Coextruded film packaging offers an innovative approach to reducing material costs while enhancing product durability across various applications. By combining multiple polymers into a single film, this advanced technology blends mechanical strength, barrier properties, and visual appeal. Its versatility is highly valued in industries such as food and beverage, pharmaceuticals, and industrial manufacturing.
This article delves into the fundamentals of coextruded film packaging, including its manufacturing process, key features, and diverse applications. By comparing it to other packaging options, highlighting its benefits and challenges, and discussing sustainability, you will gain a comprehensive understanding of why coextruded films are critical in modern packaging strategies.
What Is Coextruded Film Packaging?
Coextruded film packaging is a cutting-edge solution in the flexible packaging industry, created through a process known as coextrusion. This technique merges multiple streams of melted polymers into a single film, with each layer contributing unique functions such as durability, clarity, or barrier protection. These layers form a cohesive structure, ensuring high-performance packaging that meets diverse needs.
Unlike traditional single-layer films, which can struggle with more complex packaging requirements, coextruded films combine specialized attributes in their multilayer design. One layer may offer barrier strength to preserve freshness, another delivers mechanical resilience, and a third focuses on heat sealing. The outcome is a film that is both versatile and customized for the product’s protection standards.
Additionally, merging layers in one seamless coextrusion process reduces or removes the need for time-consuming lamination or adhesives. This often leads to streamlined production, more precise control over material composition, and potential cost savings—without sacrificing quality.
How Coextruded Films Differ from Single-Layer and Laminated Films
Coextruded films stand out by consolidating multiple polymer layers in a single production step, distinguishing them from single-layer and laminated alternatives:
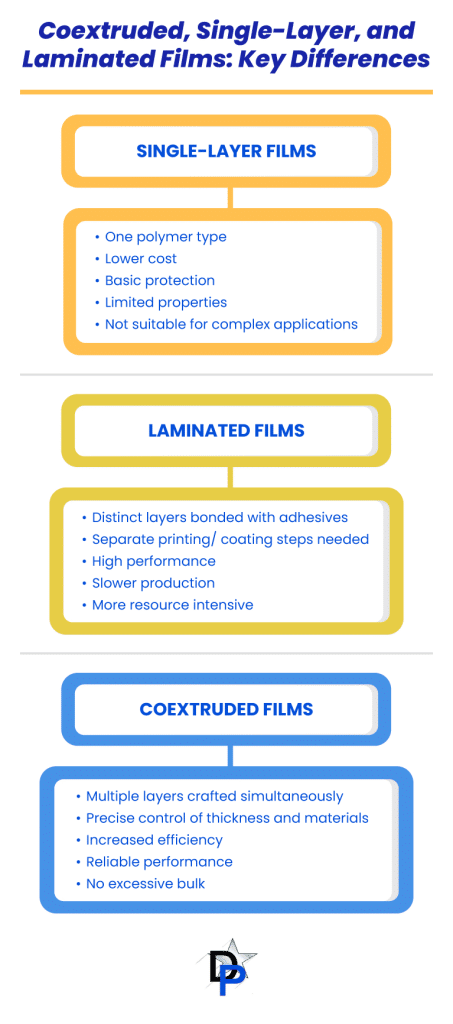
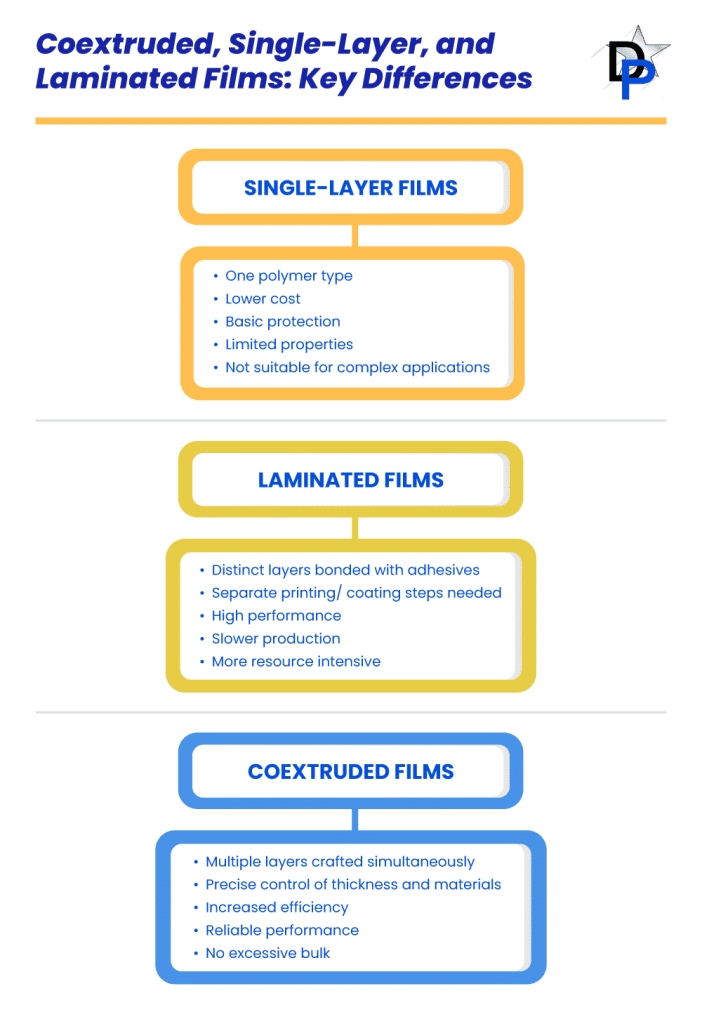
- Single-Layer Films: These rely on a single polymer type to provide all protective functions. While inexpensive and sufficient for simple applications, their limited properties make them unsuitable for products needing advanced protection or extended shelf life.
- Laminated Films: Laminates bond distinct layers with adhesives, often requiring separate steps for printing or coating. Though they can deliver high performance, the additional processing makes production slower and more resource-intensive.
