When it comes to packaging, choosing the right type of shrink wrap is crucial for ensuring product safety, compliance with industry standards, and cost-effectiveness. Shrink wrap, a plastic film that tightly secures products under heat application, comes in various materials, each with distinctive properties and advantages.
In this guide, we’ll delve into the specifics of PVC, Polyolefin, and Polyethylene shrink films, providing business owners, purchasing managers, and procurement specialists in the medical, food and beverage, and industrial sectors with the essential knowledge to make informed decisions.
By understanding the benefits and applications of each shrink wrap type, you can align your choices with your operational needs and sustainability goals, enhancing both product integrity and consumer satisfaction. Join us as we explore the diverse world of shrink film materials, their environmental impacts, and the latest innovations in the field.
Overview of Shrink Wrap Materials
Shrink wrap, also referred to as shrink film, plays a crucial role in the packaging industry, providing a protective cover that conforms to the item it encases, primarily used to secure and safeguard products during transportation and storage. This material is prized for its ability to tightly wrap objects of any size or shape, thus offering a versatile packaging solution across various sectors.
Traditionally, shrink wrap is used not only to hold products within a package but also to protect them from dust, moisture, and tampering, adapting well to the demands of numerous applications, from food packaging to bundling industrial goods or medical supplies.
Understanding the basic properties, importance, and distinct types of shrink wrap material—such as PVC, Polyolefin, and Polyethylene—can guide businesses in selecting the right packaging method to meet specific operational and environmental criteria, thus ensuring both product safety and consumer satisfaction.
Understanding PVC Shrink Wrap
PVC shrink wrap, or Polyvinyl Chloride, is known for its durability and versatility, making it a preferred material in a number of packaging applications. This section delves into the essential properties, common uses across different industries, and the advantages and limitations associated with PVC shrink wrap.
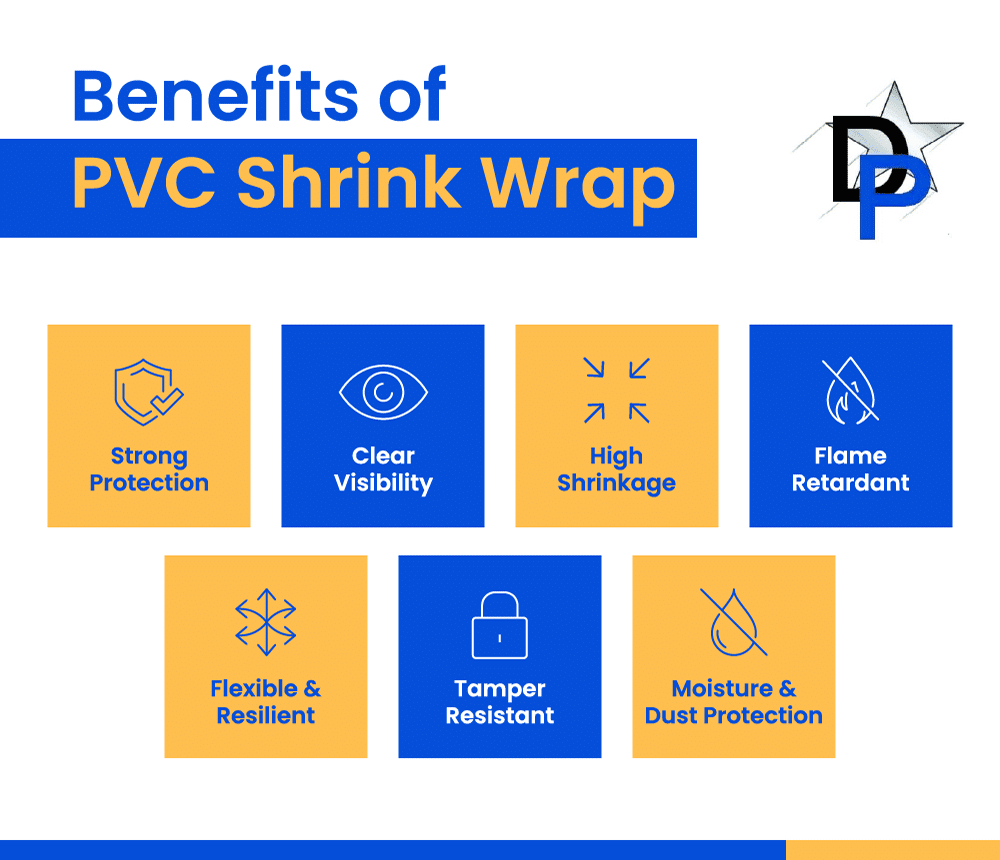
