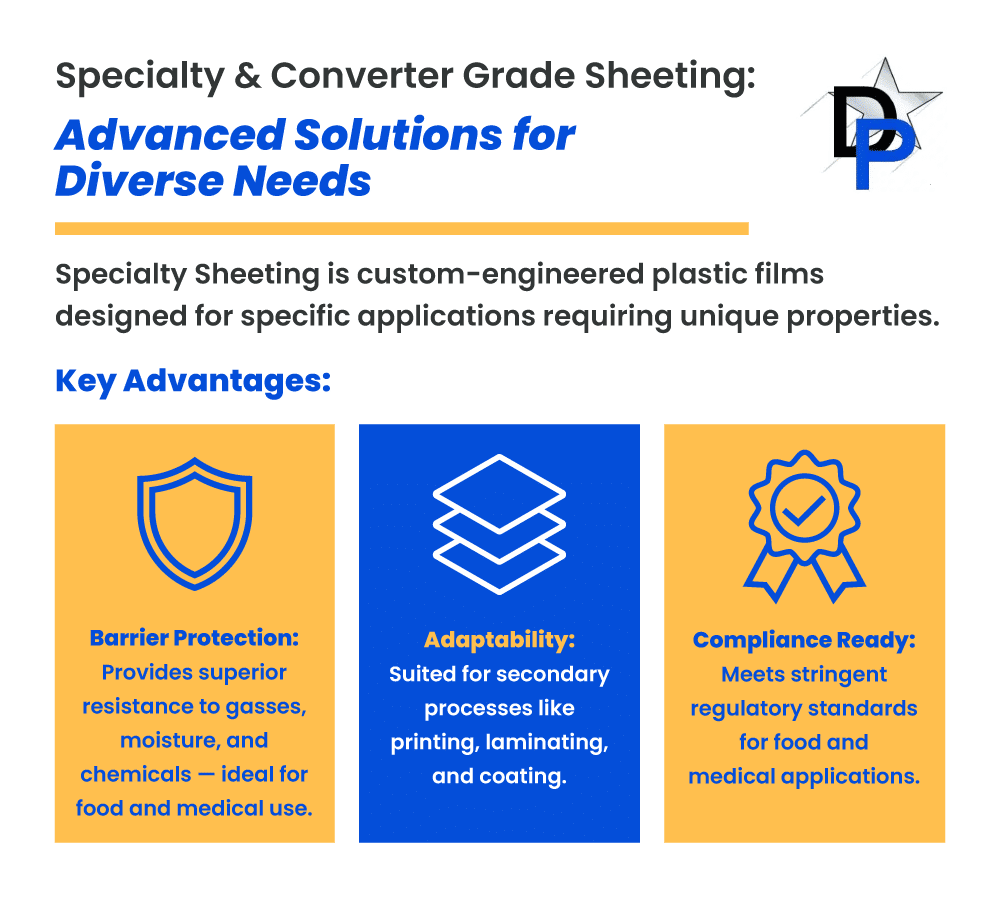

Specialty plastic films and converter grade sheeting are designed to address particular needs of various industries. These films often have enhanced properties such as increased strength, barrier protection, or ultra-clear visibility.
- Barrier Protection: Specialty films can be engineered to provide superior resistance to gasses, moisture, and chemicals, making them ideal for food packaging and medical applications.
- Adaptability: Converter grade films are designed to serve secondary processes like printing, laminating, and coating, which are essential for creating customized packaging solutions.
- Regulatory Compliance: These films are often produced to meet stringent industry standards and certifications necessary for medical and food-grade applications.
The utilization of FF&S technology combined with the production of specialized films ensures that Dallas Plastics can meet diverse and demanding industry standards effectively. By leveraging these advanced production techniques, the company not only enhances its operational efficiencies but also ensures that the final products are of the highest quality, tailored to meet the needs of their respective industries.
