Quality control is a cornerstone of plastic film production, ensuring that final products meet the stringent standards required across various industries. Plastic film testing is essential for maintaining product consistency, safety, and compliance with industry regulations. In this comprehensive guide, we delve into the critical testing methods that underpin quality control in plastic film manufacturing, highlighting their significance and application.
Plastic Film Testing Methods
In the competitive landscape of plastic film production, maintaining high-quality standards is non-negotiable. Plastic film testing processes are vital for detecting defects, ensuring product reliability, and meeting customer expectations. Challenges such as material inconsistencies, equipment calibration issues, and evolving industry standards necessitate rigorous testing protocols. Adhering to established plastic film testing methods not only guarantees product safety but also enhances operational efficiency and market reputation. Additionally, advancements in plastic film testing technologies have enabled more precise and efficient quality assessments, further strengthening the role of testing in production.
The Role of Plastic Film Testing in Various Industries
Plastic films are utilized extensively across medical, food and beverage, and industrial sectors, each with specific quality requirements. Plastic film testing processes vary to accommodate these diverse needs:
- Medical Industry: Films used in medical applications require strict compliance with standards like ISO 10993, ensuring they are biocompatible and safe for use in various medical devices, as detailed by Genesis Medical Plastics.
- Food and Beverage Industry: Packaging films must preserve product freshness and prevent spoilage. Testing for oxygen transmission rate (OTR) and moisture transmission rate (MVTR) is critical to maintain the integrity of consumables.
- Industrial Applications: Durability and resistance to environmental factors are paramount. Mechanical testing assesses tensile strength and tear resistance to ensure films can withstand harsh conditions, according to JR Panel’s summary of common plastic characteristics.
By tailoring plastic film testing methods to industry-specific demands, manufacturers can produce films that meet precise performance criteria, thereby enhancing their suitability for each sector’s unique applications.
Essential Plastic Film Testing Methods
Implementing standardized plastic film testing methods is crucial for evaluating the physical and mechanical properties of plastic films. Here are the fundamental tests integral to quality control:
Tensile Strength Testing in Plastic Film Quality Control
Assessing tensile strength is vital for understanding a film’s ability to withstand stretching forces without breaking.
- Explanation and Importance: Tensile strength testing measures the force required to pull a film until it breaks. This test reveals the film’s durability and suitability for applications involving mechanical stress.
- Methodology: According to ASTM D882, a specimen is elongated at a constant rate, and the force and elongation are recorded until failure.
- Industry Application Example: Effective packaging that has undergone tensile strength testing can withstand impacts, vibrations, and compressive forces that occur in shipping, thereby reducing the risk of product loss (QualityMag).
Tear Resistance Testing in Plastic Film Quality Control
Tear resistance determines how well a film can resist the propagation of an existing tear.
- Testing Film Longevity: This test evaluates the film’s ability to withstand forces that could cause tears during handling and use, following the ASTM D1004 standard.
- Methodology: The standard procedure outlines that a notched specimen is subjected to force, measuring the tear resistance.
- Suitability for Diverse Applications: High tear resistance is essential for films used in heavy-duty packaging and industrial coverings.
Thickness Measurement in Plastic Film Quality Control
Uniform thickness is critical for consistent performance and aesthetics.
- Ensuring Uniformity: Variations in thickness can lead to weak points or excessive material use, affecting both quality and cost.
- Contemporary Measurement Techniques: Capacitance thickness gauges (ASTM D8136) provide precise measurements without damaging delicate films.
- Challenges in Meeting Specifications: Precise thickness measurements allow businesses to detect material discrepancies early in the production process, which helps in reducing scrap and promoting more efficient use of resources.
Optical Property Testing in Plastic Film Quality Control
Visual attributes such as clarity and gloss are important for consumer appeal and product information visibility.
- Importance in Packaging Applications: Clear films allow customers to view products, while appropriate opacity can protect contents from light exposure.
- Techniques for Evaluating Optical Properties: Haze meters and spectrophotometers measure light transmission and scattering to quantify clarity and gloss.
Heat Seal Strength Testing in Plastic Film Quality Control
Sealing integrity is essential for protective packaging.
- Relevance in Packaging: Heat seals must withstand mechanical stress and environmental conditions to keep products secure.
- Methodology: ASTM F88 measures the force required to peel a heat-sealed joint, indicating the seal’s strength.
- Industry Application Example: Manufacturers adopting advanced heat seal testing methodologies have extended the shelf life of perishable items by up to 30%, reducing food waste and enhancing safety (NCBI).
Advanced Plastic Film Testing Techniques for Enhanced Quality Control
Beyond basic tests, advanced plastic film testing methods provide deeper insights into material properties and performance.