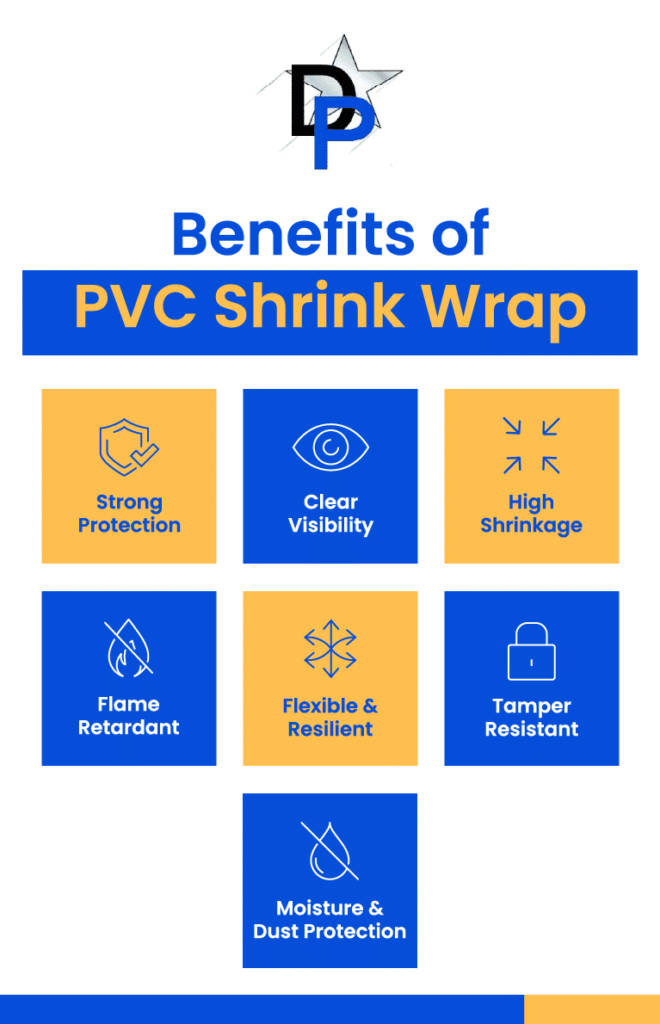
Properties of PVC Shrink Wrap
PVC is characterized by its strength and clarity, which ensure that the contents remain visible and well-protected. It has excellent shrinkage rates and inherent flame retardancy, which makes it suitable for a range of applications. Moreover, the material’s flexibility and resilience enable it to conform tightly to irregular shapes, providing a secure overwrap that resists tampering and protects against moisture and dust.
Common Uses in Various Industries
Due to its strong protective qualities, PVC shrink wrap is extensively used in the packaging of software, food items, cosmetics, and pharmaceuticals. Its ability to seal tightly makes it an excellent choice for retail packages that require a clear view of the product, enhancing visual appeal for consumer goods. Furthermore, the film’s ability to resist oil, grease, and chemicals makes it suitable for industrial applications where such exposures are common.
Advantages
The primary advantage of PVC shrink wrap is its cost-effectiveness, making it accessible for businesses looking to manage packaging costs while maintaining quality. The film is also easy to print on, which supports branding efforts without significant additional investment.
Limitations
However, there are environmental and health concerns associated with PVC shrink wrap, particularly related to the release of harmful compounds if burned.
Additionally, PVC is less breathable compared to other materials like Polyolefin, which can be a limitation when packaging food products that require air circulation. Prolonged use of PVC shrink wrap can contribute to environmental pollution, as the material’s disposal often leads to the release of dioxins and other toxic chemicals, harming both ecosystems and human health.
Potential exposure to vinyl chloride, a hazardous compound during the production and degradation of PVC, raises serious health concerns for workers and communities near production facilities.
Disclosure: Dallas Plastics does not produce PVC.
Characteristics of Polyolefin Shrink Wrap
Polyolefin shrink wrap has grown immensely popular in the packaging industry due to its versatility and exceptional properties, making it suitable for a plethora of applications. This type of shrink film is known for being strong, flexible, and food-safe, which has led to its widespread adoption, particularly in packaging consumable goods.
