Plastic resin production is the cornerstone of the modern manufacturing landscape, enabling the creation of a vast array of products we rely on daily. From medical devices and food packaging to automotive parts and household goods, understanding the intricacies of plastic resin production not only illuminates how these essential materials are crafted but also highlights the technological advancements and environmental considerations shaping the industry today. This comprehensive guide delves into the science behind polymerization, explores various types of plastic resins, details the production process, and examines the innovations driving sustainability in the field.
Plastic Resin Production
Plastic resin production is fundamental to the plastics industry, serving as the raw material for countless products across multiple sectors. These resins are synthetic polymers derived primarily from petrochemicals or renewable resources and are processed into final products through various molding and shaping techniques. The global reliance on plastic resin production underscores its significance in modern manufacturing and everyday life.
For industry professionals, educators, students in materials science or chemical engineering, and environmentally-conscious consumers, understanding plastic resin production is essential. It empowers stakeholders to make informed decisions about material selection, production methods, and sustainability practices, ensuring that advancements in the field align with both economic and environmental goals.
The Science of Polymerization
At the heart of plastic resin production lies polymerization—a chemical process that combines small molecules known as monomers into long-chain polymers. This transformation is critical in determining the properties and applications of the resulting polymer, leading to a diverse range of plastic resins with unique properties and applications.
Addition Polymerization
Addition polymerization, also referred to as chain-growth polymerization, involves monomers with double bonds reacting to form polymers without the production of by-products. This method is commonly used to produce polymers like polyethylene and polypropylene. The process typically requires initiators or catalysts to start the reaction, leading to high molecular weight polymers with specific characteristics suitable for various applications.
Condensation Polymerization
