In today’s fast-paced industrial landscape, ensuring safety, enhancing efficiency, and fostering sustainability have become critical priorities. Drum liners emerge as indispensable components, fulfilling these needs across diverse sectors such as chemicals, pharmaceuticals, and food and beverages.
These liners act as a safeguard, protecting products from contamination, ensuring adherence to safety protocols, and maintaining compliance with stringent industry regulations. This guide delves into the multifaceted benefits of drum liners, the variations available, their extensive applications across industries, and provides practical advice for selecting the most suitable liners tailored to specific industrial requirements.
The Evolution and Historical Context of Drum Liners
Initially envisioned as simple barriers for contamination control, drum liners have evolved exponentially. Spurred by growing industrial complexities, they now incorporate advanced technologies and materials, offering capabilities like anti-static properties and resistance to extreme temperatures.
This transformation aligns with the industry’s broader pivot towards sustainability, efficiency, and robust operations management. Drum liners today represent not just a tool but an integral part of a cleaner, more efficient manufacturing ecosystem.
Industrial Imperatives and Drum Liners
In a climate characterized by rigorous regulatory mandates and heightened consumer expectations, industries increasingly recognize the vital role drum liners play in upholding product integrity. With unparalleled protective qualities, drum liners mitigate the risk of cross-contamination, support logistical efficiency, and align operations with sustainable development goals (SDGs), thus redefining the landscape of responsible manufacturing and stewardship.
Thorough Examination of Drum Liner Types
Understanding the breadth of drum liner types and their material compositions is crucial for optimizing their utility across varied industrial applications.
Material Innovations and Specializations
Drum liners can be made with a variety of plastic blown film materials, including polyethylene, polypropylene, and specialty polymer blends, to suit diverse industrial needs and environmental conditions.
- Low-Density Polyethylene (LDPE): Revered for flexibility and cold resistance, LDPE is a cost-effective solution for general-purpose applications, with the added benefit of UV resistance suited for outdoor storage.
- High-Density Polyethylene (HDPE): Known for its unparalleled strength and rigidity, HDPE is indispensable for the safe handling of heavy or dense materials, promising robust resistance against abrasions and environmental stressors.
- Linear Low-Density Polyethylene(LLDPE): Offers higher tensile strength than LDPE. Great for applications where increased stretch and flexibility are needed. Provides enhanced durability for heavy-duty uses.
- Metallocene Polyethylene (mPE):High-performance resin offering improved clarity, strength, and sealing.Used for specialized applications where performance needs are higher than what standard polyethylene can provide
- Foil Liners: Offering exceptional protection against elements like moisture, oxygen, and light, foil liners are essential for maintaining the stability and longevity of sensitive or perishable products, ensuring optimal preservation standards.
- Polypropylene (PP): Esteemed for its resilience against high temperatures, PP liners are pivotal in environments demanding stringent sterilization and hygiene protocols, particularly benefiting the food and pharmaceutical sectors.
- Nylon Liners: Renowned for their superior tensile strength and impact resistance, nylon liners offer robust protection against physical stressors, making them ideal for applications with high-volume throughput or frequent handling requirements.
Style Variations Enhance Utility
Selecting an appropriate liner style that complements drum design and specific needs is crucial for maximizing operational efficiency and safety:
- Anti-Static Liners: Engineered for environments susceptible to flammable hazards, these liners neutralize static electricity, enhancing safety by minimizing ignition risks. Their integration is pivotal in refining workplace safety and mitigating occupational hazards.
- High-Temperature Liners: Constructed from materials such as Teflon or high-grade polyethylene designed to withstand extreme temperatures. These are critical in industrial processes involving high-temperature materials or conditions, ensuring that the liner maintains its integrity without melting or degrading.
- Flat Bottom Liners: Streamline insertion and removal processes, making them ideal for operations requiring frequent liner changes and facilitating agile workflow transitions. Their design minimizes setup time while bolstering productivity.
- Pleated Liners: With the ability to expand to accommodate varying volume levels, pleated liners optimize storage capacity without compromising containment integrity. They are crucial in variable production cycles where flexibility and adaptability are prized.