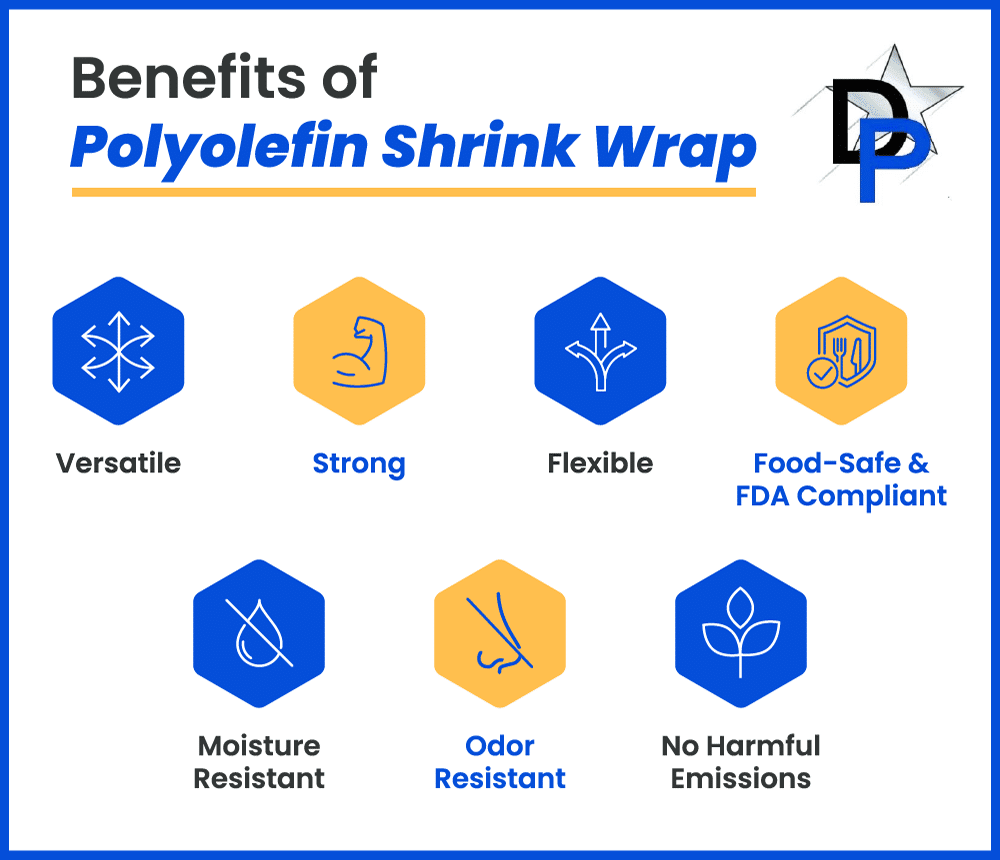
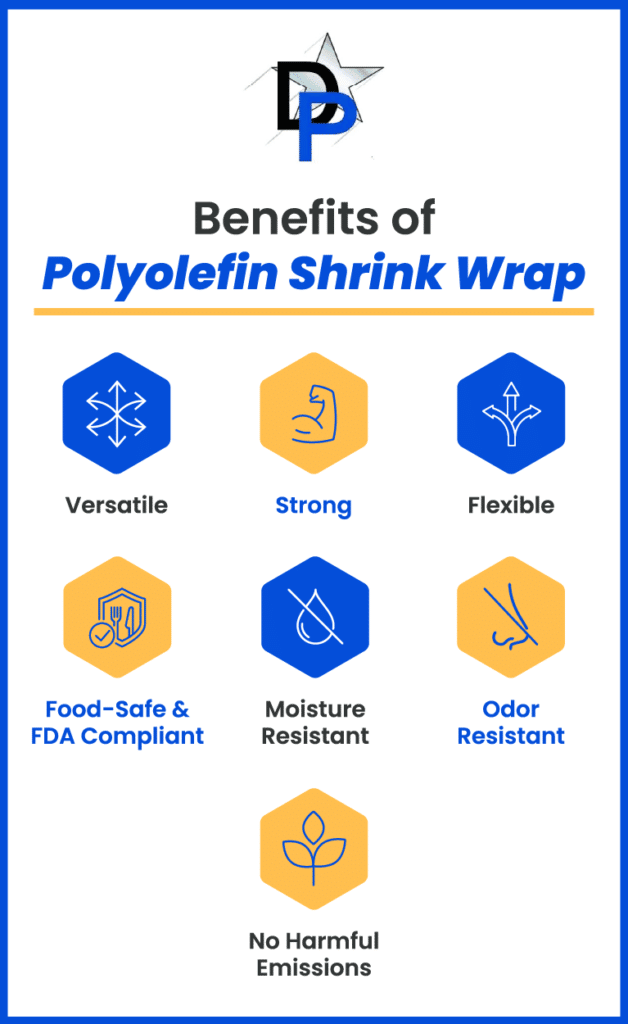
Distinctive Properties
Polyolefin is a category of thermoplastic polymers that includes both polyethylene (PE) and polypropylene (PP), each adding unique traits to the shrink wrap. These materials are known for their excellent clarity and gloss, providing aesthetically pleasing packaging. Additionally, polyolefin shrink wrap has a higher tensile strength compared to PVC, allowing it to keep a tight seal without compromising the integrity of the wrap even under stress.
Resistance to External Factors
One of the biggest advantages of polyolefin shrink wrap is its resistance to a variety of external factors such as moisture, dirt, and odors. This resistance makes it an ideal choice for food packaging where protection against contamination is essential. Additionally, it does not emit any harmful gasses during the sealing process, making it a safer choice for workers in packaging facilities.
Food Safety Compliance and Regulations
In terms of compliance, polyolefin shrink wrap meets numerous safety standards, making it favorable for food-related applications. It complies with FDA regulations for food contact, which ensures that food products remain safe from chemicals potentially leaching into the product. This compliance has solidified polyolefin’s role as a mainstay material within food-grade packaging applications.
By integrating these key characteristics, polyolefin shrink film provides a dependable and safe packaging solution, particularly important in industries adhering to stringent safety and quality standards. Whether for food, pharmaceuticals, or consumer goods, polyolefin shrink wrap stands out as a superior choice for businesses aiming to safeguard their products and ensure consumer satisfaction.
Exploring Polyethylene Shrink Wrap
Polyethylene shrink wrap is renowned for its robust characteristics, making it an ideal choice for industrial and heavy-duty packaging needs. This material is known for its substantial strength and durability, which ensures that it can withstand the rigors of transport and storage without compromising the integrity of the products it encases. Its resistance to punctures and tears helps in maintaining the protection of items through various logistical challenges.