By contrast, coextruded films craft layers simultaneously, providing precise control of thickness and material composition. This single-step approach enhances efficiency, ensures reliable performance, and avoids excessive bulk.
Key Features and Properties of Coextruded Films
Coextruded films offer numerous features that fulfill modern packaging goals:
- Multilayer Structure: Each layer targets specific properties, whether clarity, mechanical protection, or barrier performance.
- Superior Barrier Properties: With tailored resin blends, they effectively guard against moisture, oxygen, and UV light.
- High Customization Potential: Optimized thicknesses, additives, and layering options meet unique packaging demands.
- Durability: Strong enough to resist punctures, tears, and stretching.
- Sustainability: Thinner films reduce material usage and support eco-friendly resin choices, where possible.
These features provide comprehensive protection and can be readily adapted to unique industry or product challenges.
Multilayer Composition for Enhanced Functionality
At the core of coextruded film packaging is its multilayer form, where each polymer layer serves a distinct function. One layer may supply barrier defense, another layer imparts mechanical strength, and a third enhances sealing performance.
Superior Barrier Protection
By incorporating specialized resins, coextruded films successfully protect products from oxygen, moisture, and UV exposure. This is crucial for perishable goods or sensitive pharmaceuticals that depend on freshness and stability throughout the supply chain.
High Customization Potential
Coextrusion techniques offer flexible design options. Manufacturers can tailor polymer blends, thickness, and surface treatments to achieve exactly the level of clarity, barrier strength, or sealing they need, ensuring the film is optimized for its intended application.
Excellent Strength and Durability
The synergy of multiple polymers confers excellent tear and puncture resistance, enabling secure transport and storage even in challenging conditions. Robust coextruded films are particularly appealing for items that travel through complex supply chains or need rigorous protection.
Advanced Sustainability Features
With constant attention on eco-friendly packaging, coextruded films respond by reducing overall plastic usage. Thinner but stronger films lower material consumption, while advanced formulations can include renewable or recycled resins to lessen environmental impact.