FTIR (Fourier-Transform Infrared Spectroscopy)
- Assessing Chemical Properties: FTIR analyzes the molecular composition of films, identifying polymers and additives.
- Practical Benefits for Quality Assurance: FTIR detects contaminants, ensuring compliance with industry regulations and product safety.
DSC (Differential Scanning Calorimetry)
- Understanding Thermal Properties: DSC measures how a film’s heat flow changes with temperature, which is critical for understanding melting points and crystallization behavior of plastics.
WVTR and OTR Testing
- Assessing Barrier Properties: WVTR (ASTM F1249) and OTR (ASTM D3985) tests measure a film’s ability to prevent water vapor and oxygen transmission.
Other Sophisticated Testing Methodologies
- Surface Energy Testing: Determines a film’s wettability, important for printing and coating applications.
- Impact on Product Innovation: Advanced testing facilitates the development of films with specialized functions, such as antimicrobial surfaces or enhanced barrier properties.
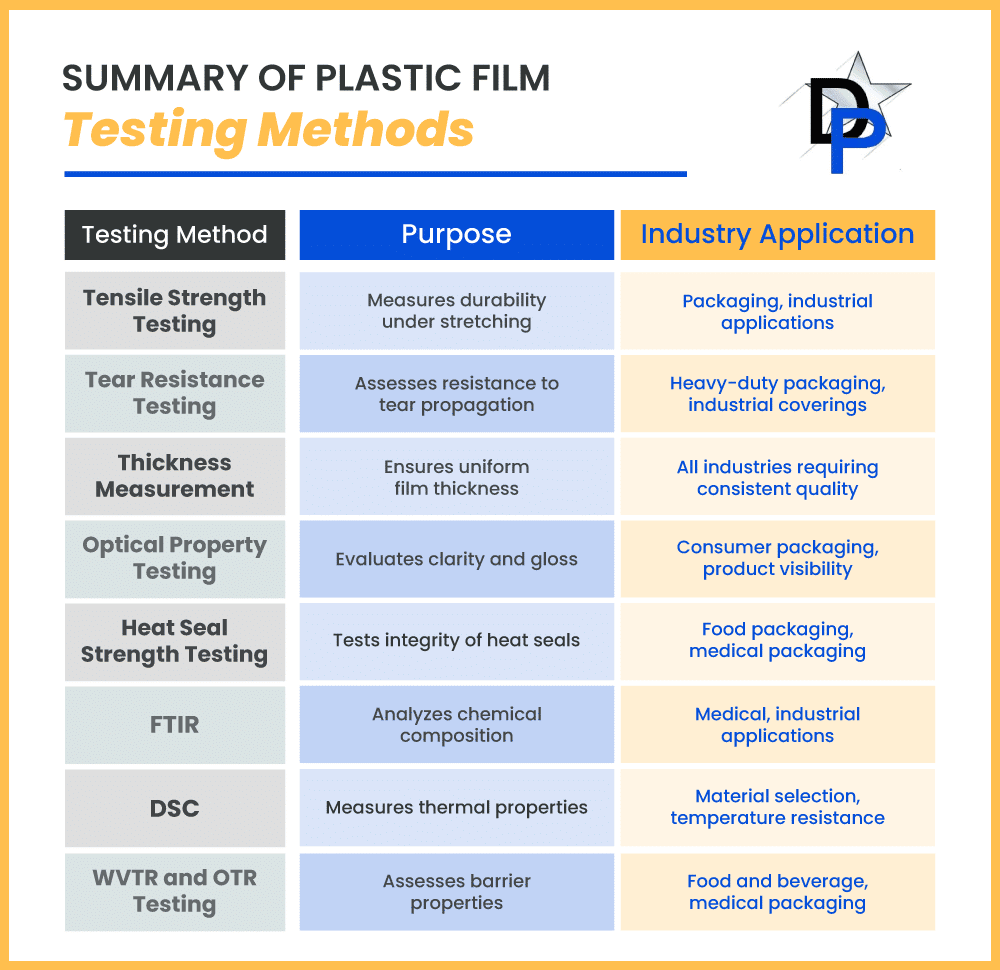
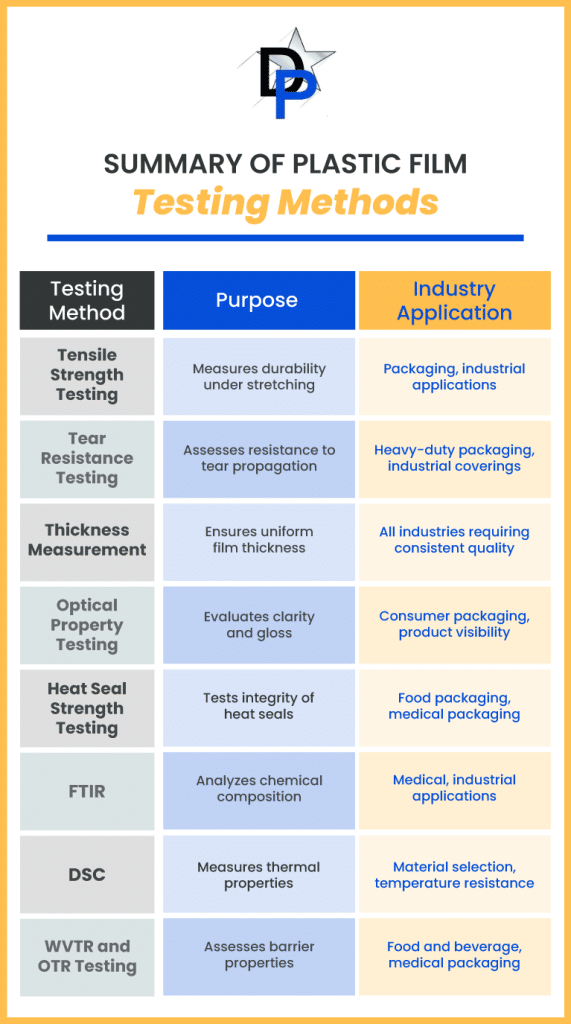
Compliance and Industry Standards in Plastic Film Testing
Adhering to industry standards ensures product safety and facilitates market acceptance.