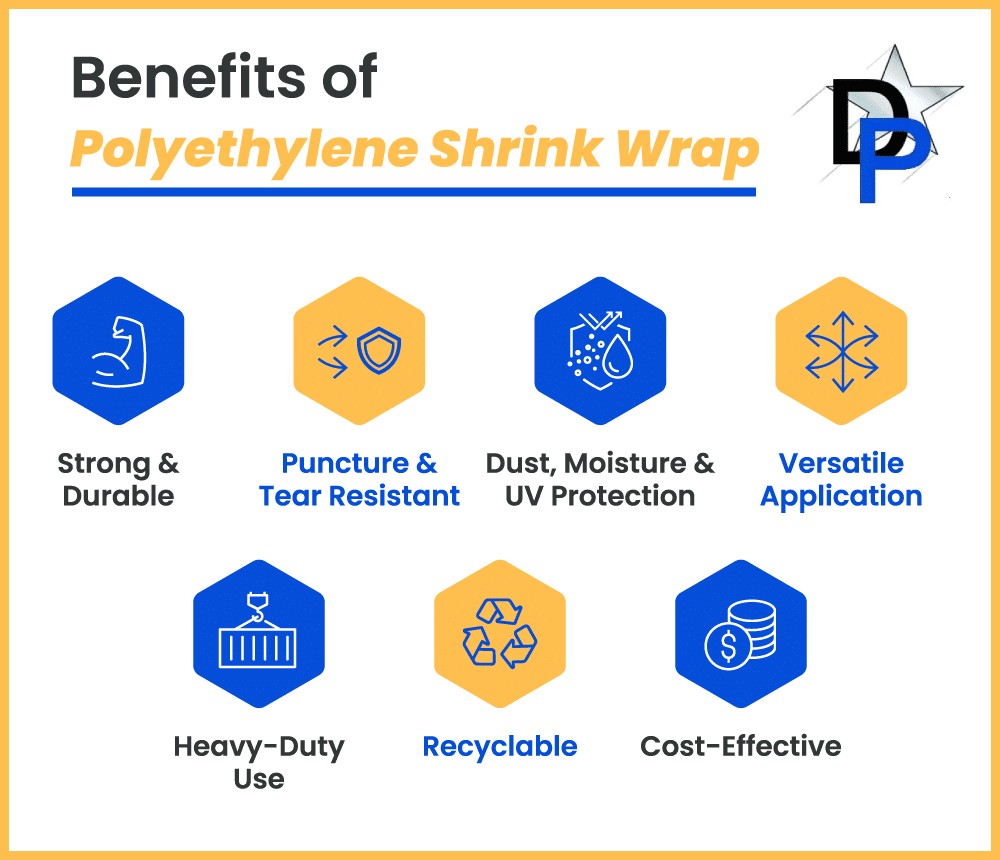
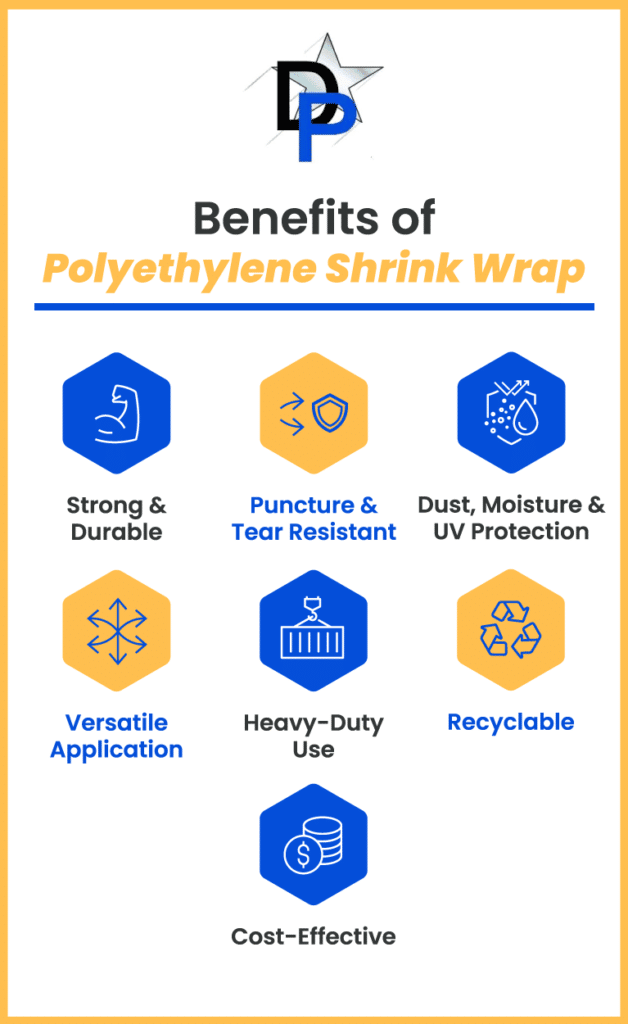
Key Properties of Polyethylene as a Shrink Wrap Material
Polyethylene shrink wrap is distinguished by its thickness and density, which contribute to its sturdy nature. This type of shrink film typically comes in thicker gauges, which delivers superior protection against external elements like dust, moisture, and UV radiation. Additionally, it is highly versatile in terms of application, lending itself well to irregularly shaped or large items that require a secure hold over extended periods.
Suitability for Industrial and Heavy-Duty Use
Given its heavy-duty characteristics, polyethylene shrink wrap is particularly suited for packaging large consumer goods, automotive parts, and building materials. It excels in applications where robustness and long-term durability are crucial. Moreover, polyethylene’s capacity to be recycled makes it attractive for businesses aiming to improve their environmental sustainability profiles without sacrificing packaging performance.
Cost-effectiveness and Environmental Impact
Opting for polyethylene shrink wrap can be economically advantageous, especially for companies dealing with bulk or large-scale industrial packaging. Its durability means fewer layers are needed compared to thinner materials, reducing the material usage per package and potentially lowering operational costs.