Condensation polymerization, or step-growth polymerization, occurs when monomers react to form polymers while releasing small molecules such as water or methanol. This method is used to produce polymers like polyesters and polyamides. The resulting polymers often have different properties compared to those made via additional polymerization, offering alternatives for specialized applications that require enhanced durability and performance.
Chemical Catalysts and Conditions
Both addition and condensation polymerization methods rely on precise conditions—including temperature, pressure, and the presence of catalysts—to control the reaction rate and polymer properties. Ziegler-Natta catalysts are essential in polyethylene production, enabling the creation of polymers with specific structures and characteristics. Proper control of these conditions ensures the production of high-quality plastic resins tailored to meet the exacting demands of various industries.
Understanding the science of polymerization allows manufacturers to tailor plastic resin production processes, resulting in materials that meet specific performance criteria and application requirements.
Types of Plastic Resins
The diversity of plastic resins is a direct consequence of the variety of monomers and polymerization methods employed. Each resin type possesses unique properties, making it suitable for specific applications across different industries.
Polyethylene (PE)
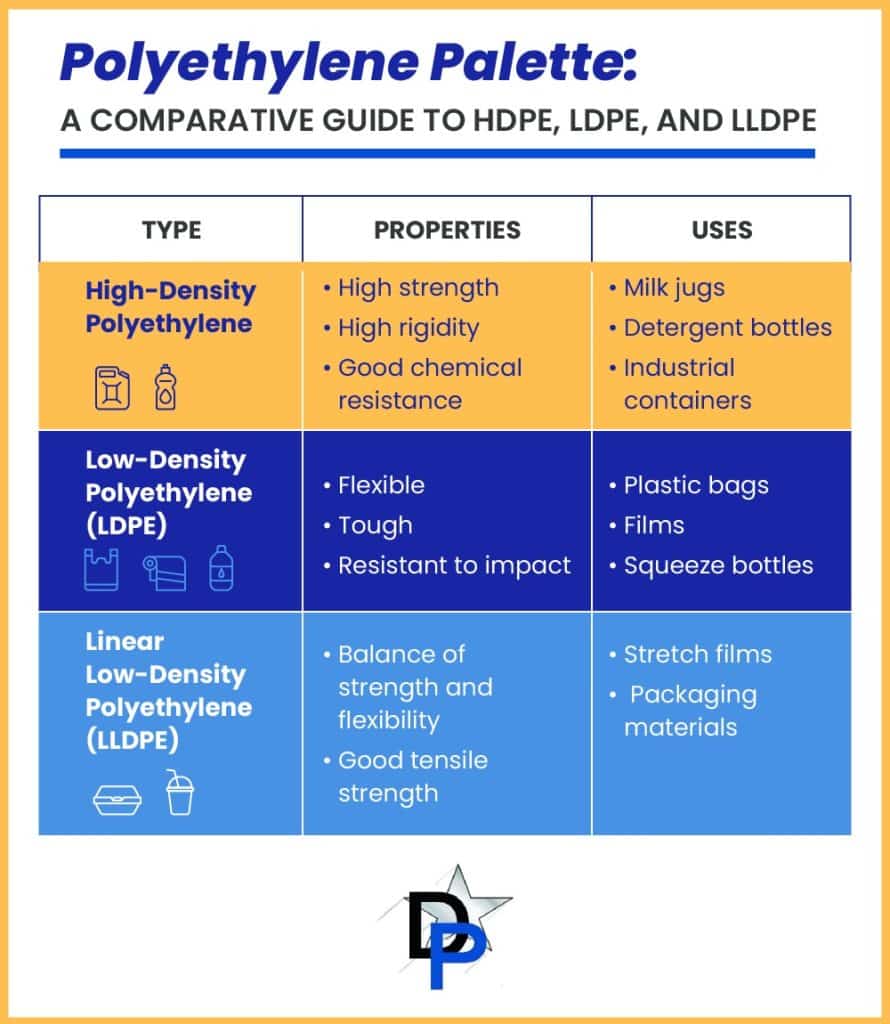
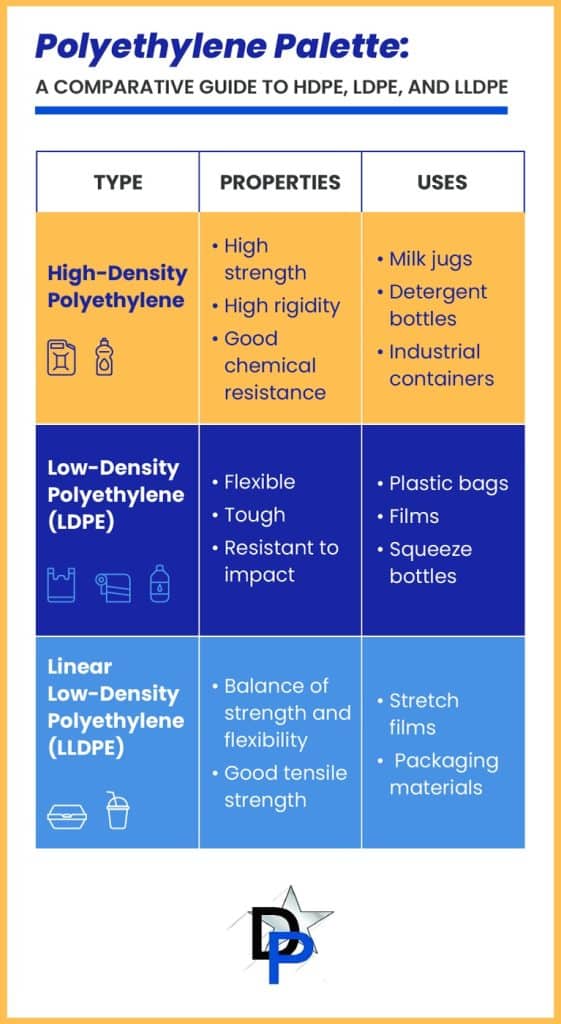
Polyethylene is the most widely used plastic resin, found in products ranging from plastic bags and films to bottles and containers. It comes in several densities:
- High-Density Polyethylene (HDPE): Known for its strength and rigidity, HDPE is used in milk jugs, detergent bottles, and industrial containers.
- Low-Density Polyethylene (LDPE): More flexible than HDPE, LDPE is often used in plastic bags, films, and squeeze bottles.
- Linear Low-Density Polyethylene (LLDPE): Offers a balance of strength and flexibility, making it suitable for stretch films and various packaging materials.
Polypropylene (PP)
Polypropylene is valued for its toughness, resistance to heat and chemicals, and versatility. It is commonly used in automotive parts, medical devices, food containers, and consumer goods. While medical-grade polypropylene can handle steam sterilization, repeated cycles may affect structural integrity.
Polyvinyl Chloride (PVC)
PVC is extensively used in construction due to its durability and resistance to environmental degradation. Applications include pipes, window frames, electrical insulation, and flooring. Its versatility also extends to medical tubing and packaging materials.