- Round Bottom Liners: Provide a secure and contoured fit, ensuring complete containment by preventing material contact with drum surfaces and significantly mitigating contamination risks. Their reliability in maintaining content purity underpins process stability.
- Straight-Sided Liners: Offer reinforced strength and structural integrity for tall drums or those under heavy load, ensuring maintenance of form even under pressure. Such durability is essential in ensuring operational continuity without disruptions.
- Form-Fit Liners: Tailored specifically to the shape and size of the drum, these liners eliminate folds and creases that could trap material. They are instrumental in minimizing waste and ensuring efficient discharge, particularly in high-precision industries.
- Thickness Variations: Liners are available in various thicknesses to cater to different load requirements and durability needs. Heavy-duty liners for rigorous applications and lightweight options for everyday use ensure tailored solutions across diverse operational contexts
- Color-Coding: Liners can be produced in different colors for easy identification and sorting, aiding in inventory management and cross-contamination prevention in facilities dealing with multiple substances.
Multifaceted Benefits of Drum Liners
The strategic integration of drum liners within industrial operations delivers a suite of benefits, enhancing performance across several dimensions.
Advanced Contamination Prevention
As reliable barriers, drum liners safeguard product quality against potential contaminants, thus upholding stringent hygiene and compliance standards essential to protect consumer well-being and brand reputation.
Cost Reduction and Labor Optimization