From an environmental perspective, polyethylene is less complex to recycle compared to other types of shrink wrap, which can help companies meet their sustainability commitments by minimizing waste and facilitating easier reprocessing into new products.
Making the Decision—Comparing These 3 Shrink Wrap Types
Shrink wrap plays an indispensable role in product packaging, offering protection and stability while maintaining a low cost and adaptability to various industry needs. Understanding the differences between PVC, Polyolefin, and Polyethylene shrink wraps in terms of durability, cost, and environmental impact can significantly aid businesses in choosing the right option for their specific needs.
Choosing the right type of shrink wrap involves balancing these aspects to meet both operational demands and financial budgets. Businesses must consider the specific attributes of each material and how these align with the nature of their products and overall environmental strategy. For instance, companies heavily focused on ecological impacts might favor Polyolefin over PVC, despite the cost difference, to align with their sustainability goals. Conversely, a small artisan shop might opt for PVC for its lower upfront costs and high clarity, which can enhance product appearance for immediate consumer appeal.
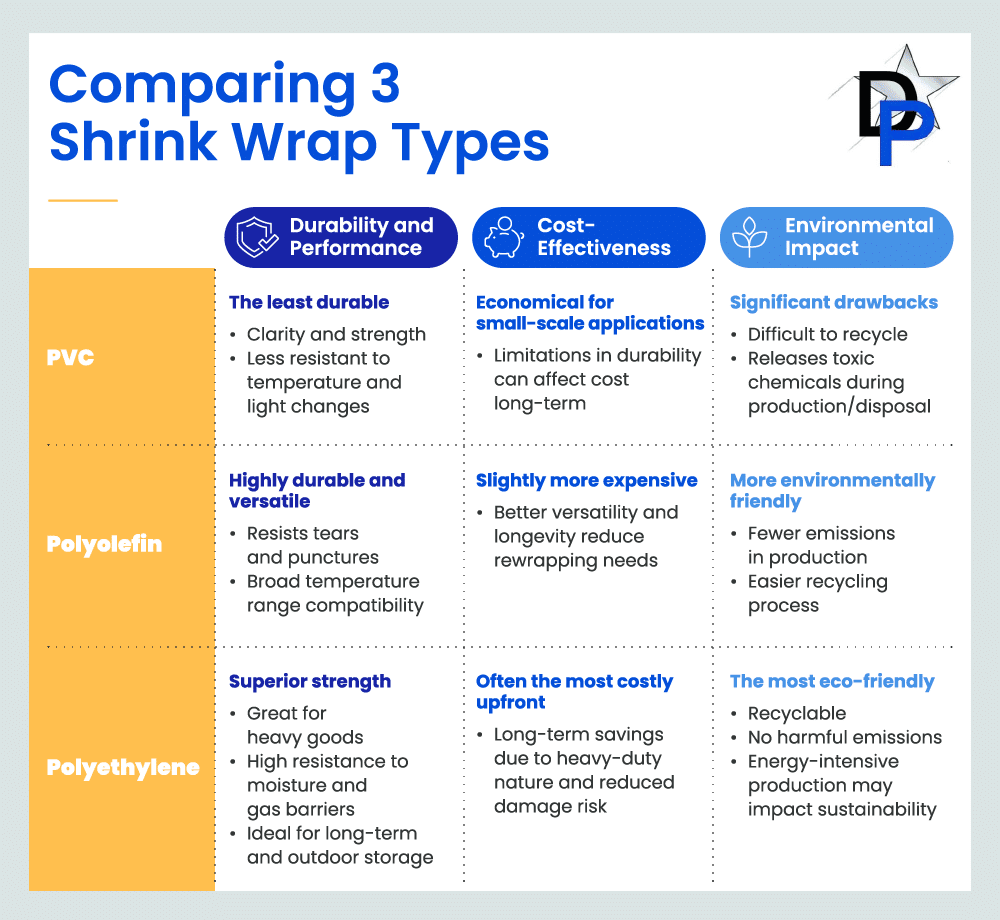
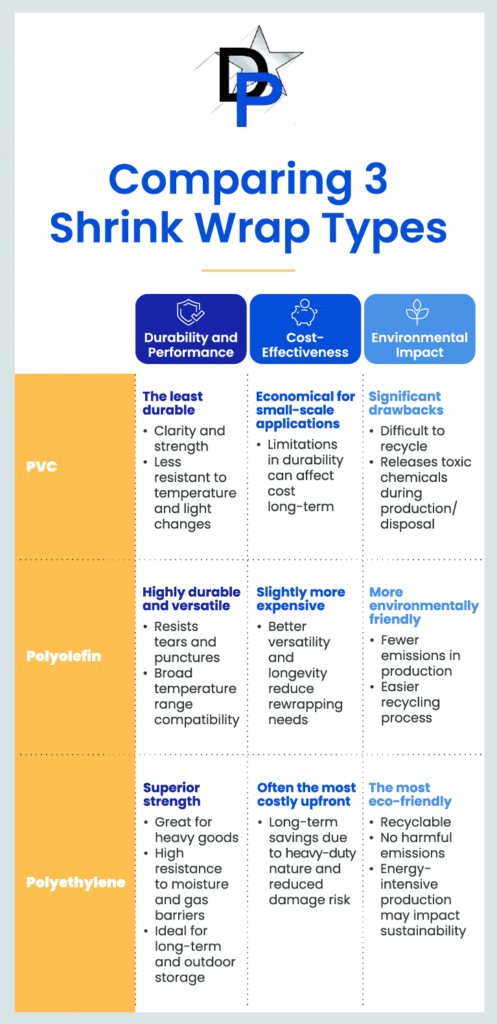
Innovations in Shrink Wrap Technology
Shrink wrap technology has seen significant advancements that have impacted everything from product safety to consumer satisfaction and environmental sustainability. Innovations in this field are instrumental in meeting the growing demands of scalability and efficiency within industries, ensuring that businesses can deliver high-quality protected products.