Polystyrene (PS)
Polystyrene is found in disposable cutlery, CD cases, insulation materials, and packaging applications. Its rigidity and clarity make it ideal for products that require a clear view of the contents, such as food containers and display items.
Polyethylene Terephthalate (PET)
PET is used in beverage bottles, food packaging, and fibers for textiles. Known for its strength and recyclability, PET is a cornerstone in the production of recyclable bottles and containers that are both durable and lightweight.
Engineering Plastics
Materials like Polyetheretherketone (PEEK) and polyimides offer high-performance characteristics suitable for aerospace, electronics, and advanced industrial applications. These engineering plastics are prized for their heat resistance, mechanical strength, and chemical inertness.
Specialty Resins
Specialty resins are tailored for specific applications that require unique properties. These include bioplastics like Polylactic Acid (PLA), which are biodegradable, and smart plastics that incorporate conductive elements for enhanced functionality.
Understanding the properties and applications of different plastic resins enables manufacturers and designers to select the most appropriate material for their specific needs, ensuring optimal performance and cost-effectiveness.
Step-by-Step Journey from Polymerization to Resin
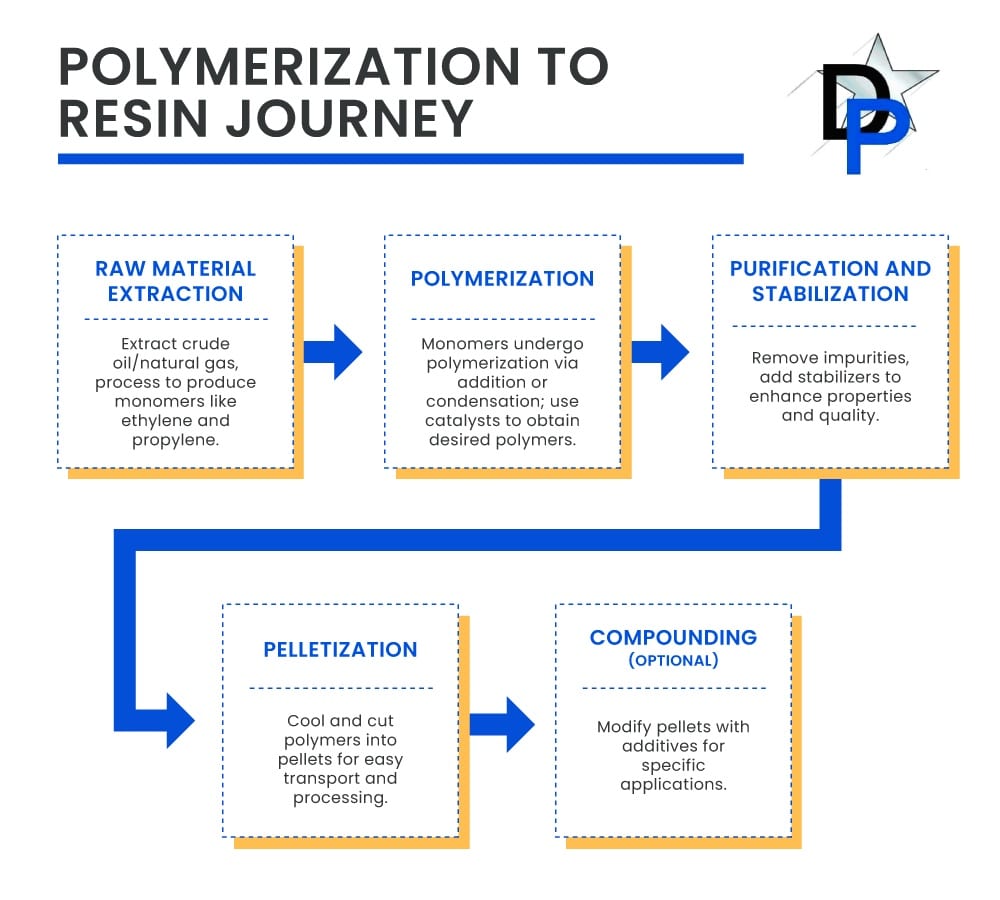
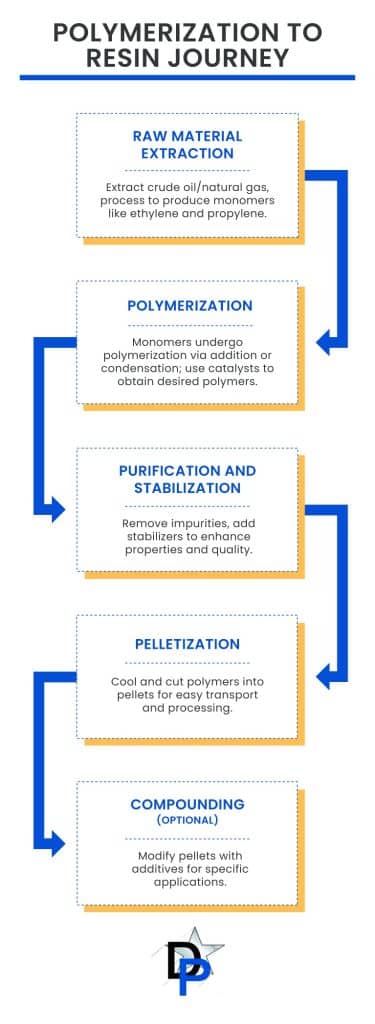
The production of plastic resin involves several critical stages, transforming raw materials into usable polymers. Understanding this journey highlights the complexity and precision required to produce high-quality plastic resins.
1. Raw Material Extraction
The process begins with the extraction of raw materials, primarily crude oil or natural gas. These hydrocarbons are processed in refineries to produce monomers like ethylene and propylene, which serve as the building blocks for various plastic resins.
2. Polymerization
The extracted monomers undergo polymerization through either addition or condensation methods. Controlled conditions and catalysts guide the reaction, resulting in polymers with desired molecular weights and structures tailored for specific applications.
3. Purification and Stabilization
After polymerization, the raw polymer may contain unreacted monomers or catalyst residues. Purification processes remove these impurities, and stabilizers are added to enhance the polymer’s properties and longevity, ensuring consistent quality and performance.
4. Pelletization
The purified polymer is cooled and cut into pellets or granules, standardized forms that are convenient for transportation and further processing. Pelletization ensures uniformity in size and shape, facilitating ease of handling and integration into various manufacturing processes.