By minimizing the need for extensive cleaning and maintenance, drum liners significantly extend the life cycle of drums, subsequently reducing operational costs and freeing human resources for more value-driven pursuits. This optimization leads to increased throughput and streamlined processes.
Enhanced Environmental Sustainability
Drum liners support initiatives aimed at waste reduction by promoting drum reuse, aligning with broader corporate sustainability objectives. Moreover, their application contributes meaningfully to minimizing landfill contributions, aiding in the ecological conservation effort.
Resistance to Extreme Conditions
Designed with durable materials, drum liners withstand severe environmental and chemical factors, thereby mitigating risks associated with variable storage conditions. Their robustness ensures that product quality is preserved even in harshest settings.
Integrated Transport Security
Bolstered durability prevents punctures or leaks, thereby securing product integrity across intricate logistics networks. This protection is critical for safeguarding international shipments, which may encounter diverse environmental challenges.
Operational Efficiency Enhancement
By streamlining standard operating protocols, drum liners facilitate smoother transitions between production cycles. Their inclusion in logistical workflows enhances responsiveness, reducing bottlenecks and elevating productivity metrics.
Diverse Applications Across Industries
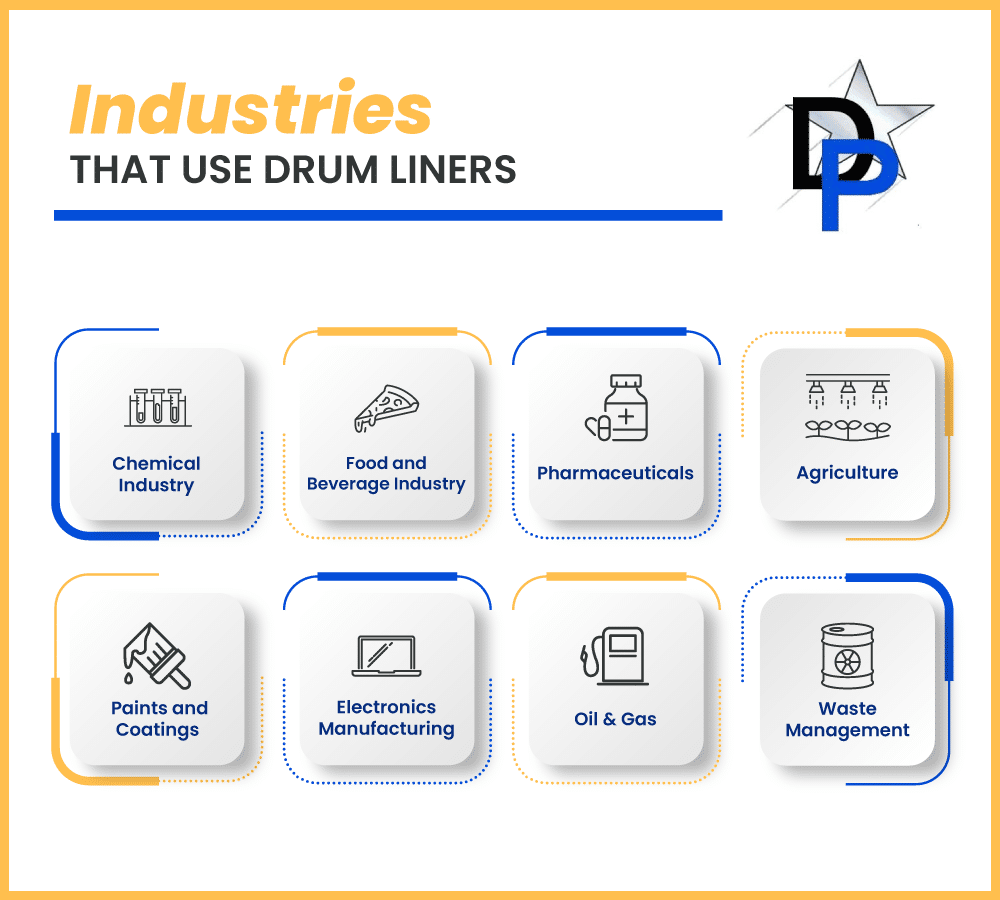
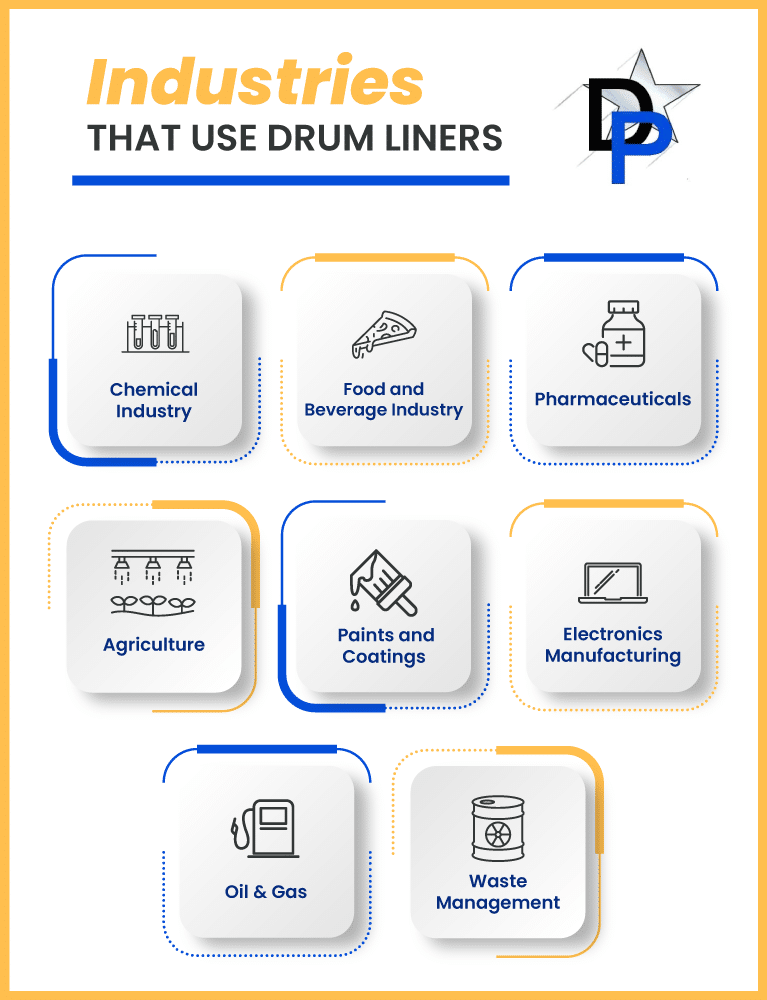
The versatility of drum liners ensures their relevance across numerous industries characterized by unique requirements and logistical challenges:
- Chemical Industry: Drum liners contain and control reactive materials, preventing adverse chemical interactions and ensuring safe storage and transportation practices. Their application is critical for maintaining stability and compliance within environments where reactive agents are prevalent.