Technological Advancements and Industry Trends
The world of polymer production is dynamic, continuously evolving with technological advancements and shifting industry trends. These developments not only enhance the efficiency of production processes but also contribute significantly to the sustainability and quality of the final products. By staying abreast of these trends, manufacturers can maintain a competitive edge in the market.
Recent Innovations in Polymer Production Techniques
The forefront of innovation in polymer production showcases an array of sophisticated techniques that leverage automation and advanced materials sciences. One of the notable advancements includes the use of nanotechnology to manipulate materials at the molecular level. This approach has enabled the creation of polymers with superior strength, flexibility, and resistance to chemicals.
Another promising development is the integration of IoT (Internet of Things) in manufacturing lines. Sensors and smart systems allow for real-time monitoring and adjustments during the polymerization process. This technology ensures consistency in the quality of plastic films and reduces waste by pinpointing and correcting production anomalies immediately.
Moreover, the adoption of bio-based polymers is gaining traction as industries push for sustainable and eco-friendly production methods. Derived from natural resources, these polymers not only help reduce dependency on fossil fuels but also offer enhanced biodegradability, which is crucial as global environmental regulations tighten.
Request a Quote
Analyzing Trends Impacting High-Quality Plastic Film Production
The demand for high-quality plastic films is influenced by several key trends within various industries. For instance, in the medical field, there is an increasing requirement for more sophisticated drug delivery systems, which rely on advanced polymer films. Similarly, in the food industry, the shift towards extended shelf life and improved food safety standards are driving innovations in barrier films that protect products from moisture, oxygen, and pathogens.
Another significant trend is the consumer and regulatory push towards sustainable packaging solutions. There is a growing preference for materials that are recyclable or derived from renewable resources, challenging polymer producers to innovate while adhering to environmental standards.
These technological advances and industry trends are essential in shaping the future of polymer production. They not only enhance the functionality and quality of plastic films but also address critical environmental concerns, thereby redefining the standards of excellence in the polymer production domain.
Positioning as an Industry Leader
Dallas Plastics has consistently cemented its reputation as a leader in the polymer production industry by not only meeting but often exceeding the stringent standards expected within this technical field. This commitment is showcased through their relentless pursuit of technological advancements and their firm adherence to quality in every aspect of production.
Commitment to Quality and Technological Expertise
At the core of Dallas Plastics’ operations is a deep-rooted commitment to producing high-quality plastic films, a standard that is unwavering regardless of the complexity of customer requirements.
The company utilizes state-of-the-art extrusion and blowing techniques, ensuring that every product meets precise specifications for thickness, durability, and clarity. These manufacturing capabilities are supported by advanced quality control systems that monitor consistency and quality at every stage of production.
Meeting Diverse Industry Needs
Dallas Plastics is not only a pioneer in the field but also highly adaptable to the evolving needs of various industries. Whether it’s developing medical packaging films that meet the rigorous sterilization and barrier standards of the healthcare industry or crafting specialized industrial packaging solutions designed for durability and sustainability, their products stand out in the market.
By providing flexible FF&S technology and specialty plastic films, Dallas Plastics demonstrates its capability to innovate and deliver tailored solutions that directly respond to the unique challenges faced by its clients.
Request a Quote
Final Thoughts on Mastering Polymer Production
Understanding the intricacies of polymer production processes and reactions is crucial for anyone involved in the industries of medical, food & beverage, and industrial sectors. Dallas Plastics is equipped to provide high-quality solutions tailored to your requirements.
This comprehensive guide has demonstrated how production processes directly impact the final product’s quality and functionality, reinforcing the criticality of meticulous process controls in polymer manufacturing.
At Dallas Plastics, we pride ourselves on our rigorous adherence to cGMP guidelines and our commitment to delivering top-tier, certified plastic films through state-of-the-art technology.
Our expertise in extrusion and blowing techniques, coupled with our specialized services in FF&S technology and converter grade sheeting, positions us to meet your precise needs. Let’s collaborate to enhance the quality and performance of your products.
Contact Dallas Plastics today to learn how our blown film products can support your business’s specific needs and help you stay ahead in a competitive market.