5. Compounding
In this optional stage, additives such as colorants, fillers, or reinforcement fibers are mixed with the polymer pellets to modify their properties for specific applications. Compounding allows for the customization of plastic resins, enabling the creation of materials that meet precise technical requirements.
Understanding this journey emphasizes the complexity and precision involved in producing high-quality plastic resins, which are essential to various industries and applications.
Processing Techniques of Plastic Resins
Once the plastic resin is produced, it undergoes processing methods that transform it into finished products. Various techniques are employed based on the desired shape, properties, and application, each offering unique benefits and capabilities.
Extrusion
Extrusion involves melting plastic pellets and forcing the molten plastic through a shaped die to create continuous forms like pipes, sheets, and films. This highly efficient process is suitable for high-volume production and is widely used in the manufacturing of plastic tubing, vinyl windows, and packaging films.
Injection Molding
Injection molding is used to produce complex, precise parts by injecting molten plastic into a mold cavity under high pressure. This technique is ideal for high-volume production and is extensively used in the automotive, medical, and consumer goods industries to create components with intricate details and tight tolerances.
Blow Molding
Blow molding creates hollow plastic products like bottles and containers by extruding a tube of molten plastic (parison) and inflating it within a mold to take its shape. This method is essential in the production of beverage bottles, storage tanks, and other hollow objects, offering consistency and durability. Learn more about the blown film extrusion manufacturing process.
Thermoforming
Thermoforming heats plastic sheets until pliable and then forms them over molds to create products like packaging trays, disposable cutlery, and containers. This versatile process allows for the rapid production of custom shapes and sizes, making it a popular choice for the food and packaging industries.
Understanding these processing techniques allows manufacturers to select the appropriate methods to achieve desired product characteristics efficiently, ensuring that plastic resins are transformed into high-quality, functional products that meet industry standards and consumer expectations.
Request a Quote
Applications of Plastic Resins
Plastic resins are integral to numerous industries, each requiring materials with specific properties to fulfill their unique needs. The versatility and adaptability of plastic resin production enable the creation of products that are essential to everyday life and advanced technological applications.