- Food and Beverage Industry: Maintaining rigorous hygiene and preventing microbial contamination is crucial across food supply chains. Drum liners fulfill this role by ensuring compliance with stringent food safety regulations, thus safeguarding consumer health and brand reputation.
- Pharmaceuticals: Within the sensitive pharmaceutical landscape, drum liners protect against cross-contamination, securing product efficacy and aligning with the regulatory frameworks governing product purity and safety.
- Agriculture: By safeguarding vital agricultural inputs such as fertilizers and pesticides during transport and storage, drum liners ensure potency and protection against volatilization or degradation caused by environmental factors.
- Paints and Coatings: Drum liners prevent residue buildup, streamline cleaning processes, and reduce waste, thereby optimizing manufacturing workflows and enhancing product turnaround times.
- Electronics Manufacturing: Anti-static or conductive liners are crucial to prevent static discharge, which can damage sensitive electronic components.
- Oil and Gas: These companies need to store and transport various materials, including drilling fluids and hazardous waste, safely and cleanly.
- Waste Management: Drum liners can be particularly useful for hazardous waste containment and disposal, ensuring compliance with environmental regulations.
Key Considerations for Selecting Drum Liner Materials
Making informed choices regarding liner materials is paramount to realizing optimal benefits while circumventing potential challenges:
- Barrier Properties: It is vital to decide whether an impermeable or breathable liner is necessary, depending on the product’s moisture sensitivity and environmental conditions. The correct choice ensures robust separation and contamination prevention.
- Chemical Compatibility: Ensuring liners remain inert when in contact with contents prevents reactions, which is crucial in industries handling reactive or volatile substances.
- Temperature Stability: Assessing a liner’s resilience to temperature extremes is essential to guarantee consistent containment, protecting both the liner and its contents across operational and ambient variance.
- Precise Fit and Size Adherence: Ensuring liners meet exact drum specifications guards against material waste and negates the need for downstream corrective adjustments.
- Comprehensive Evaluation of Environmental Considerations: Incorporate assessments of temperature variations and shipment-induced stresses when determining suitable liners, fortifying operational resilience.
Strategies for Material Selection Success
To select the perfect drum liner there are a few considerations:
- Comprehensive Research into Material Properties: Focus on tensile strength, tear resistance, and flexibility to ensure adaptability and resilience under varied operational conditions.
- Consultation with Industry Experts: Engage with suppliers to access tailored solutions, ensuring liner criteria align with specific industrial requirements while leveraging professional expertise.
- Implementation of Pilot Tests: Pilot trials are crucial for assessing liner performance within real-world settings, confirming expectations meet outcomes and refining choices as necessary.
The Influence of Expert Insights
Incorporating expert opinions is instrumental in enhancing decision-making, where consulting engineers and material scientists ensures alignment with operational goals, mitigates risks, and extends longevity for both liners and drums.
Drum Liners’ Environmental and Sustainability Contribution
Drum liners are playing a vital role in advancing sustainable practices and effective resource management for many companies. These liners significantly contribute to driving sustainable reuse by extending the lifespan of drums, thereby limiting waste generation and promoting efficient resource utilization throughout supply chains.
In addition, ongoing efforts to develop recyclable drum liners are supporting forward-looking recycling initiatives. These recyclable options integrate lifecycle considerations into packaging choices, laying the groundwork for robust circular economy models.
Furthermore, the focus on biodegradable research within the drum liner industry is yielding eco-friendly alternatives that address environmental concerns while aligning with emerging legislative mandates for sustainability. This multifaceted approach highlights drum liners’ ability to bolster environmental stewardship and compliance in a variety of industrial settings.
Sustainability Trends Across Industries
In recent years, the incorporation of drum liners within circular economy strategies has become increasingly pivotal in reducing waste and enhancing resource recycling efforts. This transformative approach not only minimizes environmental impact but also underscores a commitment to ecological sustainability.
Companies are actively leveraging drum liners as part of their holistic waste management systems, contributing to a more sustainable and resource-efficient industrial ecosystem.
Simultaneously, there is a significant focus on the development of biodegradable drum liners. Extensive research and innovation in this area highlight the ongoing prioritization of balancing ecological responsibilities with the need for high-performance materials. By investing in biodegradable solutions, industries are striving to meet their environmental goals without compromising on product efficacy and reliability.