Recent Advancements in Shrink Wrap Materials
The development of advanced polymers and blending techniques has led to new types of shrink wrap that offer enhanced properties such as increased clarity, improved puncture resistance, and greater strength. For example, multi-layer shrink films have been developed to provide a barrier against moisture and oxygen, extending the shelf life of food products. Innovations in machine compatibility and processing speeds have also allowed for faster packaging operations, which can significantly reduce downtime and increase productivity.
Impact on Product Safety and Consumer Satisfaction
Advancements in shrink wrap technology not only preserve the integrity of the packaging but also protect the product from external contaminants, which is crucial in industries such as pharmaceuticals and food and beverage. Enhanced seal properties ensure that the packaging does not tear easily, reducing the risk of product tampering and leakage. These improvements in protective features significantly enhance consumer trust and satisfaction as they receive products in optimum condition.
Contributions to Sustainability Goals
The incorporation of biodegradable and recyclable materials in the manufacture of shrink wrap films is a remarkable innovation aiming at minimizing the environmental footprint of packaging wastes. Companies are increasingly adopting green practices by utilizing films made from recycled polyethylene or other biodegradable options. Furthermore, reduced thickness of new shrink films achieves lower material usage and waste, contributing to cost savings in material consumption and waste management.
Request a Quote
Request a Quote
Environmental Considerations and Compliance
Shrink wrap materials not only need to meet the demands of packaging and protection but also comply with environmental and regulatory standards. This section explores the sustainability profiles and compliance issues associated with PVC, Polyolefin, and Polyethylene shrink wraps, particularly focusing on their use in food-grade, medical, and industrial packaging.
Sustainability of Shrink Wrap Materials
- PVC Shrink Wrap: Known for its durability and clarity, PVC is less environmentally friendly due to the release of harmful compounds during production and disposal. Efforts to recycle PVC are ongoing, but its biodegradability remains low.
- Polyolefin Shrink Wrap: This material stands out for its lower environmental impact compared to PVC. Polyolefin is non-toxic and recyclable, making it a preferable option for businesses aiming for operational sustainability.
- Polyethylene Shrink Wrap: With a high recycle rate among plastics, polyethylene is favored for its minimal environmental footprint. It is also known for being highly durable, which reduces the need for frequent replacement and thus lessens waste.
Compliance with Industry Regulations
Regulatory compliance is crucial for selecting appropriate shrink film materials, especially in sectors with stringent standards such as food and medical industries.
- Food-Grade Compliance: All three types of shrink wraps can be manufactured to meet FDA standards for food contact. However, polyolefin and polyethylene are often preferred due to their lack of toxic additives.
- Medical Sector Standards: In the medical field, shrink wrap must not only prevent contamination but also comply with health and safety regulations. Polyolefin, due to its high clarity and puncture resistance, is frequently used for sterile medical packaging.
- Industrial Usage: For industrial applications, the strength and durability of the shrink wrap are paramount. Polyethylene, being strong and resistant to punctures, aligns well with industrial needs and meets the necessary safety standards.
Understanding these environmental considerations and compliance requirements is essential for businesses in making informed decisions about which shrink wrap material aligns best with their product needs and sustainability goals. By choosing eco-friendly and compliant materials, companies can enhance their brand reputation and contribute to a safer environment.
Selecting the Right Shrink Film for Your Needs
When deciding which shrink film material best fits your company’s specific needs, several factors should be carefully considered. These include the nature of the products you are packaging, operational requirements, and compliance with applicable industry standards. Here’s a guide to help you navigate through the selection process effectively.