Medical Sector
In the medical field, plastic resins are used to produce sterile packaging, disposables, and equipment components. Materials like polypropylene and polyethylene are favored for their biocompatibility and inertness, ensuring that medical devices and packaging do not contaminate or react with sensitive products. Innovations in plastic resin production have led to the development of high-strength, transparent materials that enhance the safety and efficacy of medical products.
Food and Beverage Industry
Food-grade plastic resins ensure safety and compliance with regulatory standards in the food and beverage industry. Applications include packaging films, containers, and liners that protect food products while extending shelf life. The production of plastic resin-based packaging must adhere to strict guidelines to prevent contamination and maintain the integrity of the food, making plastic resin production critical in this sector.
Industrial Applications
In industrial settings, durable and resistant plastic resins are essential for manufacturing components, machinery parts, and protective elements. High-density materials offer the necessary strength and longevity required in harsh environments, while specialized resins provide resistance to chemicals, heat, and mechanical stress. Industries such as automotive, aerospace, and manufacturing rely heavily on plastic resins for their flexibility and performance.
Specialty Applications
Customized resins and advanced processing techniques enable the creation of specialized products that meet specific industry demands:
- Form, Fill, and Seal (FF&S) Technologies: Automated packaging systems that use plastic films for efficient product sealing, enhancing production speed and consistency.
- Converter Grade Sheeting: Used for further processing into bags, pouches, or other packaging formats, converter-grade sheeting offers high-quality materials that meet stringent industry standards.
- High-Strength Films and Centerfold Sheeting: Designed for applications requiring exceptional durability and strength, these specialized resins support a wide range of industrial and consumer products.
The versatility of plastic resins allows them to meet the diverse demands of various industries, emphasizing their importance in modern manufacturing and everyday applications.
Environmental Considerations in Plastic Resin Production
While plastic resin production offers substantial benefits in terms of versatility and functionality, it also presents significant environmental challenges. Addressing these issues is crucial for the sustainable growth of the plastics industry and the preservation of our planet.
Ecological Footprint
Plastic resin production consumes significant amounts of fossil fuels and releases greenhouse gases, contributing to environmental degradation and climate change. The American Chemistry Council reported a reduction in GHG emissions per kilogram of resin produced, with the industry shifting towards lower carbon fuels and improved production efficiencies. According to Environment + Energy Leader, 58% of U.S. plastic-related emissions arise from virgin resin production. Mitigating the ecological footprint of plastic resin production requires a concerted effort to adopt more sustainable practices and reduce reliance on non-renewable resources.
Waste Management Challenges
Plastic waste accumulation in landfills and oceans poses severe threats to wildlife and ecosystems. Microplastics resulting from the degradation of larger plastic items can enter the food chain, impacting both marine life and human health. The limited recyclability of certain plastic resins exacerbates waste management challenges. OECD reports that only 9% of plastic waste is effectively recycled, while 77% ends up in landfills and uncontrolled dumpsites. Innovative solutions are necessary to manage and reduce plastic waste effectively.
Sustainable Practices
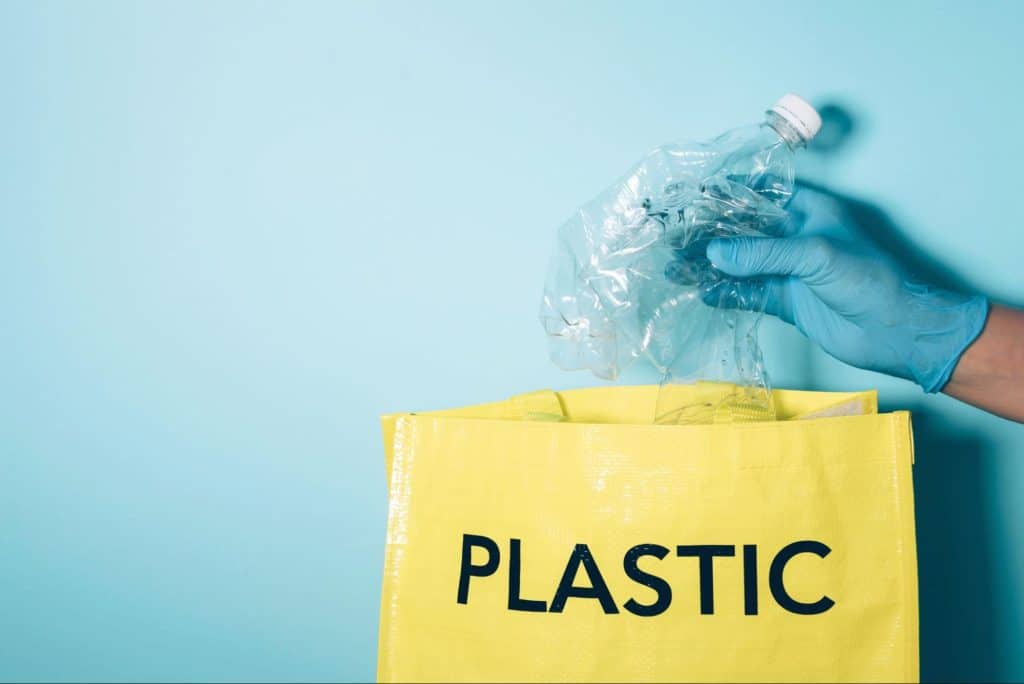
To address environmental concerns, the plastics industry is increasingly adopting sustainable practices:
- Recycling Initiatives: Incorporating post-consumer recycled materials in plastic resin production reduces the demand for virgin plastics and lowers environmental impact.