How Coextruded Films Are Made
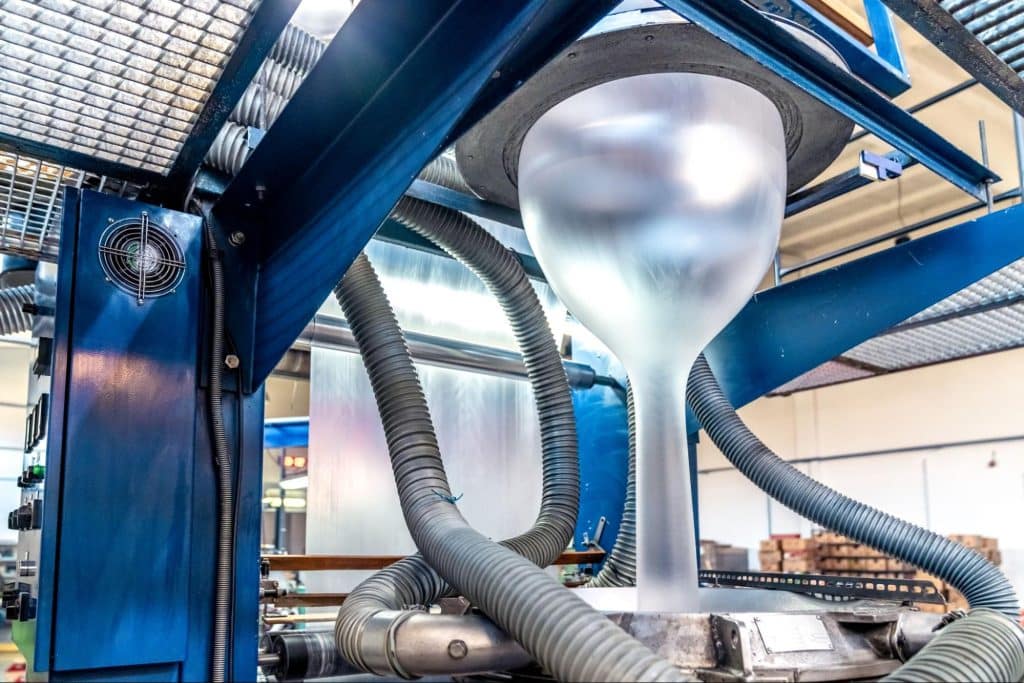
Producing coextruded films combines materials science with precision engineering:
Resin Selection and Preparation
Packaging designers select resins based on targeted properties (e.g., toughness, sealability, or clarity). Common variants include polyethylene (PE). Each resin is dried and blended with additives like antistatic agents as needed.
Melting and Extrusion
Each polymer blend is melted in its own extruder. The molten polymers converge into a feedblock or die head that forms the distinct layers. By controlling temperature and flow rates, manufacturers ensure each layer meets the required material composition.
Layer Formation and Distribution
Various molten polymers merge into a single film, distributing each resin layer with precise thickness. This approach allows for balancing attributes like mechanical strength and transparency within one cohesive product.
Shaping and Cooling
After layering, the molten film takes shape via processes such as the blown film process. The film is cooled and wound into rolls, preserving the properties achieved during extrusion.
Winding and Packaging
Completed rolls are inspected for consistent thickness, seal integrity, and appearance. Films that meet quality requirements are shipped for labeling, printing, or direct use in packaging lines.
Applications of Coextruded Films Across Industries
Coextruded films are prevalent in a variety of industries, where their performance and adaptability drive product innovation:
Food and Beverage: Preserving Freshness and Quality
The food and beverage industry depends on high-barrier solutions to minimize spoilage and maintain taste. Coextruded films protect items like meat, cheese, and produce, extending shelf life and preventing flavor degradation.
Medical and Pharmaceutical: Ensuring Sterility and Safety
In medical and pharmaceutical sectors, coextruded films deliver an essential sterile barrier for instruments, devices, and pharmaceuticals. Their controlled composition helps maintain drug efficacy and product integrity, supporting patient safety.
Industrial Packaging: Durability for Demanding Conditions
Industrial goods often require packaging that can withstand harsh conditions and extended transport times. Coextruded films offer durability and tear resistance, making them ideal for components, bulk materials, and frequently moved goods.
