Ensuring superior adhesion of inks, coatings, and adhesives is essential in the plastic film manufacturing industry, serving as the foundation for the high product quality and performance that converters depend upon. Corona surface treatment has emerged as an essential technology in enhancing the surface energy of plastic films, thereby maximizing adhesion and reducing production waste. Understanding how corona surface treatment works and its benefits can significantly impact the efficiency and quality of your operations.
This comprehensive guide delves into the science behind corona surface treatment, its practical applications across various industries, and how it can elevate your manufacturing and converting processes. Whether you’re a converter seeking to improve product performance or a stakeholder in the medical, industrial, or food and beverage sectors, mastering corona surface treatment can offer you a competitive edge.
What Is Corona Surface Treatment?
Corona surface treatment is a process that alters the surface properties of plastic films to improve their adhesion characteristics. In the blown film manufacturing industry, achieving a surface that readily bonds with inks, coatings, and adhesives is crucial. Corona surface treatment enhances the surface energy of films, making them more receptive to these materials.
In plastic film production, particularly in blown film products, corona surface treatment is integrated into the production line to ensure that the films meet the necessary quality standards for subsequent converting processes. By treating the film surfaces, manufacturers can produce high-quality plastic films with improved adhesion properties, essential for various applications in the converting industry.
The Science Behind Corona Surface Treatment
At the molecular level, plastic films like polyethylene and polypropylene have chemically inert and non-porous surfaces with low surface energy. This nature makes them less receptive to bonding with other materials. Corona surface treatment modifies these surfaces through a phenomenon known as high-speed oxidation.
When a high-voltage electrical discharge—known as a corona discharge—is applied to the film’s surface, it ionizes the air around it. This ionization breaks molecular bonds on the film surface, creating free radicals. These free radicals react with oxygen, forming new polar groups on the surface. The introduction of these polar groups increases the film’s surface energy, enhancing its adhesion and wettability properties.
Corona Surface Treatment Components
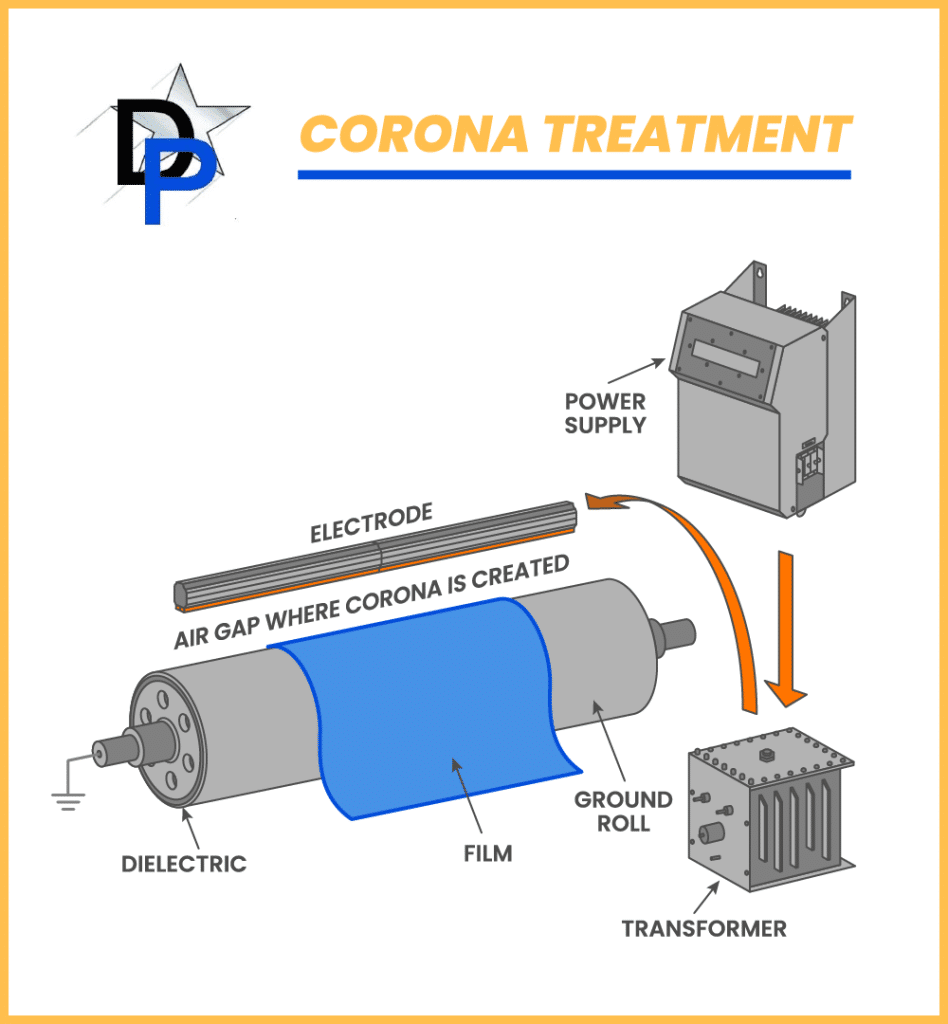
A typical corona surface treatment system comprises two primary components: Power Source & Treater Station
Power Source
The power source in a corona surface treatment system is responsible for converting standard electrical power into the high-frequency, high-voltage energy needed to create a corona discharge. This conversion is critical because the corona discharge requires a specific type of energy to ionize the air, which then interacts with the surface of the substrate.