This dual focus on the circular economy and biodegradable innovation represents a compelling shift towards more sustainable practices in the blown film industry and beyond.
Supply Chain Optimization
The strategic implementation of drum liners fosters efficiency by encouraging economies of scale, thereby reducing carbon footprints across transportation frameworks. This alignment with environmental targets offers dual benefits: cutting logistics costs while adhering to evolving regulatory landscapes.
Emerging Innovations Leading Drum Liner Evolution
Drum liners have undergone significant evolution driven by advancements in materials science, manufacturing processes, and sustainability considerations. Initially, drum liners were rudimentary, often made from basic polyethylene films offering limited protection and durability.
These early iterations served fundamental purposes but were prone to punctures, tears, and permeability to various substances, thus compromising the integrity of the stored products. As the industrial landscape evolved, the demand for more robust and reliable packaging solutions saw a concerted effort toward innovation in drum liner manufacturing.
The introduction of multi-layer co-extrusion technology marked a pivotal advancement in the production of drum liners. Blown film manufacturers began utilizing this technique to create liners with composite structures, where each layer could be engineered to provide distinct properties such as enhanced strength, chemical resistance, and barrier protection against moisture and gasses. Materials like high-density polyethylene (HDPE), linear low-density polyethylene (LLDPE), and ethylene vinyl alcohol (EVOH) have been incorporated in various combinations to address specific needs.
With growing environmental concerns, manufacturers are increasingly focusing on creating eco-friendly solutions. This has led to the development of biodegradable and recyclable materials, as well as the incorporation of post-consumer recycled (PCR) content in drum liners.
Advances in polymer chemistry have enabled the design of biodegradable liners that decompose under specific conditions, reducing their environmental footprint.
Additionally, improvements in processing technologies have allowed for the efficient manufacture of liners from recycled materials without compromising on quality and performance.
Automation and artificial intelligence (AI) are also transforming the drum liner manufacturing process. Modern blown film manufacturing lines are now equipped with sophisticated automated systems that ensure precise control over film thickness, composition, and quality. Real-time monitoring and AI-driven analytics help in detecting defects early, optimizing production parameters, and minimizing waste.
As industries advance, the expectations from drum liners are also expanding. Consequently, the research and development efforts in this domain remain robust, promising further refinements and groundbreaking solutions that will enhance the safety, efficiency, and environmental responsibility of drum liner products.
Upholding Industry Standards and Compliance for Drum Liners
Adherence to industry regulations when utilizing drum liners is vital for maintaining quality assurance and safety compliance.
Navigating Regulatory Frameworks:
Stay vigilant and informed on evolving standards, ensuring liner adherence to contemporary mandates. Purchase drum liners from companies with ISO certifications and who follow Current Good Manufacturing Practices, also known as cGMP.
Additional Compliance Considerations and Procedures
Beyond selecting the appropriate liner, safeguarding compliance necessitates comprehensive documentation and an unwavering adherence to universal standards such as FDA, EPA, and ISO regulations. Implementation includes dynamic data structuring and maintaining recall readiness.
Training and Best Practices Initiatives
Ongoing training programs enhance liner usage efficacy and regulatory understanding among teams. Introducing standard operating procedures (SOPs) alongside interactive workshops fosters a well-informed workforce keenly aligned with drum handling and selection best practices. Establishing a culture of perpetual learning and adaptability ensures sustainable success and diligence throughout operational workflows.
Unlocking Drum Liner Potential for Industrial Success
Drum liners remain indispensable components within modern industrial operations, providing significant advantages from contamination mitigation to resource optimization. Appropriately selected and strategically implemented liners transform process efficiencies, fortifying product integrity while ensuring robust compliance. Engaging with domain experts and incorporating customized, innovative solutions culminates in superior efficacy paired with sustainability.
Reach out for specialized guidance on choosing the most fitting domestically made drum liners for your requirements, and lead the charge in revolutionizing packaging methodologies to exceed future industrial demands sustainably and profitably.
In offering a comprehensive encapsulation of drum liners’ significance, this article affords industry stakeholders the insights needed to leverage these components for operational excellence, ensuring alignment with future visionary trajectories.