- Key Industry Standards: Standards like ASTM emphasize testing procedures and performance criteria.
- Role of Routine Testing: Regular plastic film testing ensures ongoing compliance and identifies deviations before products reach the market.
- Benefits of Compliance: Meeting these standards not only ensures safety but also opens up global market opportunities, as many regions require adherence to international standards for product entry.
Challenges and Solutions in Plastic Film Testing
Quality control faces technical and operational challenges.
Common Technical Challenges
- Calibration Issues: Inaccurate equipment leads to unreliable test results.
- Equipment Maintenance: Regular maintenance is essential for accurate test results.
- Human Error: Manual testing is prone to human error, leading to unreliable results.
- Environmental Factors: Humidity, temperature, and other environmental conditions can affect test outcomes.
Operational Challenges
- Costs and Time Constraints: Testing can be expensive and time-consuming, limiting its frequency and accuracy.
- Lack of Standardization: Inconsistent testing procedures across testing environments can lead to unreliable results.
- Compliance and Regulatory Requirements: Meeting industry standards and compliance regulations can be complex and resource-intensive.
Practical Solutions and Best Practices
- Technology Adoption: Implementing automated plastic film testing systems reduces human error and increases efficiency.
- Standardized Procedures: Developing and adhering to standardized plastic film testing protocols minimize variability and improve consistency across testing environments.