Key Features:
- Frequency Conversion: Standard electrical power typically operates at a frequency of 50 or 60 Hz. The power source increases this frequency to a range between 10 kHz and 40 kHz, suitable for creating a stable and effective corona discharge.
- Voltage Transformation: The power must also be stepped up to a high voltage, often several kilovolts, depending on the treatment requirements. This high voltage is necessary to generate the electric field strong enough to ionize the air and create the corona.
- Control Systems: Modern power sources are equipped with control systems that allow operators to adjust the power level according to the specific material and treatment needs. This control ensures consistent treatment quality and energy efficiency.
- Safety Features: Given the high voltage involved, the power source is typically integrated with safety mechanisms to prevent accidental shocks or equipment damage. These might include circuit breakers, automatic shutdown in case of overload, and insulated enclosures.
Treater Station
The treater station is the physical setup where the actual corona treatment takes place. It houses the electrodes and the mechanism for passing the substrate (usually a film or sheet) through the treatment zone. This component is crucial for ensuring that the substrate is uniformly exposed to the corona discharge.
Key Features:
- Electrodes: These are critical for generating the electric field necessary for corona discharge. There are typically two types of electrodes used: active (connected to the high-voltage power source) and passive (usually grounded). The design of the electrodes can vary depending on the material being treated and the desired treatment intensity.
- Rollers: The rollers serve to guide and maintain the substrate in close proximity to the electrodes as it passes through the treatment area. They ensure that the substrate is steady and at the correct distance from the electrodes to achieve optimal treatment.
- Gap Control: Key to effective treatment is the precise control of the gap between the substrate and the electrodes. This gap determines the efficiency and effectiveness of the corona discharge, and adjustments may be necessary to accommodate different material thicknesses and compositions.
- Web Handling: The treater station includes a system for handling the substrate as it moves through the treatment process. This might include tension control systems, alignment features, and speed controls to ensure consistent treatment across the entire surface of the substrate.
- Cooling Systems: The process of corona treatment can generate heat, so cooling systems may be integrated into the treater station to dissipate excess heat and avoid thermal damage to the substrate or the treater components.
Understanding these components is essential for optimizing the corona surface treatment process and ensuring consistent quality in film production.
Corona Treatment Ground Roller Systems
Corona surface treatment systems are designed to cater to various operational needs. Two main ground roller systems are utilized:
Covered Roll Systems
In Covered Roll Systems, the dielectric material (an insulating layer) covers the ground roller, and the high-voltage electrode is exposed metal. This configuration is efficient for treating non-conductive materials and allows for adjustable treatment widths.
Advantages
- Highly efficient for non-conductive films.
- Adjustable treatment width and lane treatment capabilities.
- Suitable for a wide range of film widths.
- Ability to use various dielectric coverings based on specific needs.
Disadvantages
- Maintenance can be cumbersome due to the need to remove the roll for dielectric repairs.
- Larger physical size compared to bare roll systems.
- Not suitable for treating metallized films.
Bare Roll Systems
In Bare Roll Systems, the dielectric covers the high-voltage electrode, and the ground roller remains bare metal. This setup is compact and suitable for treating conductive materials like metallized films.
Advantages
- Ideal for treating metallized or conductive substrates.
- More compact design, saving space in production lines.
- Easier maintenance for electrode dielectric repairs.
Disadvantages
- Less efficient for non-conductive materials compared to covered roll systems.
- Limited ability to adjust treatment width.
- Requires more cooling due to higher operating temperatures.
Benefits of Corona Surface Treatment in Plastic Film Manufacturing
Corona surface treatment performed by blown film manufacturers like Dallas Plastics is crucial for converters because it significantly enhances the surface properties of plastic films. This treatment involves using a high-frequency electric discharge to increase the surface energy of the film, facilitating better adhesion of inks, coatings, and adhesives.
By altering the film surface at a molecular level, corona treatment ensures that the subsequent processes carried out by converters, such as printing and laminating, adhere more effectively and uniformly. This enhancement is vital for maintaining the quality, appearance, and functionality of the end products, meeting the high standards and diverse requirements of various industries reliant on these materials.
Request a Quote
Enhanced Adhesion and Wettability
By increasing the surface energy of plastic films, corona treatment enhances the adhesion of inks, coatings, and adhesives. This results in more vibrant printing, durable laminations, and a broader range of adhesives that can be effectively used.
Reduction of Production Waste
Corona surface treatment techniques are proven to reduce material waste by improving adhesion quality, minimizing risks like delamination and peeling, and thus reducing defects. Industry experts have observed that this reliability leads to cost savings by ensuring more efficient production runs.