Specialty Applications: Custom Solutions for Unique Needs
Coextrusion enables the incorporation of features like high clarity, unique color, or specialized sealing, opening the door for customized packaging solutions. From high-end retail displays to performance films in niche technical fields, the possibilities are expansive.
In addition, industries often turn to coextruded films for items like bags on rolls or drum liners where reliable protection and strength are crucial for secure transport and handling.
Benefits of Coextruded Film Packaging
Embracing coextruded film solutions provides several key benefits:
- Outstanding Performance: Multiple layers yield reliable strength and product integrity.
- Cost Efficiency: A single manufacturing process can lower production and material expenses.
- Flexible Customization: Layer thickness or resin composition can be fine-tuned.
- Improved Sealing Capabilities: Consistent, high-integrity seals reduce leakage or contamination.
- Lightweight and Space-Saving: Thinner films reduce overall packaging bulk.
- Sustainability: Efficient use of materials and support for recycled or renewable resins.
Comparing Coextruded Film Packaging to Other Packaging Types
When weighed against single-layer, laminated, and rigid packaging, coextruded films frequently offer a more balanced blend of performance, cost, and sustainability:
Single-Layer Films: Simplistic but Limited
Single-layer media can be suitable for basic needs. However, they typically fall short in barrier protection or durability for sensitive or perishable products.
Laminated Films: Effective but Resource-Intensive
Laminated films provide enhanced functionality by bonding together multiple pre-formed layers. This process, however, involves adhesives and extra steps, driving up costs and production times.
Rigid Packaging: Durable but Bulky
Rigid packaging solutions (like bottles or clamshells) can endure tough handling but require more raw material and increased shipping space, contributing to higher waste and transport costs.
Coextruded films offer a lighter, space-saving alternative while maintaining durability and product integrity.
Potential Drawbacks and Challenges of Coextruded Film Packaging
Though coextruded films hold numerous advantages, businesses should also note potential downsides:
- Recycling Complexity: Mixing polymers can complicate recycling efforts if the layers are incompatible.
- Specialized Equipment: Coextrusion demands advanced machinery and skill, resulting in higher capital investment.
- Customization Costs: Developing specific polymer blends for small-scale projects may be cost-prohibitive.
- Layer Property Trade-offs: Boosting clarity in one layer may curtail barrier performance in another, necessitating thorough design and testing.
Sustainability in Coextruded Film Packaging
Coextruded films address sustainability in multiple ways:
Material Efficiency and Reduction
Their ability to perform effectively in thinner gauges reduces total plastic usage so that products remain protected without excess material.
Integration of Recycled and Renewable Materials
Manufacturers increasingly explore recycled resins or renewable resins to craft environmentally conscious films. Using green materials can help meet regulatory or market demands for eco-friendly packaging.
Extended Product Shelf Life
Superior barrier properties extend product longevity, diminishing food waste and the associated environmental impact of discarded items.
Developments in Recyclable Alternatives
As manufacturing technologies advance, more easily recyclable coextruded solutions become feasible, supporting global sustainability initiatives.
Why Coextruded Films Are Essential for Modern Packaging Solutions
Packaging continues to evolve, driven by efficiency, consumer expectations, and sustainability targets. Coextruded films seamlessly align with these demands:
- Significant Versatility and Customization: Layer-by-layer control ensures a perfect match for packaging goals.
- Outstanding Product Protection: Multi-barrier performance maintains freshness, safety, and durability.
- Cost-Efficiency in Production and Application: Producing multiple layers in one pass reduces resources and boosts efficiency.
- Commitment to Sustainability: Thinner, stronger films and potential for green resins balance performance and eco-responsibility.
Request a Quote
Explore the Future of Packaging with Coextruded Films
Coextruded film packaging merges multiple layers into a unified structure that addresses diverse, modern packaging challenges. From safeguarding sensitive pharmaceuticals to fresh food packaging, these multilayer films provide an ideal blend of protection, cost savings, and potential for sustainability.
As your business adapts to changing market demands, coextruded film technology can help ensure product integrity, extend shelf life, and enhance brand appeal. Contact our expert team at Dallas Plastics to explore how customized coextruded films can deliver reliable, high-performance packaging solutions that align with evolving consumer and environmental priorities.