Key Benefits of Effective Plastic Film Testing
Investing in comprehensive plastic film testing yields significant advantages.
- Enhancing Product Reliability: Consistent quality builds customer trust and brand reputation.
- Operational Efficiency and Cost Reduction: Early detection of defects minimizes waste and reduces production costs.
- Contribution to Innovation: Advanced plastic film testing enables the development of new materials and applications, driving industry growth.
- Regulatory Compliance and Market Access: Ensuring products meet regulatory standards allows for smoother entry into various markets, expanding business opportunities.
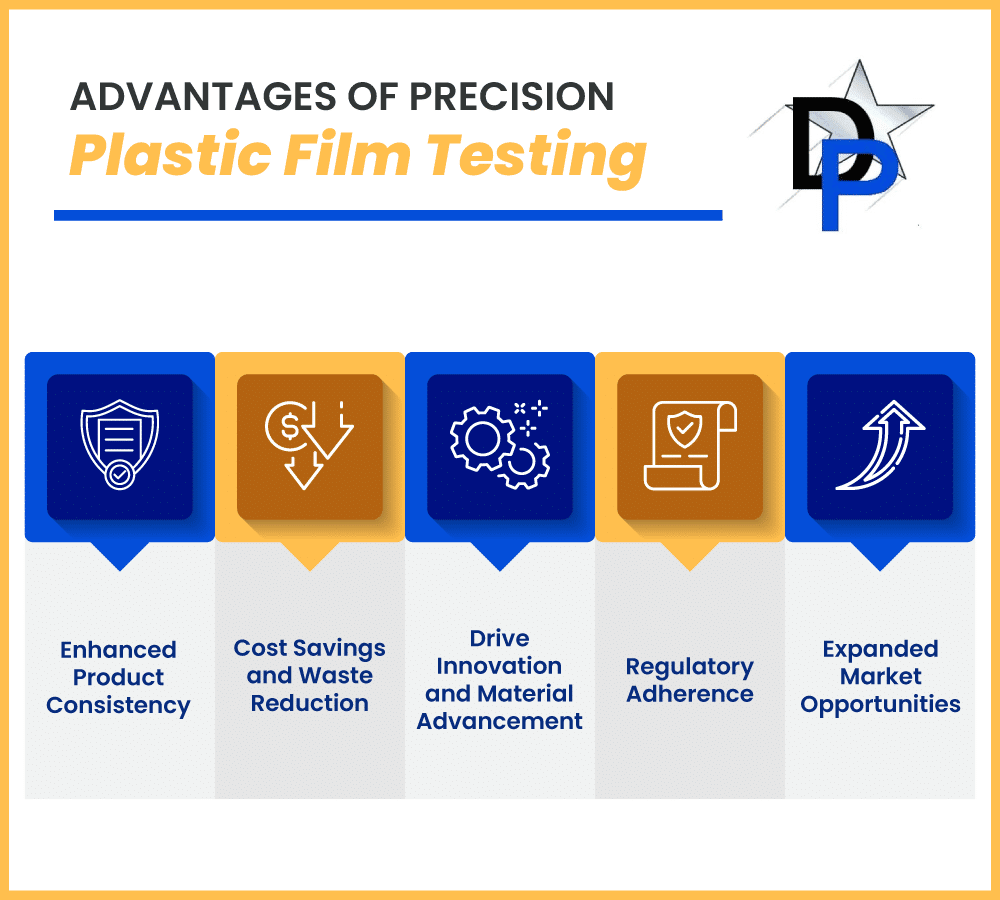
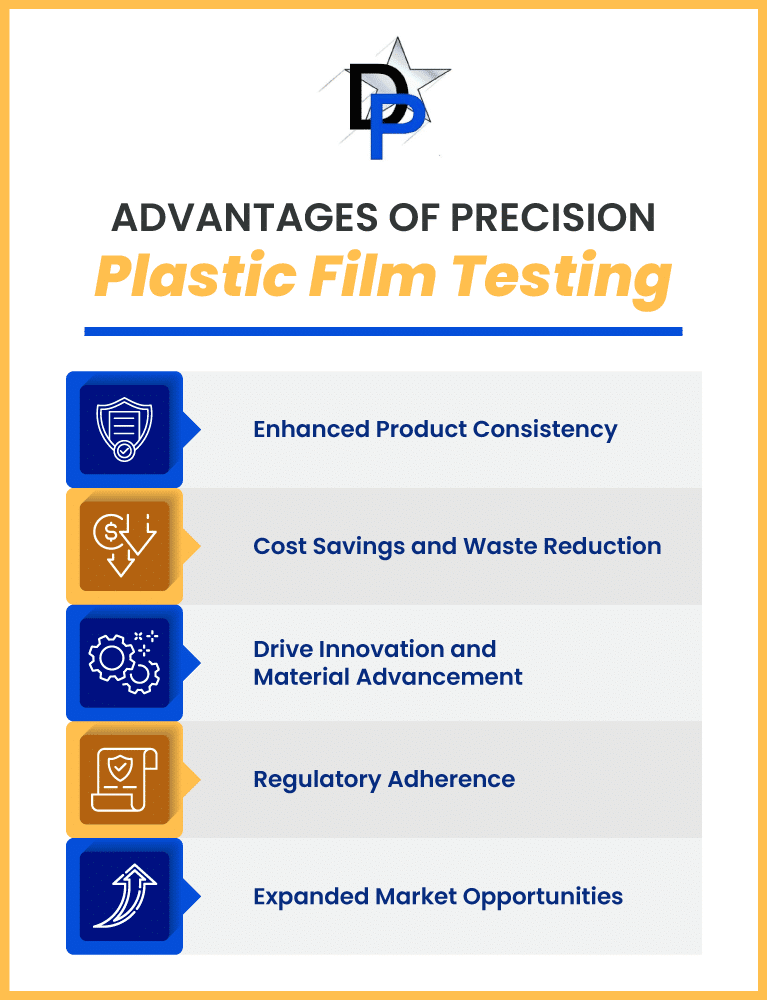
Wrap-Up: The Critical Role of Comprehensive Plastic Film Testing
Understanding and implementing essential plastic film testing methods are fundamental for maintaining quality control in manufacturing. From tensile strength and thickness measurement to advanced techniques like FTIR and DSC, plastic film testing ensures that films meet the rigorous demands of various industries. Adhering to standards and overcoming testing challenges safeguard product integrity, enhance customer satisfaction, and foster innovation.
As professionals in the field, prioritizing robust plastic film testing and staying abreast of evolving methodologies is essential. By committing to excellence in plastic film testing, your business can achieve unparalleled quality and market success.
Ready to enhance your plastic film quality control? Contact us today to learn more about our advanced testing solutions.