Increased Quality Control
Consistent corona surface treatment allows manufacturers to maintain high-quality standards across production batches. The process ensures each film meets the necessary dyne level—a measure of surface energy—for optimal performance, facilitating quality assurance protocols.
Increased Product Lifespan
With improved bonding, the final products exhibit better durability and resistance to environmental factors, enhancing their shelf life and performance.
Productivity and Quality
Effective corona surface treatment reduces setup times and trial runs in converting operations. With predictable and reliable film surfaces, converters can operate at higher speeds without compromising quality, boosting overall productivity.
Versatility
The treatment makes films suitable for a wide range of applications across different industries, from packaging and labeling to automotive and medical uses.
Recent Technological Advancements in Corona Treatment
Technological innovations have propelled corona surface treatment systems to new levels of efficiency and integration.
Innovations in Equipment and Processes
Modern corona surface treatment systems are equipped with advanced features such as:
- Digital Control Systems: Allow precise adjustments of treatment parameters.
- Automated Electrode Positioning: Enhances safety and consistency.
- Improved Dielectric Materials: Extend equipment life and performance.
Integration with Digital and Automated Systems
Corona surface treatment systems now integrate seamlessly with automated production lines, enabling real-time monitoring and adjustments. This connectivity supports Industry 4.0 initiatives, promoting smarter manufacturing processes.
Role of Data Analytics
Data analytics in corona surface treatment allows for:
- Predictive Maintenance: Anticipating equipment servicing needs to minimize downtime.
- Quality Tracking: Monitoring treatment effectiveness to ensure consistent results.
- Process Optimization: Analyzing data to refine treatment parameters for optimal performance.
Practical Applications and Impacts on Various Sectors
Corona treatment of plastic films is particularly beneficial in several key industries, each leveraging the improved material characteristics for diverse applications.
Packaging Sector
In the packaging sector, corona treatment plays a pivotal role in meeting the demands for high-quality, functional, and visually appealing packaging solutions. Treated plastic films are used extensively for creating flexible packaging that can withstand rigorous handling and environmental stresses while maintaining the integrity of the printed graphics and information. This is crucial for attracting consumers and communicating brand values effectively. By improving the adhesion of labels and films, the treatment enables packaging manufacturers to meet diverse design and functionality requirements, ultimately leading to more reliable and sustainable packaging solutions.
Food and Beverage Industry
In the food and beverage industry, corona-treated plastic films are essential for ensuring product safety and legalities. The improved adhesion capabilities allow for the application of high-quality, vibrant, and detailed printed graphics, which are essential for ingredient disclosure, branding, and consumer engagement. This results in packaging that not only preserves the freshness and quality of its contents but also stands out on retail shelves. By utilizing corona-treated films, food and beverage manufacturers can create packaging that aligns with regulatory standards and consumer expectations.
Industrial Applications
Within the industrial sector, corona treatment is crucial for optimizing the performance and versatility of plastic films used in various applications. Treated films are employed as protective coatings and liners. This makes them suitable for use in harsh industrial environments where reliability and longevity are critical. Additionally, corona treatment allows for the use of plastic films in labeling and marking applications, ensuring that safety warnings, instructional labels, and product identifiers adhere securely and clearly to their surfaces. By improving the adhesion and functional properties of plastic films, the treatment supports the industrial sector in achieving higher efficiency, safety, and precision in its operations.
Enhancing Product Design and Customization
Corona surface treatment enables manufacturers and converters to offer customized solutions.
Tailored Treatments
By adjusting corona surface treatment parameters, films can be customized to meet unique customer requirements, such as specific dyne levels for particular inks or coatings.
Integration with Existing Production Lines
Corona treaters can be seamlessly integrated into existing production setups like blown film extrusion, enhancing capabilities without overhauling infrastructure.
Applications for Various Plastic Film Products
The versatility of corona surface treatment extends to numerous products:
Quality Assurance Through Corona Treatment
Maintaining high-quality standards is essential in plastic film manufacturing.
Ensuring High Standards for Surface Energy and Adhesion
Consistent corona surface treatment ensures that every film produced meets the required surface energy levels, supporting reliable adhesion in subsequent processes.
Importance of In-line and Pre-production Treatments
Combining treatments at the time of production with in-line treatments during converting maximizes adhesion properties and compensates for any surface energy degradation over time.
Adherence to Current Good Manufacturing Practices (cGMP)
Implementing corona surface treatment supports compliance with Current Good Manufacturing Practices (cGMP) by ensuring product consistency, quality, and safety, which is especially crucial in medical and food packaging sectors.
Maximize Efficiency and Product Performance Today
Corona surface treatment stands as a vital process in maximizing adhesion and enhancing the quality of plastic films. By understanding its science, applications, and benefits, manufacturers and converters can significantly improve their production efficiency, product performance, and competitiveness in the market.
At Dallas Plastics, we leverage over 35 years of expertise in blown film products to deliver high-quality films tailored to your specific needs. Our commitment to utilizing the latest technology ensures that our customers receive products that not only meet but exceed industry standards. Contact us today to discover how our solutions can elevate your operations and product offerings.