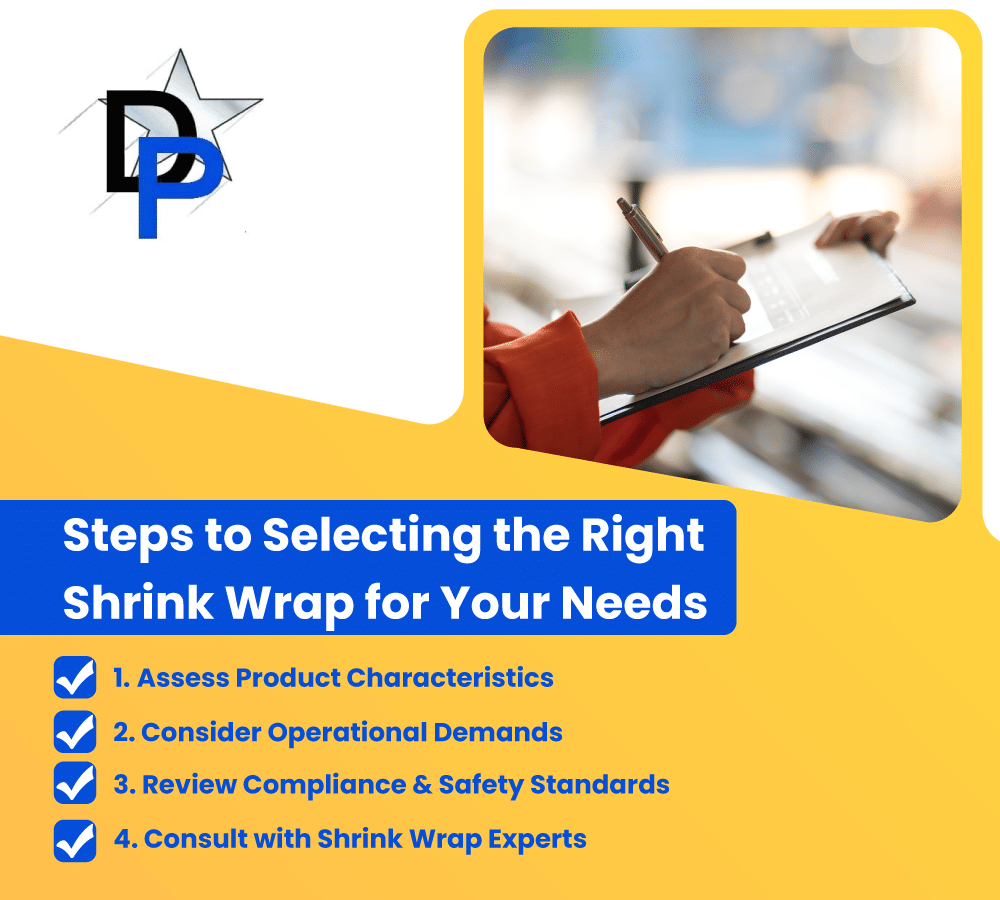
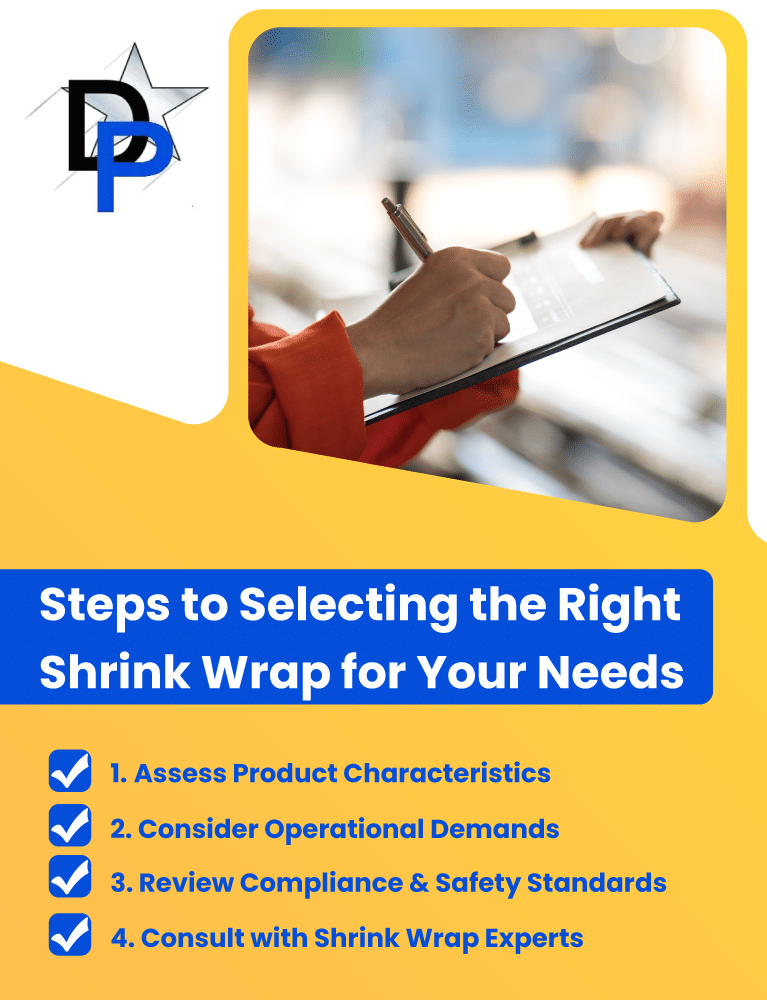
Step 1: Assess Product Characteristics
Begin by evaluating the characteristics and requirements of the product to be wrapped. Consider aspects such as:
- Size and Shape: Larger or irregularly shaped items might need more durable shrink film like polyethylene.
- Sensitivity: For sensitive products, especially in the food and medical sectors, consider polyolefin for its lower shrink force and absence of chlorine, which makes it safer and compliant with stringent regulations.
Step 2: Consider Operational Demands
The operational context in which the shrink wrap will be applied is crucial. Reflect on:
- Volume of Packaging: High-volume operations may benefit from materials that are quick and easy to wrap, such as PVC which has excellent machinability.
- Equipment Compatibility: Ensure the shrink film you choose is compatible with your existing machinery to maintain efficiency and reduce costs.
Step 3: Review Compliance and Safety Standards
Compliance with industry regulations cannot be overlooked. Each sector has its standards and requirements that influence the choice of shrink wrap:
- Food Packaging: Requires food-grade shrink wrap, often necessitating the use of polyolefin due to its FDA approval for direct food contact.