- Bioplastics Development: Creating plastics from renewable resources that are biodegradable or compostable offers eco-friendly alternatives to traditional plastic resins. As reported by PMC, the bioplastics market is projected to grow from USD 9.2 billion in 2020 to USD 20 billion by 2026.
- Energy Efficiency: Improving manufacturing processes to reduce energy consumption and emissions contributes to more sustainable plastic resin production.
Industry Innovations
Companies are investing in technologies that support a circular economy and reduce environmental impact. Innovations like chemical recycling break down plastics into their monomers for repolymerization, and the development of materials with enhanced recyclability are paving the way for more sustainable plastic resin production.
Understanding and mitigating the environmental impacts of plastic resin production are essential steps toward a more sustainable plastic industry. Embracing these practices not only benefits the environment but also aligns with increasing consumer demand for eco-friendly products.
Regulatory Framework and Industry Standards
Compliance with regulations and adherence to industry standards are paramount in ensuring the safety, quality, and environmental responsibility of plastic resin production. The regulatory landscape governs every aspect of the production process, from raw material extraction to final product disposal.
Regulatory Bodies
Several key regulatory bodies oversee plastic resin production:
- Environmental Protection Agency (EPA): Oversees environmental aspects of plastic production, ensuring compliance with pollution control standards and promoting sustainable practices.
- Food and Drug Administration (FDA): Regulates plastics used in food contact applications, ensuring that materials meet safety and health standards.
- Occupational Safety and Health Administration (OSHA): Ensures workplace safety in manufacturing facilities, protecting workers from chemical hazards and enforcing safety protocols.
Current Good Manufacturing Practices (cGMP)
Current Good Manufacturing Practices (cGMP) guidelines encompass quality assurance systems, contamination prevention, and process controls. Adherence to cGMP ensures consistent product quality and compliance with regulatory requirements, safeguarding both consumer safety and industry integrity.
International Standards
Global markets require compliance with international standards such as ISO certifications, which signify adherence to quality and safety norms. These standards facilitate international trade by ensuring that plastic resin products meet universally recognized criteria, enhancing marketability and consumer trust.
Understanding the regulatory landscape is crucial for manufacturers navigating compliance, enhancing product quality, and maintaining consumer trust. Adhering to these frameworks not only ensures legal compliance but also promotes responsible and sustainable plastic resin production.