- Medical Products: Typically demands high-barrier properties to ensure sterility, making polyolefin and polyethylene preferred options due to their strong barrier qualities against moisture and contaminants.
Step 4: Consult with Shrink Wrap Experts
After considering the above factors, it might still be beneficial to consult with shrink wrap specialists. Experts can offer insights into:
- Latest Material Technologies: They can advise on the latest advancements in shrink film materials that could enhance your packaging’s performance.
- Custom Solutions: If standard shrink wrap options do not perfectly meet your needs, a custom solution may be necessary. This could include specific thicknesses, enhanced UV protection, or specialized additives for improved strength.
Engaging with Dallas Plastics for Custom Solutions
Optimizing your packaging solution can be critical to the success of your product, and engaging with a leader in the industry like Dallas Plastics can provide you with the high-quality materials and customized solutions you need. Known for their blown film products and expertise in polyvinyl chloride (PVC), polyolefin, and polyethylene shrink films, Dallas Plastics stands ready to address complex packaging challenges with tailor-made options.
Whether you’re packaging perishable foods, sensitive medical equipment, or robust industrial goods, Dallas Plastics has the capabilities to create custom shrink wrap solutions designed for your product’s specific requirements. Leveraging years of industry experience and a deep understanding of film properties, they work closely with clients to develop films that meet essential criteria, such as durability, clarity, and resistance to various environmental stresses.
Advantages of Choosing Dallas Plastics
- Material Precision: Products are crafted precisely to the specifications required for your product’s safety and appeal, ensuring perfect fit and protection.
- Innovative Technology: Utilization of the latest technologies in plastic film production that contribute to enhanced product safety and customer satisfaction.
- Regulatory Compliance: Assistance in navigating the complex regulatory environment to ensure that your packaging complies with relevant standards and laws, particularly in sensitive areas like food-grade and medical packaging.
By choosing Dallas Plastics as your shrink film provider, you also gain a strategic partner who is invested in your success. This partnership goes beyond just providing products; it fosters innovation, sustainability, and operational efficiency. Moreover, Dallas Plastics is committed to ongoing research and development, continuously advancing their technology to meet emerging market demands and environmental guidelines.
Partner with Dallas Plastics for Innovative, Sustainable Shrink Film Solutions
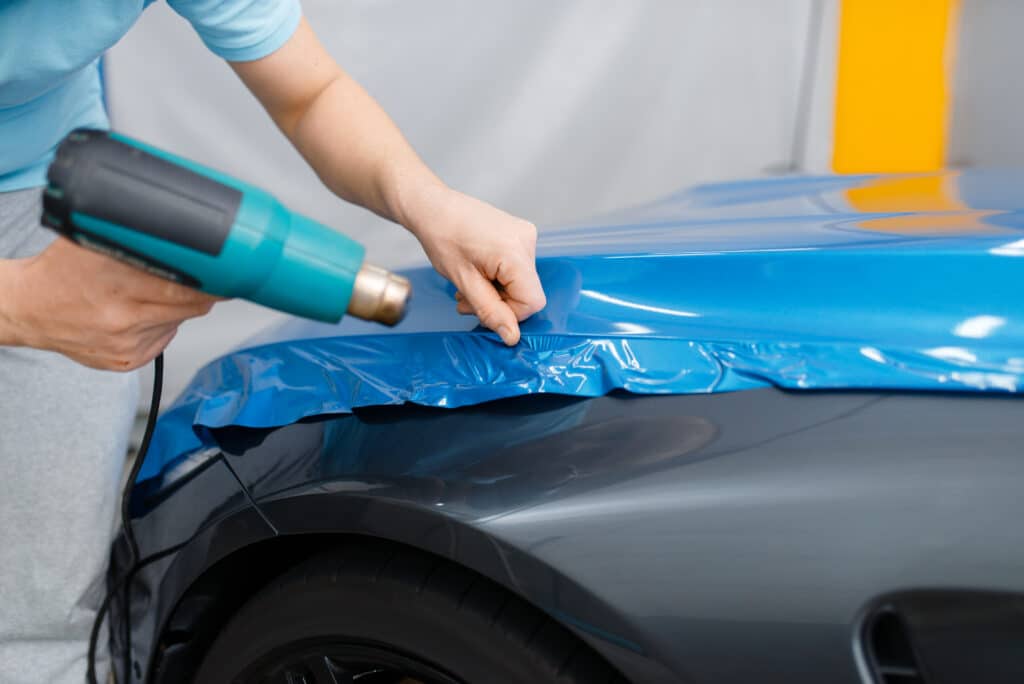
Choosing the right shrink film for your product packaging is crucial, not only for the protection and longevity of your products but also for aligning with industry standards and environmental considerations. At Dallas Plastics, we understand these requirements intimately and are equipped to provide you with the highest-quality, most suitable plastic film solutions tailored to your specific needs.
Whether you are in the medical, food and beverage, or industrial sectors, our team of experts is ready to assist you in selecting from our extensive range of PVC, Polyolefin, and Polyethylene shrink films Our commitment to innovation and quality ensures that you receive the most advanced and reliable packaging solutions available.
Let’s discuss how we can support your business’s unique packaging challenges and sustainability goals. Contact us today to learn more about our custom shrink film solutions and how we can help enhance the safety, efficiency, and environmental footprint of your packaging processes.