Innovations in the Plastic Resin Industry
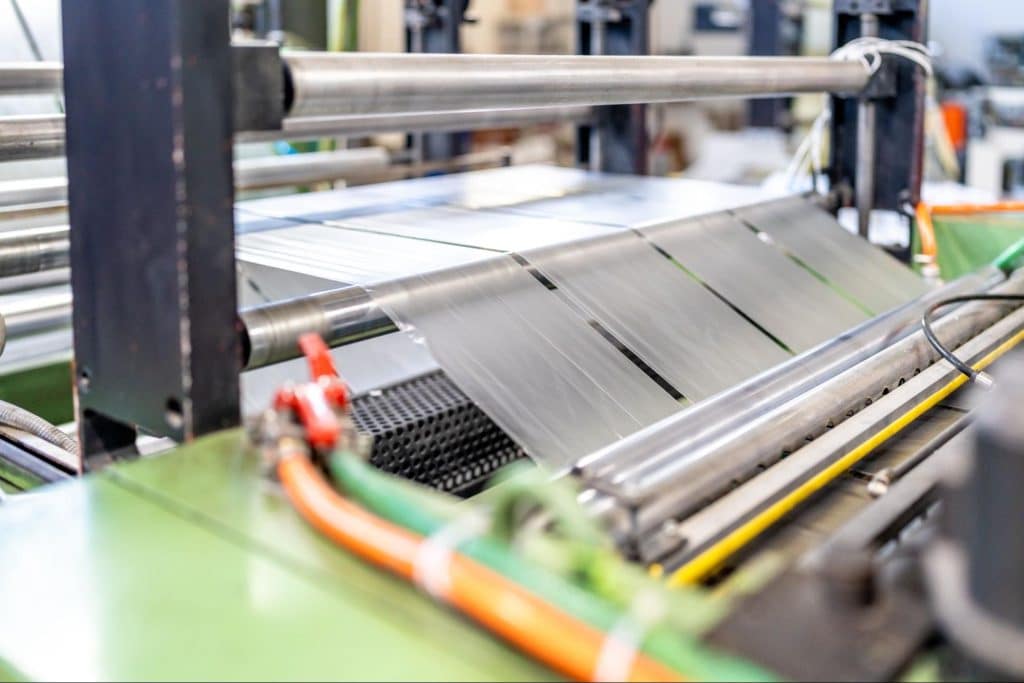
Technological advancements are revolutionizing plastic resin production, focusing on sustainability, efficiency, and performance. These innovations are essential for addressing environmental challenges and meeting the evolving demands of various industries.
Chemical Recycling Technologies
Innovations in chemical recycling enable the conversion of plastic waste back into monomers, supporting a circular economy. Processes like pyrolysis, solvent-based recycling, and hydrothermal processing break down plastics into their chemical components, which can then be repolymerized into new plastic resins. This approach reduces reliance on fossil fuels and minimizes plastic waste, contributing to more sustainable production practices.
Advanced Materials
- High-Performance Polymers: The development of materials such as Polyetheretherketone (PEEK) and polyimides offers superior properties for demanding applications in aerospace, electronics, and medical devices. These polymers are renowned for their heat resistance, mechanical strength, and chemical inertness.
- Smart Plastics: Integration of conductive polymers and nanotechnology results in smart plastics with enhanced functionality. These materials can exhibit properties like electrical conductivity, self-healing, and responsiveness to environmental stimuli, opening new avenues for innovative applications.
Automation and Industry 4.0
The adoption of automation and Industry 4.0 technologies improves manufacturing efficiency, reduces costs, and allows for greater customization in production processes. Smart manufacturing systems enable real-time monitoring, predictive maintenance, and flexible production lines, enhancing the overall productivity and adaptability of plastic resin production facilities.
Sustainable Materials
Investment in bioplastics and the use of renewable resources are driving the industry toward greener alternatives. Bioplastics derived from natural sources like starch, cellulose, and sugarcane offer biodegradable and compostable options that reduce environmental impact. Additionally, the incorporation of recycled materials into production processes lowers the demand for virgin plastics, promoting sustainability.
Embracing these innovations positions the plastic resin industry to meet future challenges and opportunities, balancing performance with sustainability.
Final Thoughts on Industry Trends and Sustainability Practices
Mastering plastic resin production requires an intricate comprehension of sophisticated chemical processes, material characteristics, and emerging technological innovations. As the industry progresses, it’s essential to strike a balance between the advanced demands of modern manufacturing and crucial environmental responsibilities.
To meet industry needs while lessening environmental impact, producers are called to prioritize sustainable methods, integrate cutting-edge innovations, and comply with regulatory benchmarks. Pioneering advancements, such as chemical recycling and the development of smart plastics, not only boost the functional performance of plastic resins but also chart a path toward a sustainable future.
For those involved in this constantly evolving domain, staying updated on the latest techniques and sustainability trends in plastic resin production is critical. To discover how Dallas Plastics can partner with you in achieving sustainable goals and innovative solutions in plastic resin production, reach out to our expert team today.